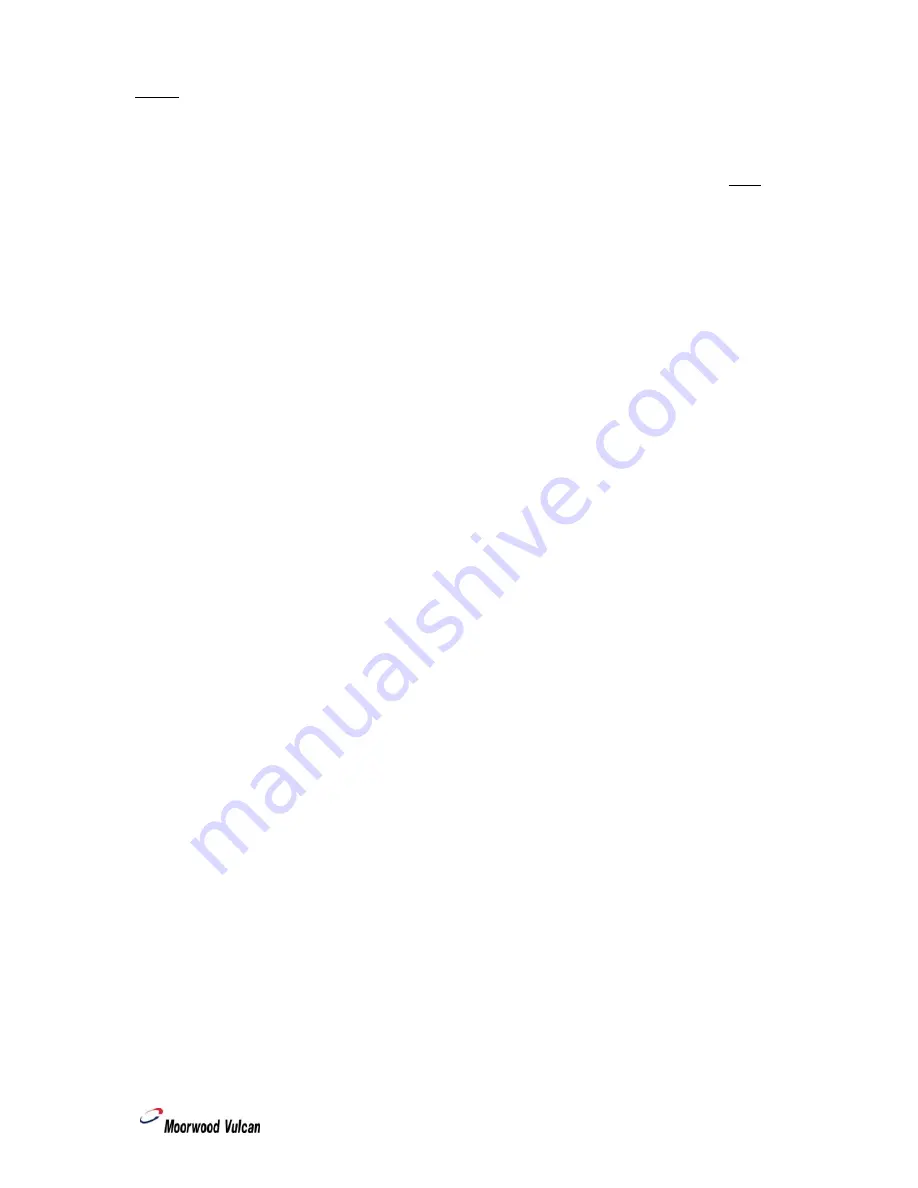
Manual Part No: 932971-01 MD Gas Convection Oven
Page 3 of 32
Manual Rev No: 1
INDEX
Page
Cover Sheet:
1
Revision Sheet:
2
Index:
3
Warning Sheet :
4
Introduction:
5 & 6
General Introduction
5
Important Note
6
Specification:
7 - 12
Gas Pressure/Connection
7 & 8
Overall Dimensions
9 & 10
Wiring Diagrams
11 & 12
Installation:
13 - 16
Important Note
13
Positioning
14 & 15
Checking & Commissioning
15 & 16
User Instructions:
17 - 21
Important Note
17
Operation
18 & 19
Cleaning
20 & 21
Service & Maintenance:
22 - 29
Routine Maintenance
22
Fault Finding
23 - 25
Instructions
26 - 29
Spare Parts:
30 & 31
Warranty Cover Sheet:
32