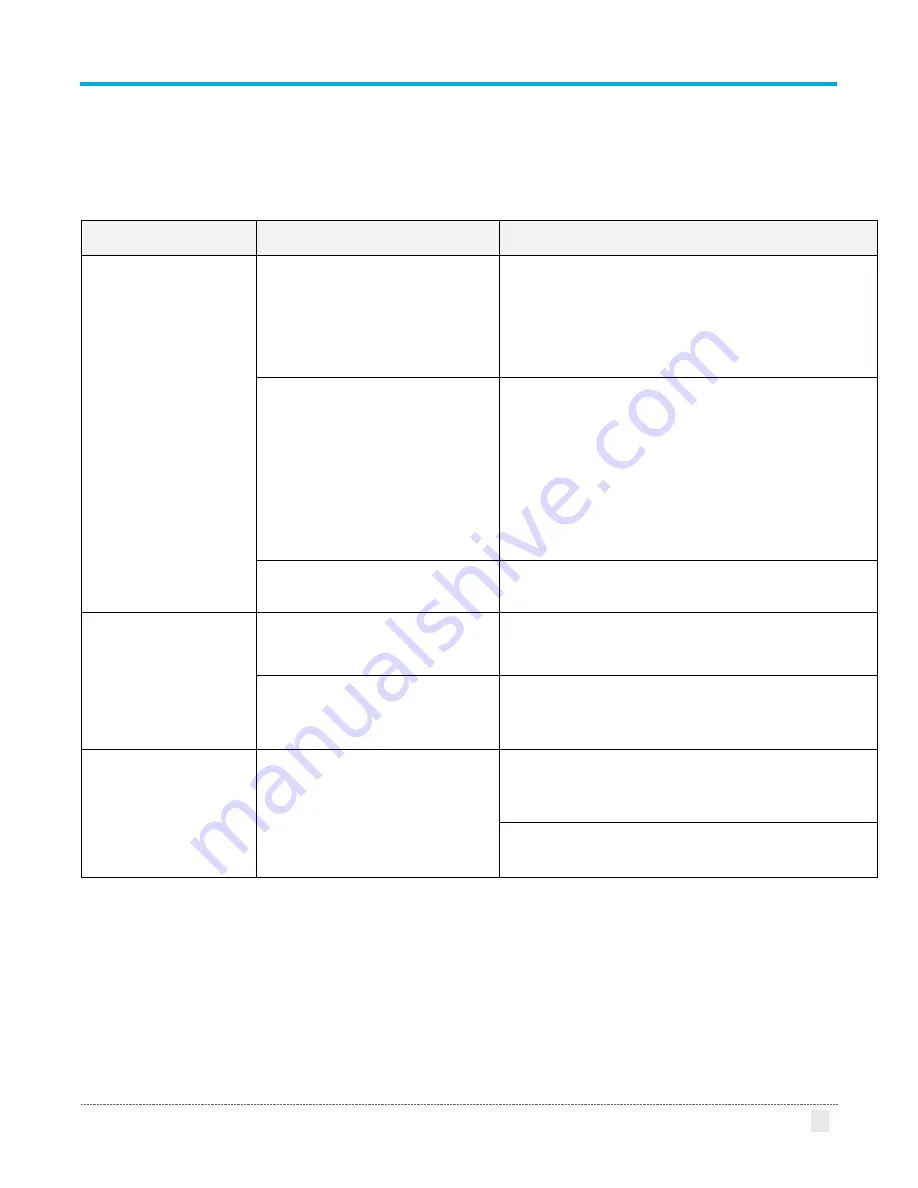
49
7.1
Troubleshooting Guide
If a degradation in performance or other failures are experienced, check for these common issues:
Problem/Symptom
Possible Cause
Solution/Suggestion
Axis not moving
Physical impediment.
•
Check physical state of positioner stack for:
o
Grease on the axis that isn’t moving.
o
Any other contamination on the axis.
o
Wire routing impediments.
o
Potential collisions preventing
movement.
Control cabling issue.
Ensure all cables and wiring are connected/plugged in
and do not have any shorts or breaks.
•
Check thermal clamp where In-Vacuum control
cable is clamped and make sure it isn’t clamped
too tight:
o
Remove clamp and check to see if axis
becomes operational.
o
Re-install clamp and do not torque
screws to more than 0.5 in-lbs.
Incorrect settings (open loop
only).
Confirm that settings are correct.
No encoder feedback
(incorrect feedback)
Cables are not properly
connected.
Check cables and plugs to ensure everything is
connected properly and do not have any shorts or
breaks.
Nanopositioner is not paired with
the correct controller (multi-stack
configuration).
If in a multi-stack configuration confirm that the
correct controller is being paired with the
nanopositioner.
Z-axis not moving up
Mass on top of positioner is too
heavy (100g-250g)
Mass (>100g) on top of the positioner, you may have
overloaded the z-axis. Reduce the mass on top of the
positioner.
Install the Low Force Spring Plunger and see if the
positioner can lift the mass.