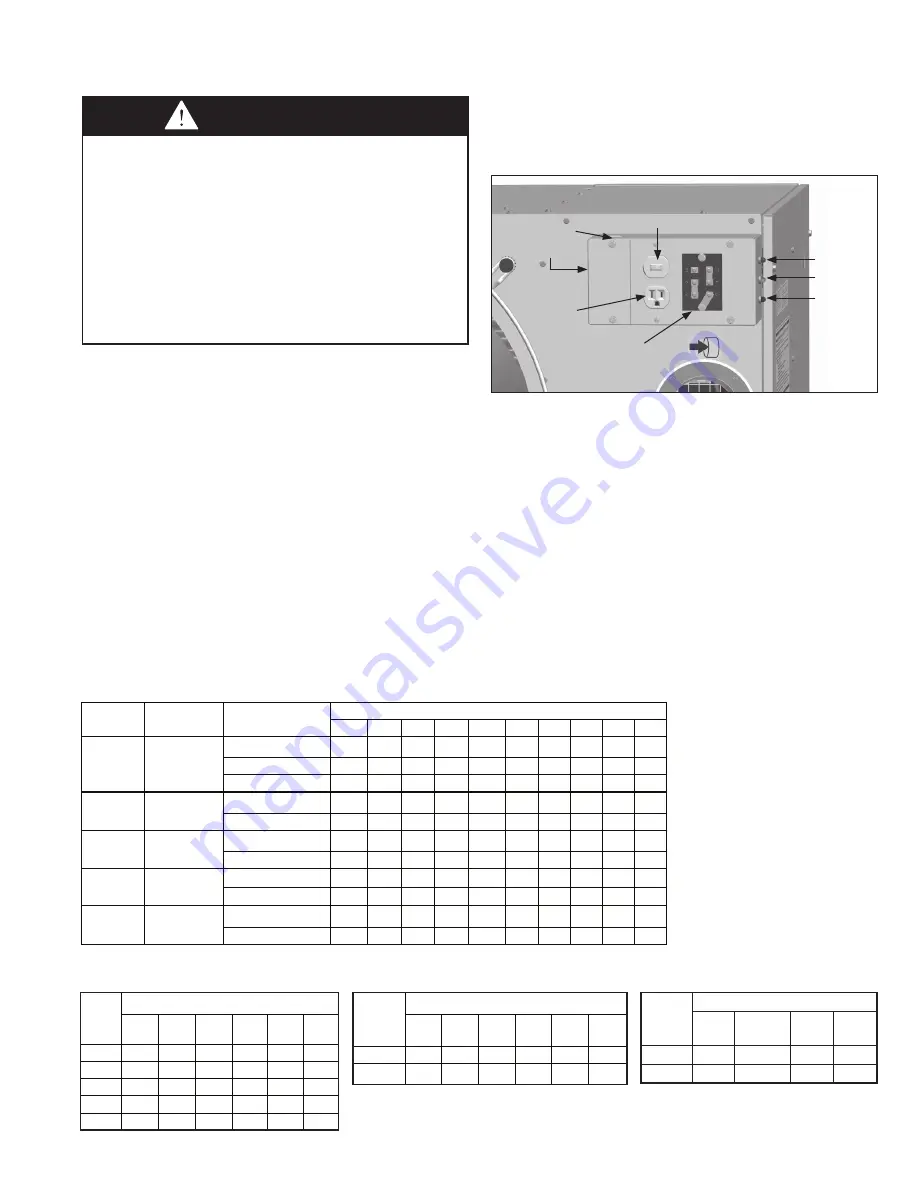
17
6-563.7
eleCTrICAl ConneCTIons
WARNING
1. Disconnect power supply before making wiring connections
to prevent electrical shock and equipment damage.
2. All appliances must be wired strictly in accordance with
wiring diagram furnished with the appliance. Any wiring
different from the wiring diagram could result in a hazard
to persons and property.
3. Any original factory wiring that requires replacement must
be replaced with wiring material having a temperature
rating of at least 105°C.
4. Ensure that the supply voltage to the appliance, as
indicated on the serial plate, is not 5% greater than or
5% less than the rated voltage.
1. Installation of wiring must conform with local building codes, or in
the absence of local codes, with the National Electric Code ANSI/
NFPA 70 - Latest Edition. Unit must be electri cally grounded in
conformance to this code. In Canada, wiring must comply with
CSA C22.1, Part 1, Electrical Code.
2. Two copies of the unit wiring diagram are provided with each unit.
One is located in the side access control compartment and the
other is supplied in the literature packet. Refer to this diagram for
all wiring connections.
3. Make sure all multi-voltage components (motors, transform ers,
etc.) are wired in accordance with the power supply voltage.
4. The power supply to the unit must be protected with a fused or
circuit breaker switch.
5. The power supply must be within 5 percent of the voltage rating
and each phase must be balanced within 2 percent of each other.
If not, advise the utility company.
6. External electrical service connections that must be installed
include:
a. Supply power connection (115, 208, 230, 460, or 575 volts).
b. Connection of thermostats, or any other accessory control
devices that may be supplied (24 volts).
