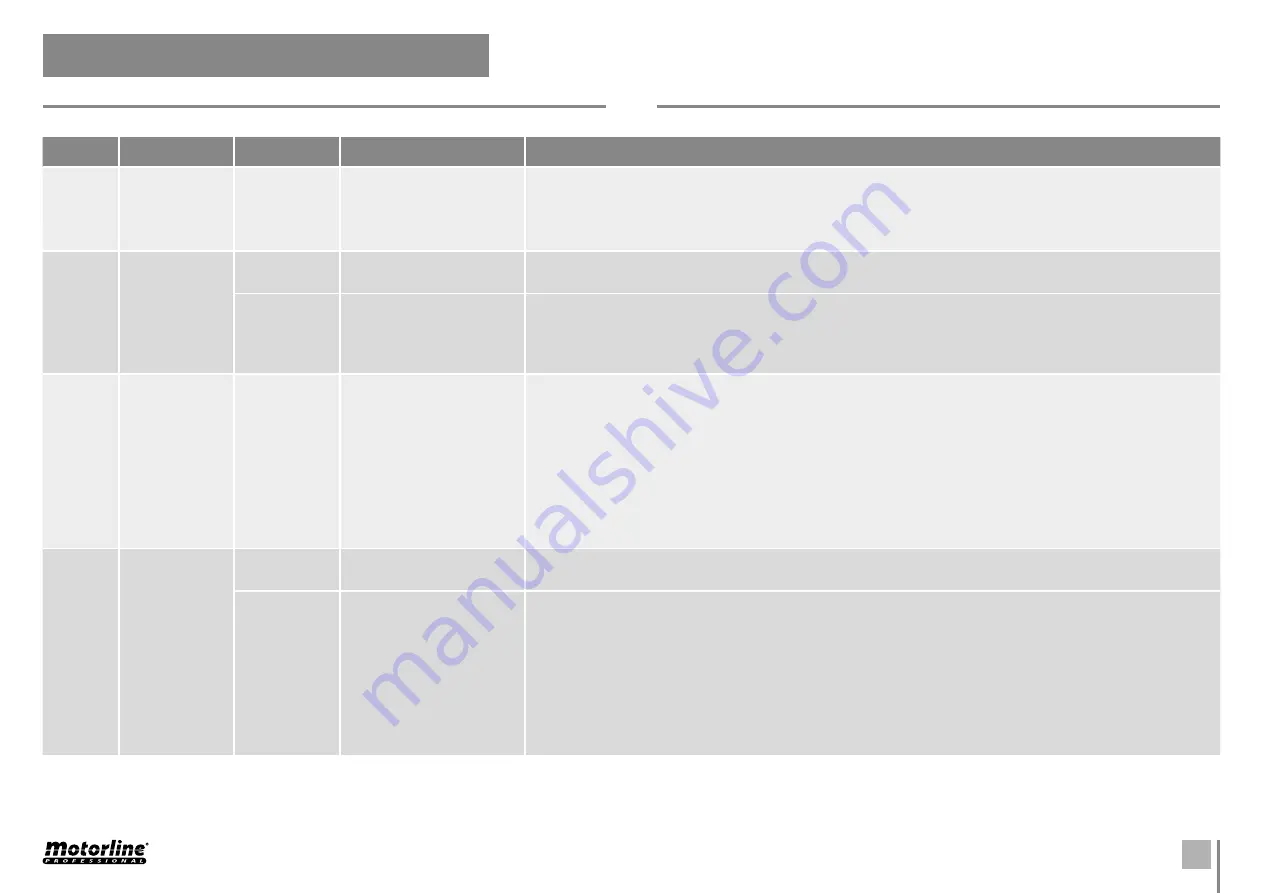
12A
12
EN
Anomaly
Procedure
Behavior
Procedure II
Discovering the origin of the problem
• Motor
doesn't
work at all.
• Make sure you
have power in the
automation control
board and if it is
working properly.
• Still not working.
• Consult a qualified MOTORLINE
technician.
• Motor
doesn’t
move
but makes
noise.
• Unlock motor and
move gate by hand
to
check for
mechanical
problems on the
gate.
• Is the gate
closed?
