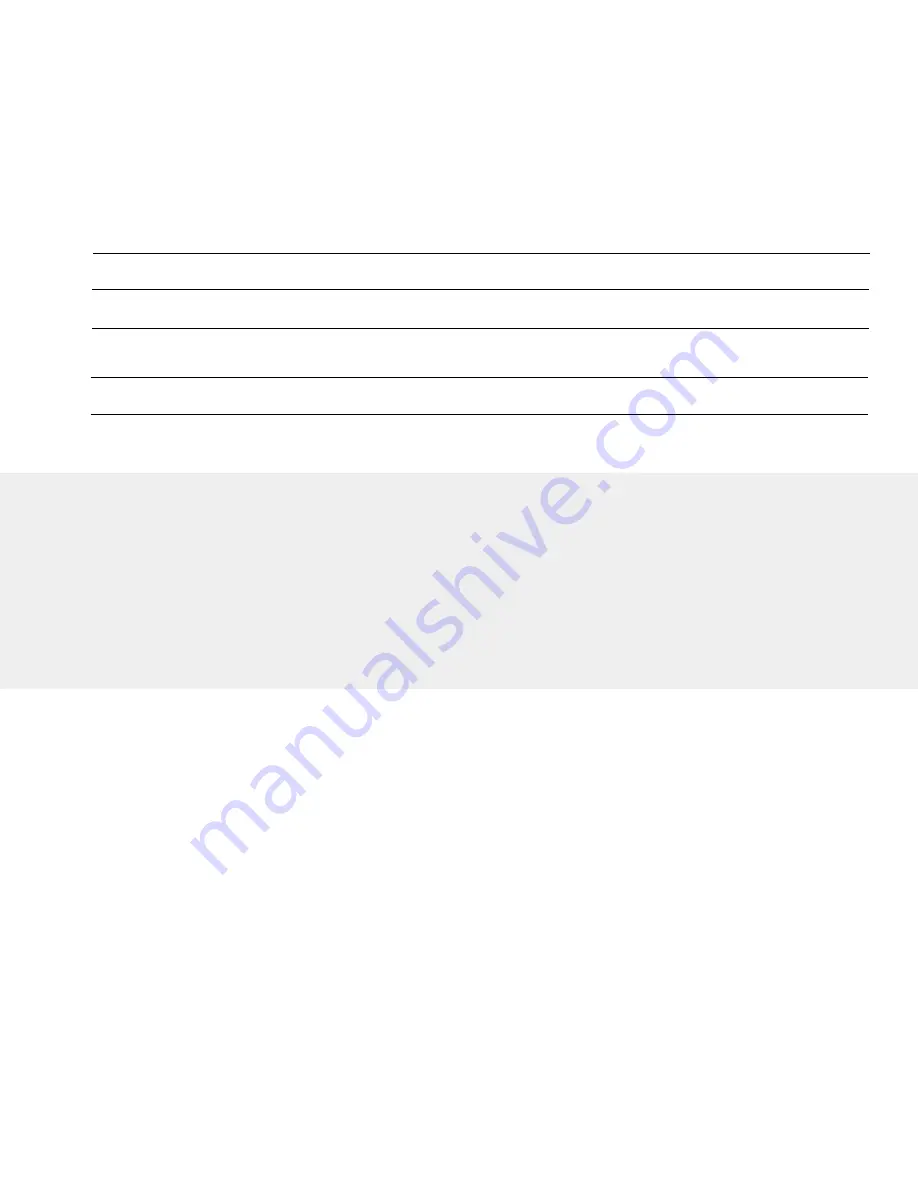
Probable Cause
1. Seals damaged or missing.
2. Required torque is incorrect.
1. Loss of hydraulic pressure.
2. Loss of supply voltage.
1. Unstable external loop.
2. Valve electronics defective.
1. Power supply problem.
2. Incorrect null adjust.
1. Orifice contaminated.
9. TROUBLESHOOTING CHART
The following troubleshooting chart lists potential troubles encountered, probable causes and remedies.
Potential Trouble
Leakage at the mounting surface
of the valve.
No hydraulic response of the
valve.
Instability of the system, plant
oscillates.
With zero command signal, the
load drifts slowly off position
(open loop).
With hydraulics on, valve goes
hardover.
Remedy
1. Make sure all seals are installed at ports A, B, P, T, X and Y are ok.
2. Tighten mounting bolts.
1. Check all signals from Pin A to Pin F.
2. Check the mating connector for corrosion.
1. Check whether output signal at Pin F (6) is following exactly the command signal at Pin D.
2. Send to Moog factory for repair.
1. With
±
15 VDC supply, check for supply voltage at pins A and B being stable within
±
3% of 15V
2. With both
±
15 VDC and 24 VDC supply, at zero command and normal operation temperature,
stop load motion by adjusting nulladjust potentiometer (behind screw plug).
1. Send to Moog factory for repair.
13
10.
AUTHORIZED REPAIR FACILITIES
If servovalve continues to malfunction after all recommended
corrective action procedures are performed, defective valve should be
returned to Moog for repair. Moog does not authorize any facilities other
than Moog or Moog subsidiaries to repair its servovalves. It is
recommended you contact Moog at (716)655-3000 to locate your closest
Moog repair facility. Repair by an independent (unauthorized) repair
house will result in voiding the Moog warranty and could lead to
performance degradation or safety problems.
11. DECLARATION OF MANUFACTURER
A Declaration of Manufacturer according to EC machine directive 89/
392/EWG, Annex II B, is available for servo and proportional valves D661
Series and will be supplied upon request.