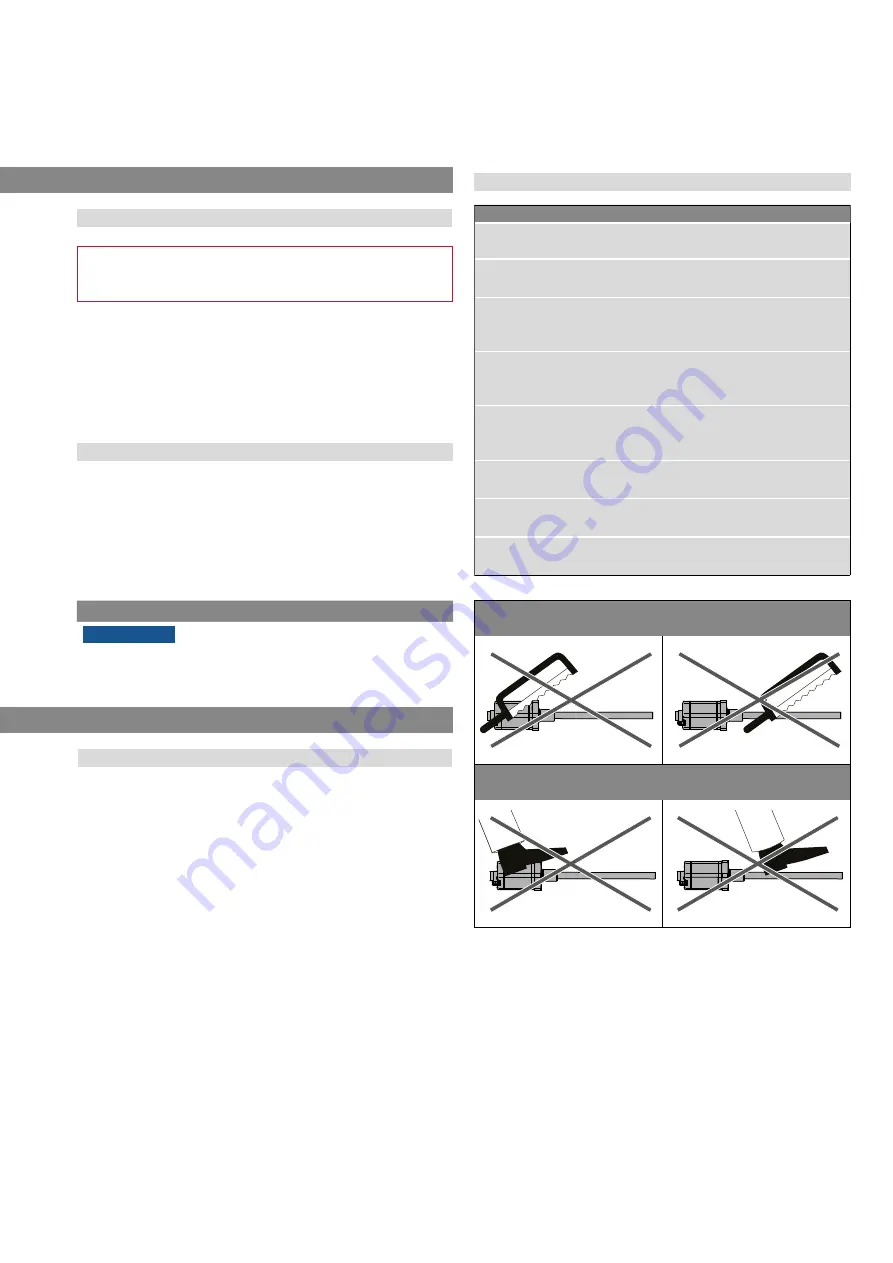
Temposonics
®
R-Series
V
SSI
Operation Manual
I 3 I
1. Introduction
1.1 Purpose and use of this manual
Before starting the operation of Temposonics
®
position sensors,
read this documentation thoroughly and follow the safety
information. Keep this manual for future reference!
1/
The term “qualified technical personnel” characterizes persons who:
• are familiar with the safety concepts of automation technology applicable to the
particular project
• are competent in the field of electromagnetic compatibility (EMC)
2. Safety instructions
2.1 Intended use
This product may be used only for the applications defined under item
1 and only in conjunction with the third-party devices and components
recommended or approved by MTS Sensors. As a prerequsite of prop-
er and safe operation the product requires correct transport, storage,
mounting and commissioning and must be operat ed with utmost care.
1. The sensor systems of all Temposonics
®
series are intended
exclu sively for measurement tasks encountered in industrial,
commercial and laboratory applications. The sensors are
considered as system accessories and must be connected
to suitable evaluation electron ics, e.g. a PLC, IPC, indicator
or other electronic control unit.
Foreseeable misuse
Consequence
Wrong sensor connection
The sensor will not work
properly or can be damaged
Operate the sensor out of the
operating temperature range
No signal output –
the sensor can be damaged
Power supply is out of the
defi ned range
Signal output is wrong/
no signal output/
the sensor will be damaged
Position measurement is
infl uenced by an external
magnetic fi eld
Signal output is wrong
Cables are damaged
Short circuit – the sensor can
be damaged/sensor does not
respond
Spacers are missing/
installed in a wrong order
Error in position measurement
Wrong connection
of ground/shield
Signal output is disturbed –
the electronics can be damaged
Use of a magnet that is not
specifi ed by MTS Sensors
Error in position measurement
Do not alter the sensor afterwards.
The sensor might be damaged.
Do not step on the sensor.
The sensor might be damaged.
2.2 Foreseeable misuse
The content of this technical documentation and of its appendices is
intended to provide information on mounting, installation and com-
missioning by qualified automation personnel
1
or instructed service
technicians who are familiar with the project planning and dealing with
Temposonics
®
sensors.
1.2 Used symbols and warnings
Warnings are intended for your personal safety and for avoidance
of damage to the described product or connected devices. In this
documentation, safety information and warnings to avoid danger
that might affect the life and health of operating or service personnel
or cause material damage are highlighted by the pictogram defined
below.
Symbol
Meaning
NOTICE
This symbol is used to point to situations
that may lead to material damage, but not
to personal injury.
• have received adequate training for commissioning and service operations
• are familiar with the operation of the device and know the information required for
correct operation provided in the product documentation