InsTAllATIon - eleCTrICAl ConneCTIons
Table 17.1 - Propeller unit model PTC operating electrical data
➀
Table 17.2 - Blower model BTC motor
Amp
draw
Table 17.3 - Blower model BTC Control
Circuit Amp draw
➁
Table 17.4 - Blower model BTC
Accessory Transformer size (kvA)
➂
➀
Amp draw data shown is operating amp
draw at incoming power. For units that
use a field installed accessory step-down
transformer as noted, the amp draw
shown is the primary side operating amp
draw. For sizing of circuit protection for
equipment with transformers, please refer
to the National Electric Code.
➁
For BTC models, add the Motor Amp
Draw and Control Circuit Amp Draw to get
the Total Unit Amp Draw.
➂
Transformers for blower models are
typically smaller than those used for
propeller models, as the transformer is
not needed for the blower motor.
noTe: All units with supply voltage 208V and greater must use a
field installed step-down transformer, available as a separate
accessory. Refer to Tables 17.1 and 17.4 for additional
information on the required transformer.
7. Refer to Figure 17.1 for the junction box wiring entry location.
8. All supply power electrical connections are made in the junction
box compartment of the unit. The low voltage (thermostat and
accessory control devices) can be wired to the terminals on the
junction box.
Additional notes for the Condensate Pump outlet:
9. The condensate pump outlet supplied with this unit is intended for
use with a condensate pump with operating amps not to exceed
2 Amps.
10. The condensate pump cutlet can be used as a service outlet. To
be used as a service outlet, the disconnect switch located above
the outlet must be in the OFF position to disable the unit heater
power and gas control circuits to prevent equipment damage.
When the unit is wired directly to a 115V power supply, the outlet
is rated for a maximum load of 20 amps at 115V. If this unit has
been provided with an accessory step-down transformer to 115V
from a higher supply voltage, ensure that the load plugged into
the outlet does not exceed 8A for 1.0kVA or 12A for 1.5kVA rated
transformers.
Supply Power
Conduit Entry
Knockouts
Unit On/Off Switch
Condensate
Pump Outlet
Terminal Board
for Low Voltage
Control Wiring
unit status
lights:
Green =
Power On
Amber =
Call for Heat
Blue =
Burner On
supply
voltage
Power
Code
model PTC sizes
55
65
85 110 135 156 180 215 260 310
115V
1 Phase
01 (115V)
m
otor Amps
2.20 2.20 2.20 4.60 4.60 4.60 4.60 7.00 8.80 8.80
Total Amps
4.35 4.35 4.35 6.75 6.75 6.75 6.75 9.15 10.95 9.85
Transformer kvA n/a
n/a n/a n/a
n/a
n/a n/a n/a n/a n/a
208V
1 or 3
Phase
01 (115V)
with
Transformer
Transformer kvA 1.00 1.00 1.00 1.00 1.00 1.00 1.00 1.50 1.50 1.50
208v Total Amps
2.41 2.41 2.41 3.73 3.73 3.73 3.73 5.06 6.05 5.45
230V
1 or 3
Phase
01 (115V)
with
Transformer
Transformer kvA 0.75 0.75 0.75 1.00 1.00 1.00 1.00 1.50 1.50 1.50
230v Total Amps
2.18 2.18 2.18 3.38 3.38 3.38 3.38 4.58 5.48 4.93
460V
3 Phase
01 (115V)
with
Transformer
Transformer kvA 0.75 0.75 0.75 1.00 1.00 1.00 1.00 1.50 1.50 1.50
460v Total Amps
1.09 1.09 1.09 1.69 1.69 1.69 1.69 2.29 2.74 2.46
575V
3 Phase
01 (115V)
with
Transformer
Transformer kvA
0.75 0.75 0.75 1.00 1.00 1.00 1.00 1.50 1.50 1.50
575v Total Amps
0.87 0.87 0.87 1.35 1.35 1.35 1.35 1.83 2.19 1.97
motor
HP
supply voltage
115v/
1ph
230v/
1ph
208v/
3ph
230v/
3ph
460v/
3ph
575v/
3ph
1
14.00 7.00 3.20 3.20 1.60 1.30
1-1/2 15.00 7.50 4.60 4.80 2.40 1.90
2
-
-
6.00 5.80 2.90 2.30
3
-
-
8.40 7.80 3.90 3.20
5
-
-
13.60 12.30 6.20 5.10
model
size
supply voltage
115v/
1ph
230v/
1ph
208v/
3ph
230v/
3ph
460v/
3ph
575v/
3ph
215-260 2.15 1.08 1.19 1.08 0.54 0.43
310
1.05 0.53 0.58 0.53 0.26 0.21
model
size
supply voltage
208v
3 ph
230v
1 or 3 ph
460v
3 ph
575v
3 ph
215-260 0.50
0.50
0.50
0.50
310
0.50
0.25
0.25
0.25
figure 17.1 - Power/Control Wiring