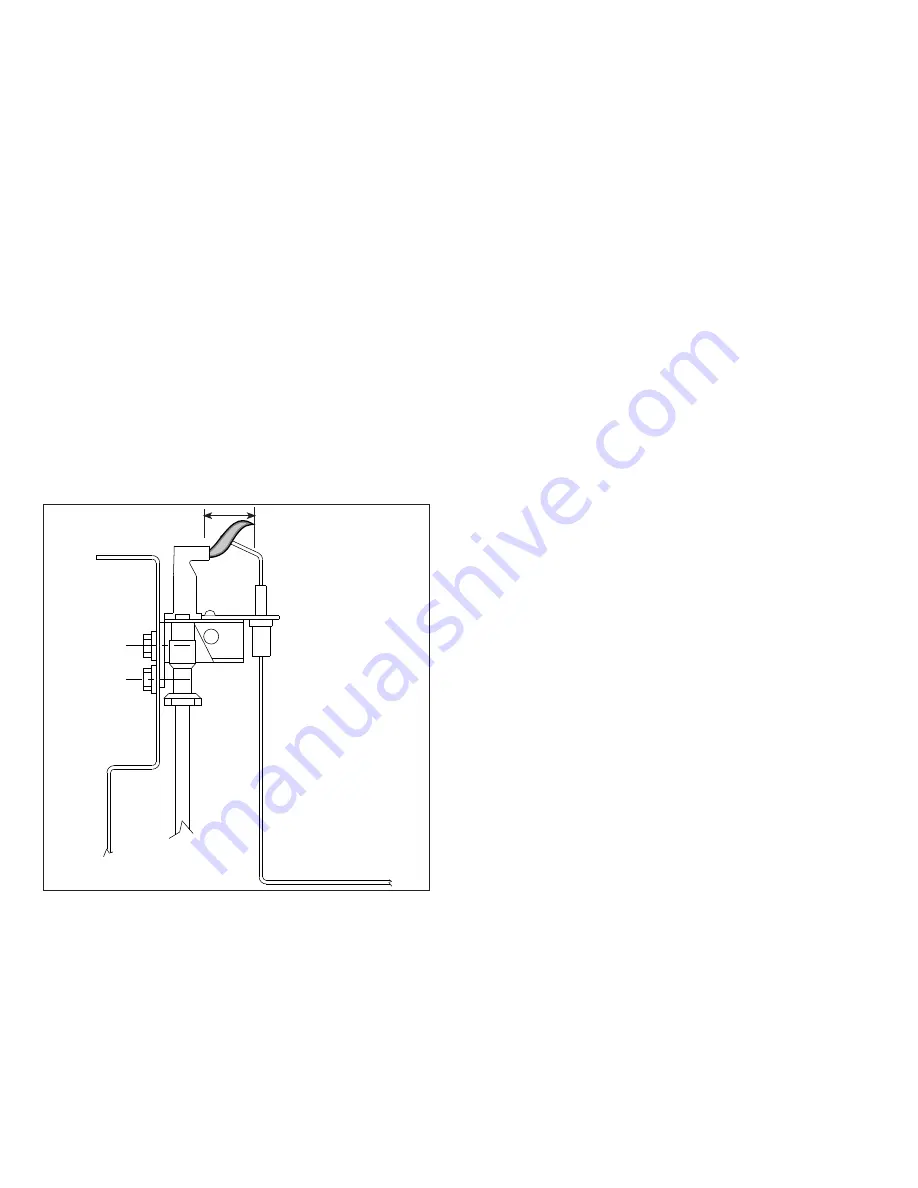
5-571.4
88
start-uP ProceDure
Pilot burner adjustment
The pilot burner is orificed to burn properly with an inlet
pressure of 6-7" W.C. on natural gas and 11-14" W.C. on
propane gas, but final adjustment must be made after
installation. If the pilot flame is too long or large, it is possible
that it may cause soot and/or impinge on the heat exchanger
causing failure. If the pilot flame is shorter than shown, it may
cause poor ignition and result in the controls not opening the
combination gas control. A short flame can be caused by a
dirty pilot orifice. Pilot flame condition should be observed
periodically to assure trouble-free operation.
to adjust the Pilot flame
1. Create a call for heat from the thermostat.
2. Remove the cap from the pilot adjustment screw. For
location, see the combination gas control literature supplied
with unit.
3. Adjust the pilot length by turning the screw in or out
to achieve a soft steady flame 3/4" to 1" long and
encompassing 3/8"-1/2" of the tip of the thermocouple or
flame sensing rod (See Figure 8.1).
4. Replace the cap from the pilot adjustment screw.
figure 8.1 - correct Pilot flame
main burner adjustment
The gas pressure regulator (integral to the combination gas
control) is adjusted at the factory for average gas conditions.
It is important that gas be supplied to the duct furnace in
accordance with the input rating on the serial plate. Actual
input should be checked and necessary adjustments made
after the duct furnace is installed. Over-firing, a result of too
high an input, reduces the life of the appliance and increases
maintenance. Under no circumstances should the input exceed
that shown on the serial plate.
Measuring the manifold pressure is done at the tee in the
manifold (See Figure 9.1).
to adjust the manifold Pressure
1. Move the field installed manual shut-off valve to the “OFF”
position.
2. Remove the 1/8" pipe plug in the pipe tee and attach a
water manometer of “U” tube type which is at least 12" high.
3. Move the field installed manual gas shut-off valve to the
“ON” position.
4. Create a high fire call for heat from the thermostat.
5. Determine the correct high fire manifold pressure. For
natural gas 3.5” W.C., for propane gas 10” W.C. Adjust the
main gas pressure regulator spring to achieve the proper
manifold pressure (for location, see the combination gas
control literature supplied with unit).
6. If the unit has Electronic Modulation gas controls
(determine from the Model Identification Digit 12), the low
fire gas pressure needs to be adjusted. Using Figure 9.2 for
item number locations, this is accomplished as follows:
a. Disconnect power.
b. Remove all wires from duct furnace terminal “43” and
remove cover plate (2).
c. Turn on power at the disconnect switch.
d. Remove the maximum adjustment screw (4), spring
(5), and plunger (8). A small magnet is useful for this
purpose. CAUTION - The plunger is a precision part.
Handle carefully to avoid marring or picking up grease
and dirt. Do not lubricate.
e. Using minimum adjusting screw (9), adjust low fire
manifold pressure to 0.56" W.C. for natural gas and
1.6" W.C. for propane gas.
f. Replace plunger and spring retainer, spring, and
maximum adjusting screw in proper order.
g. Using maximum adjustment screw (4), adjust high fire
manifold pressure to 3.5" W.C. for natural gas and 10"
W.C. for propane gas.
h. Disconnect power.
i. Replace cover plate (2) and re-install all wires from
duct furnace terminal “43”.
7. After adjustment, move the field installed manual shut-off
valve to the “OFF” position and replace the 1/8" pipe plug.
8. After the plug is in place, move the field installed manual
shut-off valve to the “ON” position and recheck pipe plugs
for gas leaks with soap solution.
3/4" to 1"