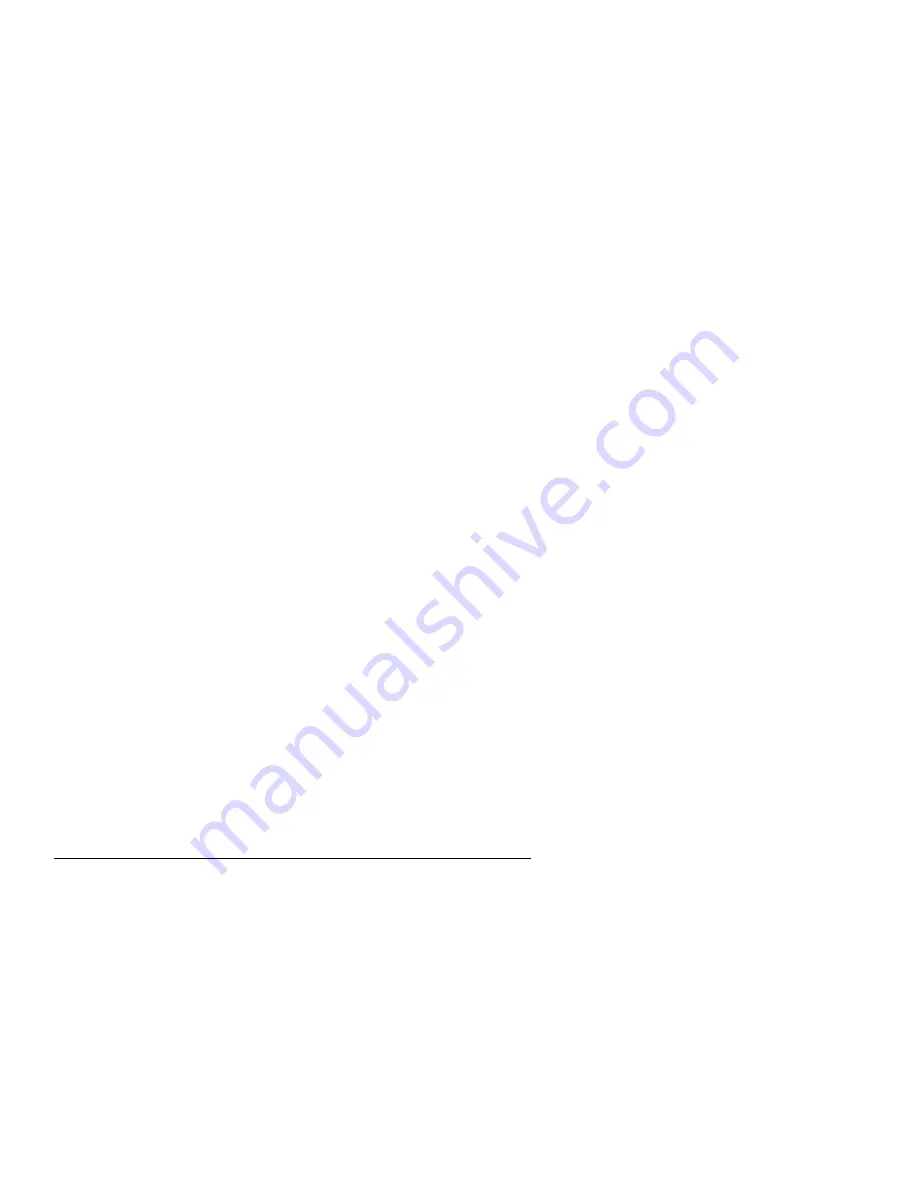
ii
Limited Warranty
LIMITED WARRANTY
Moyer Diebel. (herein referred to as The Company), 3765 Champion Blvd., Winston-Salem, North Carolina 27105, and
2674 N. Service Road, Jordan Station, Canada, L0R 1S0, warrants machines, and parts, as set out below.
Warranty of Machines:
The Company warrants all new machines of its manufacture bearing the name "Moyer Diebel"
and installed within the United States and Canada to be free from defects in material and workmanship for a period of one
(1) year after the date of installation or fifteen (15) months after the date of shipment by The Company, whichever occurs first.
[See below for special provisions relating to glasswashers.] Warranty registration must be submitted to Moyer Diebel within
ten (10) days after installation either online on the Moyer Diebel website (http://www.moyerdiebel.com/service/) for the USA
or http://www.championindustries.com/warranty-registration for Canada or by fax on the form provided in the front of this
manual. If warranty registration is not returned to The Company within such period, the warranty will expire after one year from
the date of shipment. The Company will not assume any responsibility for extra costs for installation in any area where there are
jurisdictional problems with local trades or unions. If a defect in workmanship or material is found to exist within the warranty
period, The Company, at its election, will either repair or replace the defective machine or accept return of the machine for full
credit; provided; however, as to glasswashers, The Company's obligation with respect to labor associated with any repairs shall
end (a) 120 days after shipment, or (b) 90 days after installation, whichever occurs first. In the event that Moyer Diebel elects
to repair, the labor and work to be performed in connection with the warranty shall be done during regular working hours by
The Company's authorized service technician. Defective parts become the property of The Company. Use of replacement parts
not authorized by The Company will relieve The Company of all further liability in connection with its warranty. In no event will
The Company's warranty obligation exceed The Company's charge for the machine. The following are not covered by The
Company's warranty:
a.
