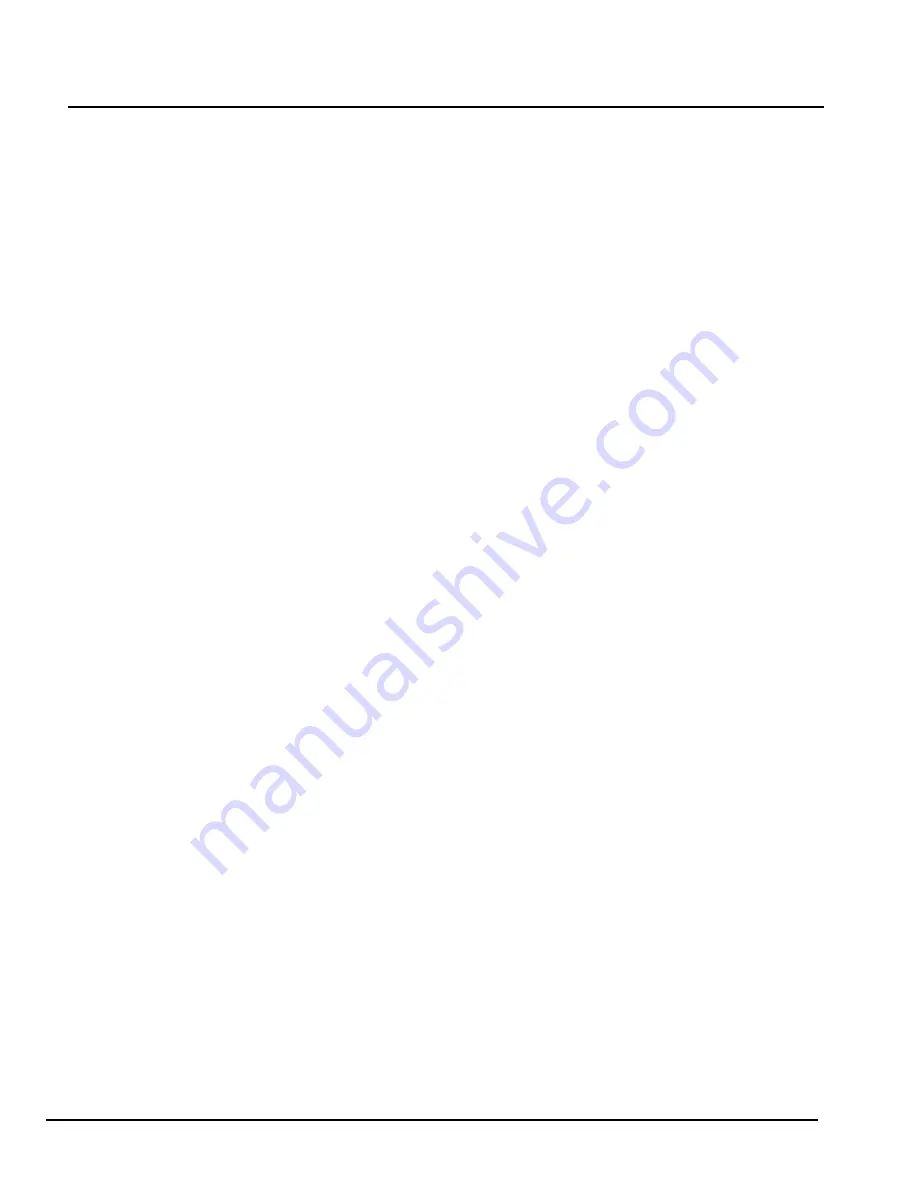
Table of Contents
Bin Level Adjustment ...................................................................................................5-16
Filling Tank ...................................................................................................................5-16
Unloading Tanks ..........................................................................................................5-18
Rate Charts .................................................................................................................5-19
Spacing Sprocket .....................................................................................................5-19
Rate Chart Use ........................................................................................................5-20
Extra Low Rates .......................................................................................................5-21
Extra High Rates ......................................................................................................5-21
Fertilizer Rate Chart .................................................................................................5-22
Seed Rate Chart ......................................................................................................5-23
Slow Speed Seed Rate Chart ..................................................................................5-24
Rate Calibration ...........................................................................................................5-25
Seeding Fine Seeds (Canola, Mustard, etc.) ...............................................................5-27
Applying Inoculant .......................................................................................................5-27
Hydraulic Fan Drive .....................................................................................................5-28
Fan Speed Recommendations ....................................................................................5-29
Double Shoot Settings .................................................................................................5-30
Plenum Damper Settings .........................................................................................5-30
Collector Valve Settings ............................................................................................5-31
Flapper Valve Run Test .............................................................................................5-31
Accumulator System Operation and Pre-Charge Information ...................................5-32
Setting Maximum System Pressure (Trip Out Force) ................................................5-33
Relieve System Pressure .........................................................................................5-34
Normal Operation .....................................................................................................5-34
Pressure Adjustment (On the go) .............................................................................5-35
Depth Adjustment ........................................................................................................5-36
Work Switch .................................................................................................................5-38
Quick Tips ....................................................................................................................5-39
Shank Trip Force .......................................................................................................5-39
Packing Force ...........................................................................................................5-39
Hydraulic System .....................................................................................................5-39
Lifting and Lowering the Openers ............................................................................5-39
Setting the Seed Depth ............................................................................................5-40
Seeding Conditions ..................................................................................................5-40
Straw Management ..................................................................................................5-40
Air Drill Frame ..........................................................................................................5-41
Trouble Shooting Guide ............................................................................................5-41
Wing Lift Hydraulics .....................................................................................................5-42
Opener Hydraulics ......................................................................................................5-43
General Guidelines ......................................................................................................5-48
Turning ......................................................................................................................5-49
Seed Rate Settings ..................................................................................................5-49
Fertilizer Application .................................................................................................5-49
Fan Setting ...............................................................................................................5-49
Product Application...................................................................................................5-49
Adjustments and Operational Checks ......................................................................5-50
Checking Seed Flow ................................................................................................5-50
Moisture Alert ...........................................................................................................5-50
Air Leaks ..................................................................................................................5-50
Tank Low in Product .................................................................................................5-50
Monitor .....................................................................................................................5-51
ii
December 2016
CX 8105 - Ground Drive
Summary of Contents for CX 8105
Page 1: ...OPERATOR S MANUAL N62398 00 CX 8105 Air Drill Ground Drive...
Page 2: ......
Page 8: ...Table of Contents vi December 2016 CX 8105 Ground Drive Notes...
Page 18: ...Safety 1 10 December 2016 CX 8105 Ground Drive Safety Signs Continued Front Side Rear Side...
Page 19: ...Safety CX 8105 Ground Drive December 2016 1 11 Safety Signs Continued Left Side Right Side...
Page 26: ...Specifications 2 4 December 2016 CX 8105 Ground Drive Notes...
Page 30: ...Checklist 3 4 December 2016 CX 8105 Ground Drive Notes...
Page 34: ...Introduction 4 4 December 2016 CX 8105 Ground Drive Notes...
Page 86: ...Operation 5 52 December 2016 CX 8105 Ground Drive Notes...
Page 116: ...Monitor 6 30 December 2016 CX 8105 Ground Drive Notes...
Page 162: ...Maintenance 7 46 December 2016 CX 8105 Ground Drive Notes...
Page 168: ...Storage 8 6 December 2016 CX 8105 Ground Drive Notes...
Page 180: ...T roubleshooting Problem Correction Cause 9 12 December 2016 CX 8105 Ground Drive...
Page 181: ......