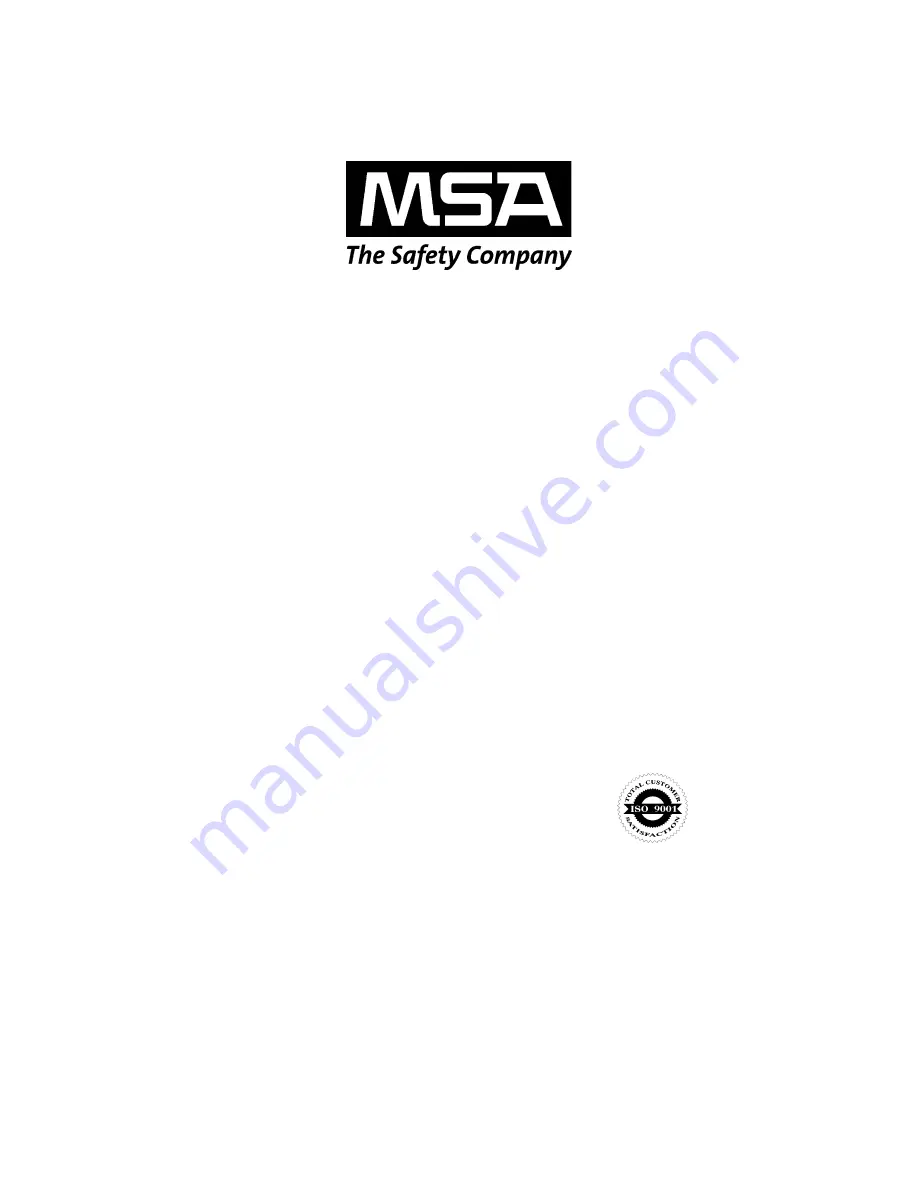
The information and technical data disclosed in
this document may be used and disseminated
only for the purposes and to the extent
specifically authorized in writing by MSA.
Instruction Manual 04-14
MSA reserves the right to change published
specifications and designs without prior notice.
MANMOS5
Part
No.
MANMOS5
Revision
1
Ultima® MOS-5
Intelligent Sensor for
Hydrogen Sulfide Gas Detection