Lighting of gas pilots or burners.
b.
Cleaning of gas lines.
c.
Replacement of fuses or resetting of overload breakers.
d.
Adjustment of thermostats.
e.
Adjustment of clutches.
f.
Opening or closing of utility supply valves or switching of electrical supply current.
g.
Cleaning of valves, strainers, screens, nozzles, or spray pipes.
h.
Performance of regular maintenance and cleaning as outlined in operator’s guide.
i.
Damages resulting from water conditions, accidents, alterations, improper use, abuse,
tampering, improper installation, or failure to follow maintenance and operation procedures.
j.
Wear on Pulper cutter blocks, pulse vanes, and auger brush.
Examples of the defects not covered by warranty include, but are not limited to:
(1) Damage to the exterior or interior finish
as a result of the above, (2) Use with utility service other than that designated on the rating plate, (3) Improper connection to
utility service, (4) Inadequate or excessive water pressure, (5) Corrosion from chemicals dispensed in excess of recommended
concentrations, (6) Failure of electrical components due to connection of chemical dispensing equipment installed by others, (7)
Leaks or damage resulting from such leaks caused by the installer, including those at machine table connections or by connection
of chemical dispensing equipment installed by others, (8) Failure to comply with local building codes,
(9) Damage caused by labor dispute.
Warranty of Parts:
The Company warrants all new machine parts produced or authorized by The Company to be free from
defects in material and workmanship for a period of 90 days from date of invoice. If any defect in material and workmanship is
found to exist within the warranty period The Company will replace the defective part without charge.
DISCLAIMER OF WARRANTIES AND LIMITATIONS OF LIABILITY. THE COMPANY'S WARRANTY
IS ONLY TO THE EXTENT REFLECTED ABOVE. THE COMPANY MAKES NO OTHER WARRANTIES,
EXPRESS OR IMPLIED, INCLUDING, BUT NOT LIMITED, TO ANY WARRANTY OF MERCHANTABILITY,
OR FITNESS OF PURPOSE. MOYER DIEBEL SHALL NOT BE LIABLE FOR INCIDENTAL OR CONSE-
QUENTIAL DAMAGES. THE REMEDIES SET OUT ABOVE ARE THE EXCLUSIVE REMEDIES FOR ANY
DEFECTS FOUND TO EXIST IN THE COMPANY'S DISHWASHING MACHINES AND THE COMPANY'S
PARTS, AND ALL OTHER REMEDIES ARE EXCLUDED, INCLUDING ANY LIABILITY FOR INCIDENTALS
OR CONSEQUENTIAL DAMAGES.
Moyer Diebel does not authorize any other person, including persons who deal in Moyer Diebel dishwashing machines to change this warranty
or create any other obligation in connection with Moyer Diebel Dishwashing Machines.
Summary of Contents for 601HRG
Page 43: ...35 Digital Temperature Display Board...
Page 44: ...36 Blank Page This Page Intentionally Left Blank...
Page 46: ...38 Wash Pump Motor Assembly 1 11 12 2 3 4 5 7 8 9 10 6 13 14 15...
Page 51: ...43 43 Blank Page This Page Intentionally Left Blank...
Page 54: ...46 Fill Solenoid Valve 1 2 3 4 9 5 6 7 8...
Page 56: ...48 Final Rinse Piping 1 2 2 10 7 2 1 1 1 1 1 8 9 4 6 5...
Page 62: ...54 Booster Heater 3 8 2 2 1 4 5 7 6 9 10 12 11 14 13 11 16 15...
Page 68: ...60 Power Input Block 1 2 3 4 5 6 7 8...
Page 70: ...62 Timer Control Board Assembly Rear View Front View 1 10 2 4 4 5 6 2 4 7 8 9 11 12 13 3...
Page 74: ...66 Control Panel 10 11 12 13 14 3 2 1 4 5 6 7 9 8 8 9...
Page 76: ...68 Panels 7 8 10 1 2 3 4 5 6 9...
Page 78: ...70 Door Assembly 1 10 4 5 6 6 7 7 9 9 8 10 2 3 3 5...
Page 80: ...72 Dish Racks Line Strainer PRV 1 2 3 4...
Page 82: ...74 74 Electrical Schematic SINGLE PHASE THREE PHASE 6 AMP FUSE...
Page 84: ...76 Blank Page This Page Intentionally Left Blank...