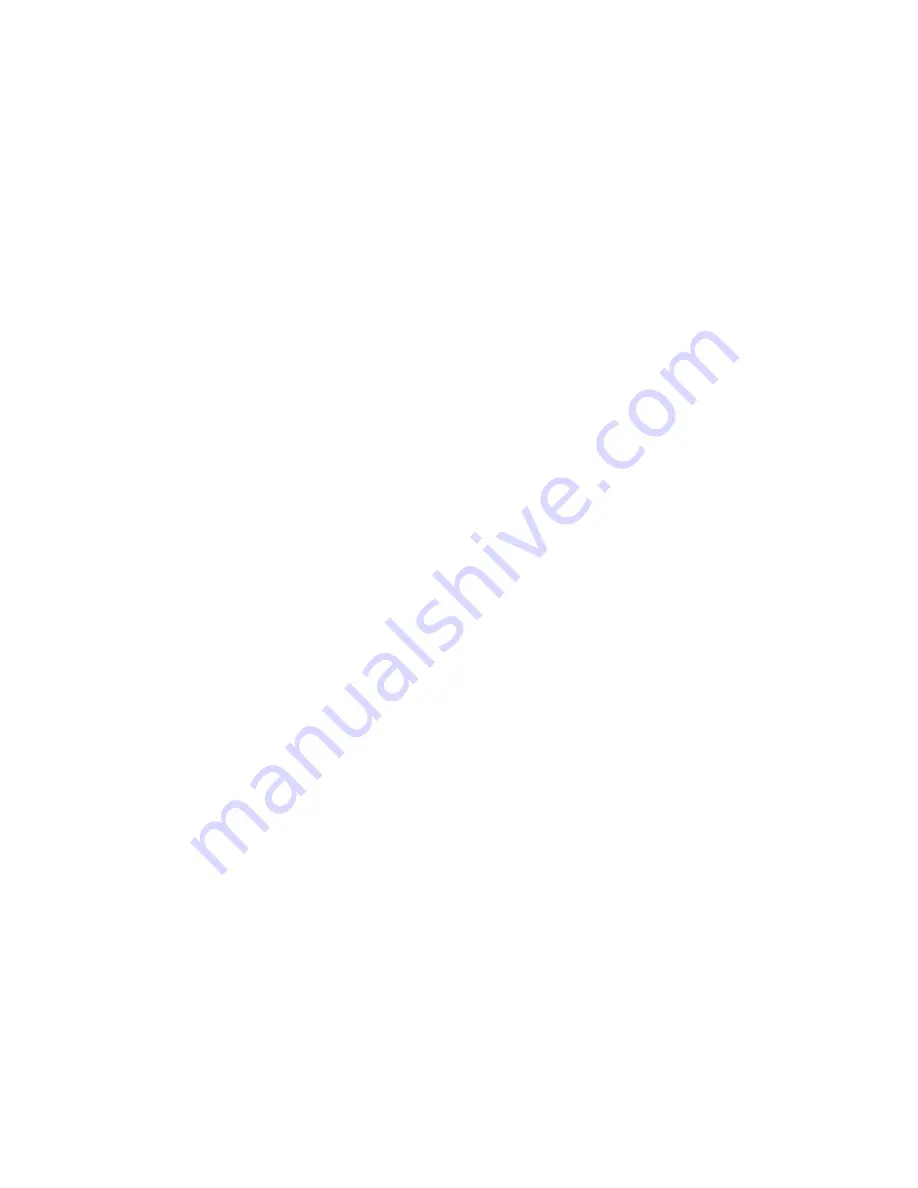
1. The seal seat (#125) must be
installed in the motor bracket (#1)
before the bracket is installed on the
motor. To install the seat:
a. Place the motor bracket face up
on a fl at surface.
b. Apply a coating of compatible
lubricant to the elastomer portion
of the seat to aid with installation.
c. Carefully press the seat, smooth
side up, into the seat cavity of
the motor bracket. Thumb
pressure is usually suffi cient to
install the seat.
2. Install the motor bracket. This is
best done with the motor standing
on end. Make sure that both the
"C"-face of the motor and the feet of
the motor bracket are clean. Slide
the motor bracket over the shaft onto
the motor.
3. Install the rotating element (#12).
Lubricate I.D. of the rotating element
. Place the rotating element on the
shaft with the carbon end towards
the seat. Place the spring over the
shaft, with the backing plate up and
compress the spring to locate the
rotating element against the seat. If
this fails to seat the rotating element
gently push the rotating element
down with a thin blade screwdriver
being careful not to damage the seat
or the rotating element.
4. Compress and hold the seal spring
slightly below the snap ring groove
and install the snap ring (#4). Make
sure the snap ring is locked in the
groove.
5. Install the impeller key (#23) into the
shaft keyway.
6. The impeller is a slip fi t and should
slide on fi rmly but easily until it stops
against the impeller wearing sur-
face. Force should not be required
or used to install the impeller in the
correct position. The impeller hub
should be facing out away from the
motor bracket. Refer to Figure 5-2.
7. Next, rotate the impeller by hand,
the impeller should move freely.
8. Place the large “O” ring (#7) into the
outside “O” ring groove in the motor
bracket. Place the two (2) smaller
"O" rings (#8) into the smaller "O"
ring grooves.
9. Place the cover (#2) over the motor
bracket and install the four (4) M6-1
X 80mm bolts (#19). Tighten the
bolts systematically, alternating
diagonally across the cover. DO
NOT exceed 7-11 ft. lbs. of torque or
damage to the motor "C"-face may
occur.
5E Testing and Final Adjustment
The pump is now ready for installation.
Final adjustments will be made with the
pump in operation.
1. Connect all piping and fi ll the pump
with fl uid.
2. Reconnect the electrical connec-
tions, referring to the colored or
numbered tape used to mark the
wires.
3. Make sure all valves are opened,
and fl uid will fl ow through the sys-
tem.
4. Start the pump and make the fi nal
adjustments to the M6 bolts holding
the cover on. These nuts and bolts
must be torqued to about 7-11 ft.
lbs. to obtain proper performance.
5. Check for leaks on pump and piping.
Special attention
should be
given to the seal area at the rear
opening in the motor bracket.
6. Under pressure, the impeller will fi nd
its “hydraulic” balance.
7. Using an amprobe or similar device,
check for motor overload.
8. While the impeller is seating, it
is common to experience some
variance in readings. After a run-in
period the readings should level off.
This completes the adjustment and
testing phase. The pump is ready for
service.
Page 510