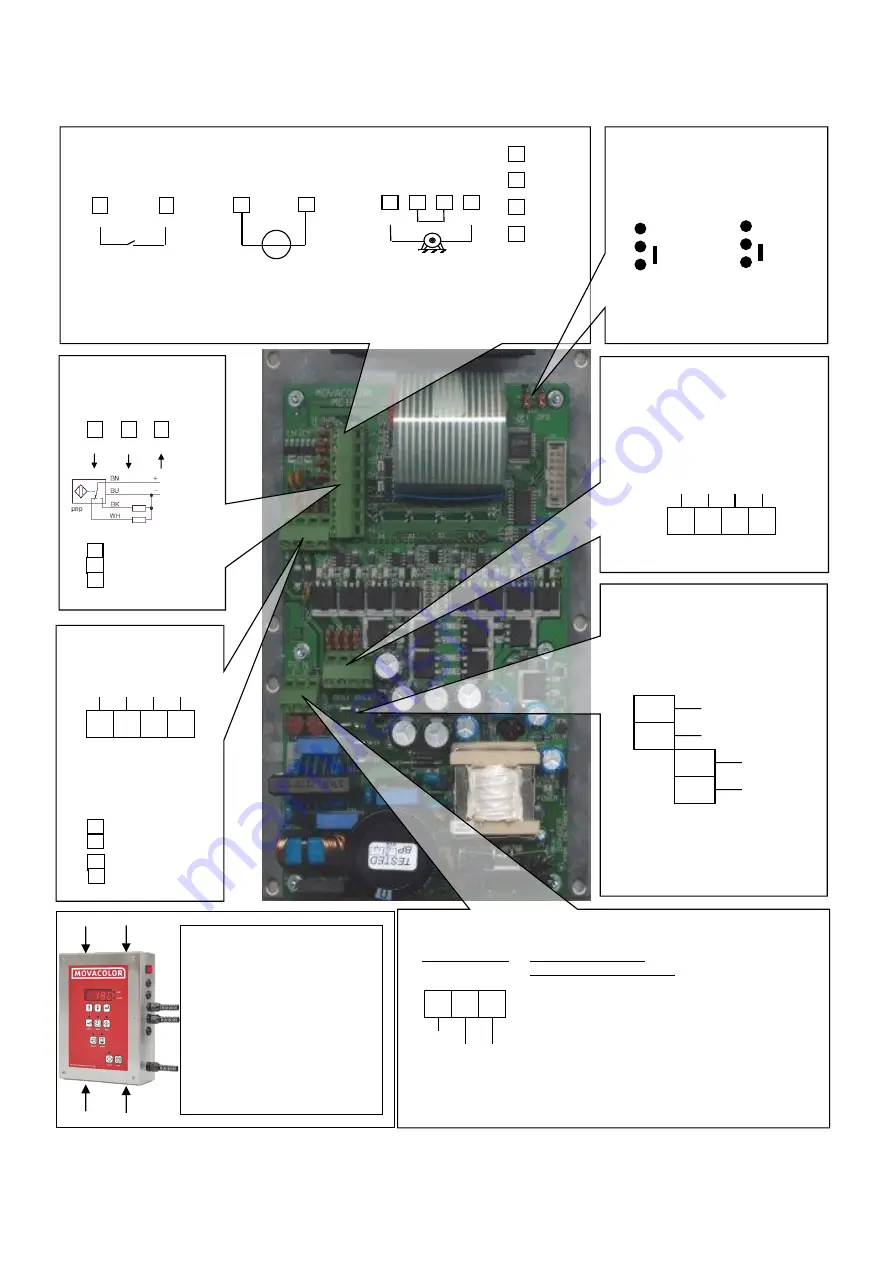
21
MC18-Micro manual
APPENDIX B: MC18-Micro Wiring Diagram
Motor
B
ro
w
n
(
1
)
7
6
5
4
Coil 1
Coil 2
Y
e
llo
w
(
2
)
Gr
e
e
n
(
3
)
W
h
it
e
(
4
)
To open the control cabinet
use the 4 bolds on the top and
bottom side, not the 6 bolds at
the front side.
WARNING
Do not make any changes to
the main board/components
ore warranty will lapse.
Black (N)
Blue (N)
X5
Brown (L)
X4
Black (L)
X2
X3
Internal wires
main power switch
Outputs
[ 24 VDC]
A
lar
m
(-
)
18
19
20
21
Output
1
A
lar
m
(+)
V
a
lv
e
(
-)
V
a
lv
e
(
+)
Output
2
Input (start) signal
Potential free contact
Potential contact
[Min 18VDC to Max.24VDC]
-
+
10
8
9
+
10
IN
-
+
17
8
9
10
8
= Yellow
9
= Brown
10
= White
17
= Green
Tacho
[Min 0VDC to Max. 30VDC]
Sensor input
(24VDC) INP2
11
13
+24VDC
Gnd
12
Inp.2
Capacity
sensor
11
= Blue
12
13
= Brown
= White
18
19
20
= White
= Brown
= White
= Brown
21
Jumper settings
JP1 Motor alarm on/off
JP2 Motor type selection LT, HT
Power Supply
USA,Canada,Mexico,
Mid America,Japan,Taiwan
1 = Black
2 = White
3 = Green
Western Europe
3
2
B
ro
w
n
1
PE
L
N
B
lue
Gr
e
e
n
/Y
e
llo
w
JP1
OFF
Alarm OFF
ON
Alarm ON
OFF
JP2
Motor 4,5A
ON
Motor 2 A