• Consult an experienced
gate expert.
1 • Check all motion axis and associated motion systems related with gate and operators (pins, hinges, etc.) to find out what is the problem.
• Gate moves
easily?
• Consult a qualified
MOTORLINE technician.
• Motor
opens
but doesn’t
close.
• Unlock motor and
move gate by hand
to
closed position.
Lock motor(s) again
and turn off power
supply for 5
seconds.
Reconnect it and
send
order to open gate
using transmitter.
• Gate opened but
didn’t close again.
1 • Check if there is any
obstacle in front of the
photocells;
2 • Check if any of the control
devices (key selector, push
button, video intercom, etc.)
of the gate are jammed and
sending permanent signal to
control unit;
3 • Consult a qualified
MOTORLINE technician.
• Motor
doesn’t
make
complete
route.
• Unlock motor and
move gate by hand
to
check for
mechanical
problems on the
gate.
• Encountered
problems?
• Consult an experienced
gate expert.
1 • Check all motion axis and associated motion systems related with gate and operators (pins, hinges, etc.) to find out what is the problem.
• Gate moves
easily?
• Consult a qualified
MOTORLINE technician.
1 • Open control box and check
if it has 230V/110V/24V power
supply;
2 • Check input fuses;
3 • Disconnect motors from
control board and test them by
connecting directly to power
supply in order to find out if they
have problems (see page 8B/9).
4 • If the motors work, the
problem is on the control board.
Pull it out and send it to our
MOTORLINE technical services for
diagnosis;
5 • If the motors doesn’t work,
remove them from installation
site and send to our MOTORLINE
technical services for diagnosis.
1 • Check capacitors, testing
operator with new capacitors;
2 • If capacitors are not the
problem, disconnect motors
from control board and test them
by connecting directly to power
supply in order to find out if they
have problems (see page 8B/9).
3 • If the motors work, the
problem is from control board.
Pull it out and send it to our
MOTORLINE technical services for
diagnosis;
4 • If the motors doesn’t work,
remove them from installation
site and send to our MOTORLINE
technical services for diagnosis.
1 • Check capacitors, testing with
new capacitors;
2 • If capacitors are not the
problem, disconnect motors from
control board and test them by
connecting directly to power
supply in order to find out if they
are faulty;
3 • If the motors doesn’t work,
remove them from installation
site and send to our MOTORLINE
technical services for diagnosis.
4 • If motors work well and move
gate at full force during the
entire course, the problem is
from controller. Set force using
trimmer on the board. Make a
new working time programming ,
giving suffient time for opening
and closing with appropriate
force (see manual of the
controller in question).
5 • If this doesn’t work, remove
control unit and send it to
MOTORLINE technical services
services.
NOTE:
Setting force of the
controller should be sufficient
to make the gate open and close
without stopping, but should stop
with a little effort from a person.
In case of safety systems failure,
the gate shall never cause
physical damaged to obstacles
(vehicles, people, etc.).
All MOTORLINE control boards have LEDs that
easily allow to conclude which devices are
with anomalies.
All safety devices LEDs (DS) in normal
situations remain On.
All "START" circuits LEDs in normal situations
remain Off.
If LEDs devices are not all On, there is some
security systems malfunction (photocells,
safety edges), etc.
If "START" circuits LEDs are turn On, there is a
control device sending permanent signal.
A) SECURITY SYSTEMS:
1 • Close with a shunt all safety systems
on the control board (check manual of the
control board in question).
If the automated system starts working
normally check for the problematic device.
2 • Remove one shunt at a time until you find
the malfunction device .
3 • Replace it for a functional device and
check if the operator works correctly with
all the other devices. If you find another one
defective, follow the same steps until you find
all the problems.
B) START SYSTEMS:
1 • Disconnect all wires from START terminal
input.
2 • If the LED turned Off, try reconnecting one
device at a time until you find the defective
device.
NOTE:
In case procedures described in sections A)
and B) don’t result, remove control board and
send to our technical services for diagnosis.
08. TROUBLESHOOTING
FINAL CONSUMERS INSTRUCTIONS
INSTRUCTIONS FOR SPECIALIZED INSTALLERS