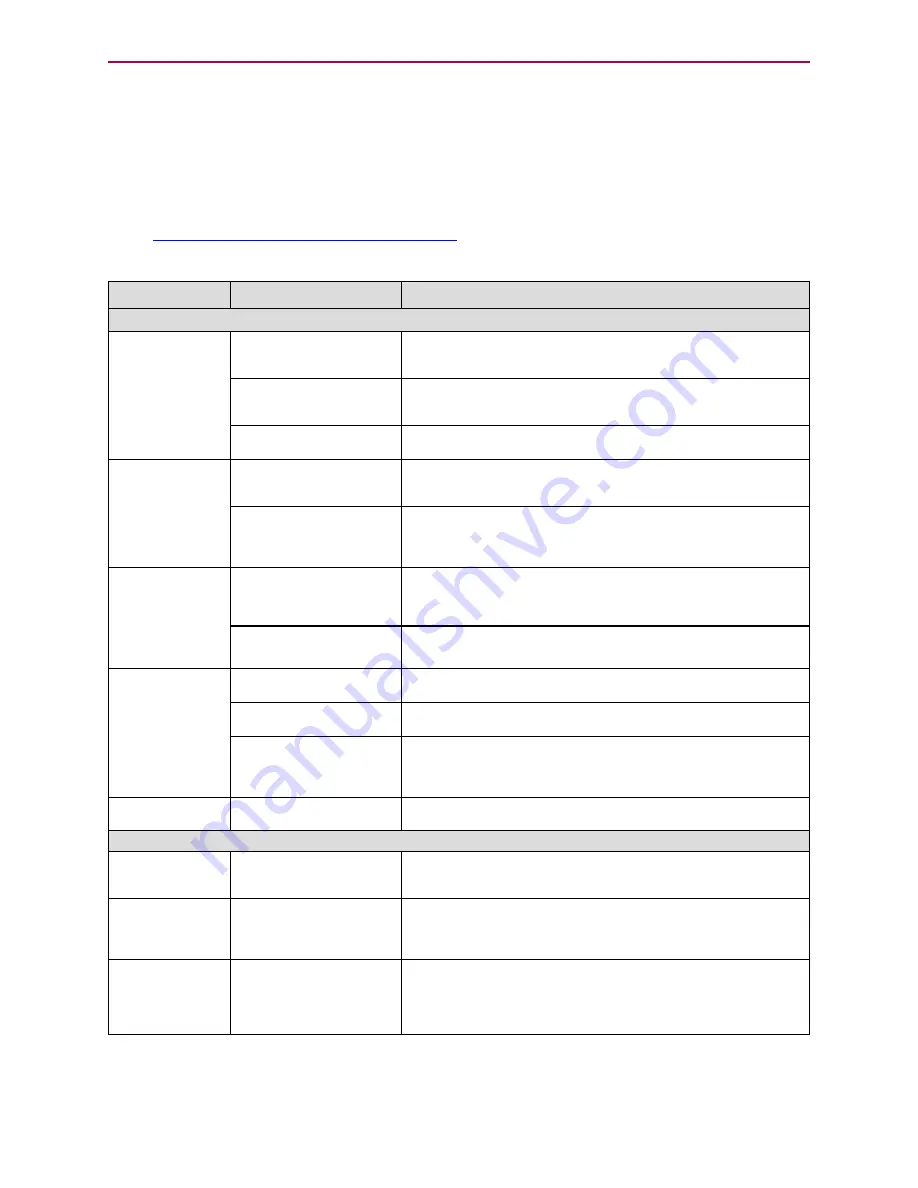
Troubleshooting
Troubleshooting
The following table provides troubleshooting information for solving common problems. For
additional support resources, see the Moog Animatics Support page at:
http://www.animatics.com/support.html
Issue
Cause
Solution
Communication and Control Issues
Motor control
power light does
not illuminate.
Control power is off,
disconnected or
incorrectly wired.
Check that control power is connected to the proper pins and
turned on. For connection details, see Connecting the System on
page 12.
Motor has routed drive
power through drive-
enable pins.
Ensure cabling is correct and drive power is not being delivered
through the 15-pin connector.
Motor is equipped with
the DE option.
To energize control power, apply 24-48 VDC to pin 15 and ground
to pin 14.
Motor does not
communicate
with SMI.
Transmit, receive or
ground pins are not
connected correctly.
Ensure that transmit, receive and ground are all connected
properly to the host PC.
Motor program is stuck in
a continuous loop or is
disabling
communications.
To prevent the program from running on power up, use the
Communications Lockup Wizard located on the SMI software
Communications menu.
Motor not detec-
ted or not com-
municating
through TCP (Eth-
ernet port in
SMI).
IP address and/or net-
mask not set.
See IPCTL command, or check DHCP server.
Feature disabled
See ETHCTL(100,<value>) command.
Motor
disconnects from
SMI sporadically.
COM port buffer settings
are too high.
Adjust the COM port buffer settings to their lowest values.
Poor connection on serial
cable.
Check the serial cable connections and/or replace it.
Power supply unit (PSU)
brownout.
PSU may be too high-precision and/or undersized for the
application, which causes it to brown-out during motion. Make
moves less aggressive, increase PSU size or change to a linear
unregulated power supply.
Red PWR SERVO
light illuminated.
Critical fault.
To discover the source of the fault, use the Motor View tool located
on the SMI software Tools menu.
Common Faults
Bus voltage fault.
Bus voltage is either too
high or too low for
operation.
Check servo bus voltage. If motor uses the DE power option,
ensure that both drive and control power are connected.
Overcurrent
occurred.
Motor intermittently drew
more than its rated level
of current. Does not cease
motion.
Consider making motion less abrupt with softer tuning
parameters or acceleration profiles.
Excessive
temperature
fault.
Motor has exceeded
temperature limit of 85°C.
Motor will remain
unresponsive until it cools
down below 80°C.
Motor may be undersized or ambient temperature is too high.
Consider adding heat sinks or forced air cooling to the system.
Moog Animatics Class 6 SmartMotor™ Ethernet Serial Encapsulation Guide, Rev. B
Page 29 of 32
Summary of Contents for Smart Motor SM23166MT
Page 31: ......
Page 32: ...PN SC80100017 001 Rev B Ethernet Serial Encapsulation ...