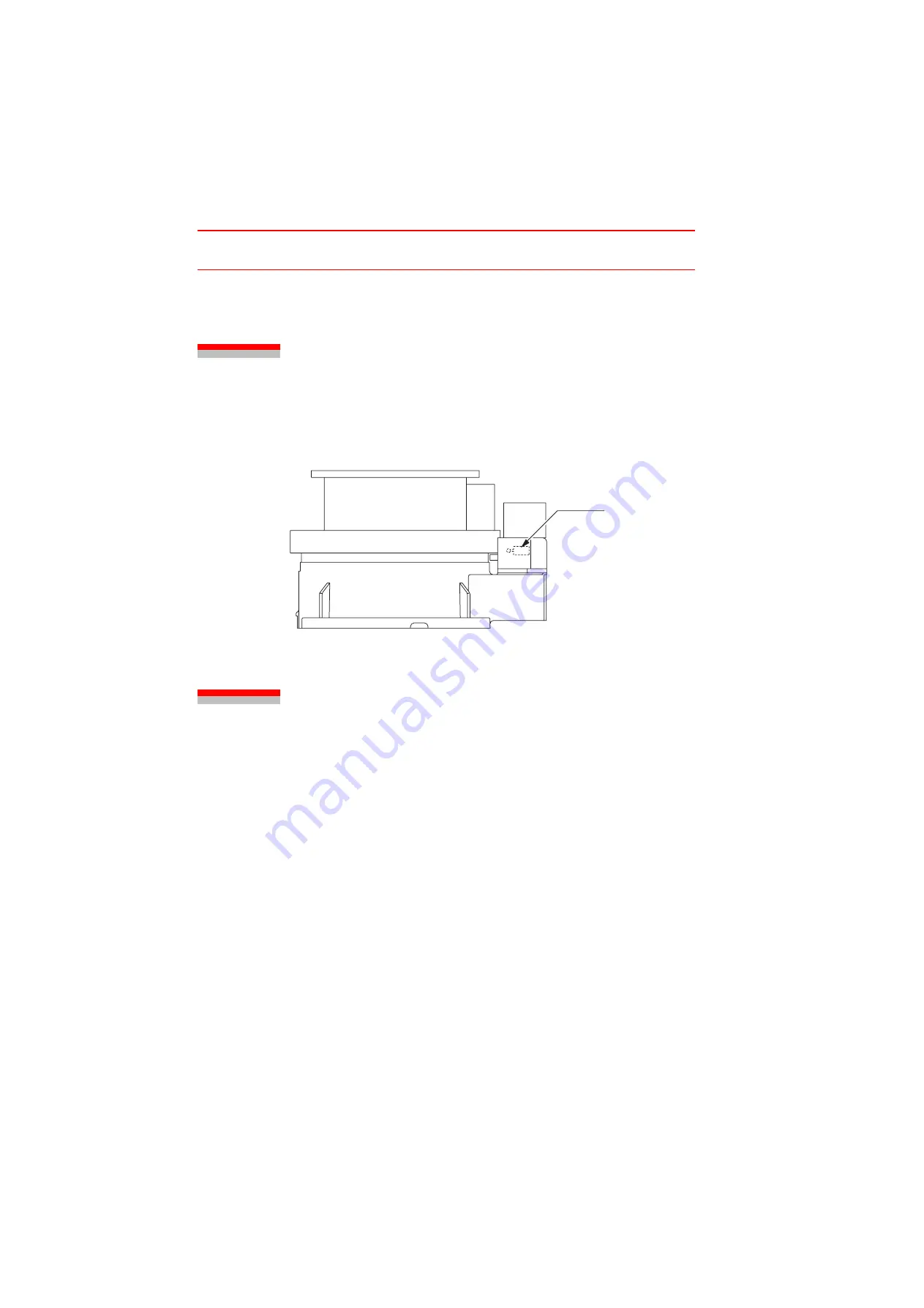
8.1 Position of Limit Switch
8-1
HS0481357
HS0481357
8
Electrical Equipment Specification
8.1
Position of Limit Switch
One limit switch is provided inside the MOTOPOS. For the location, refer to " Fig. 15
Location of Limit Switch ".
Fig. 15 Location of Limit Switch
8.2
Internal Connections
High reliability connectors which can be easily put on and removed are used in each
connector part.
Limit switch