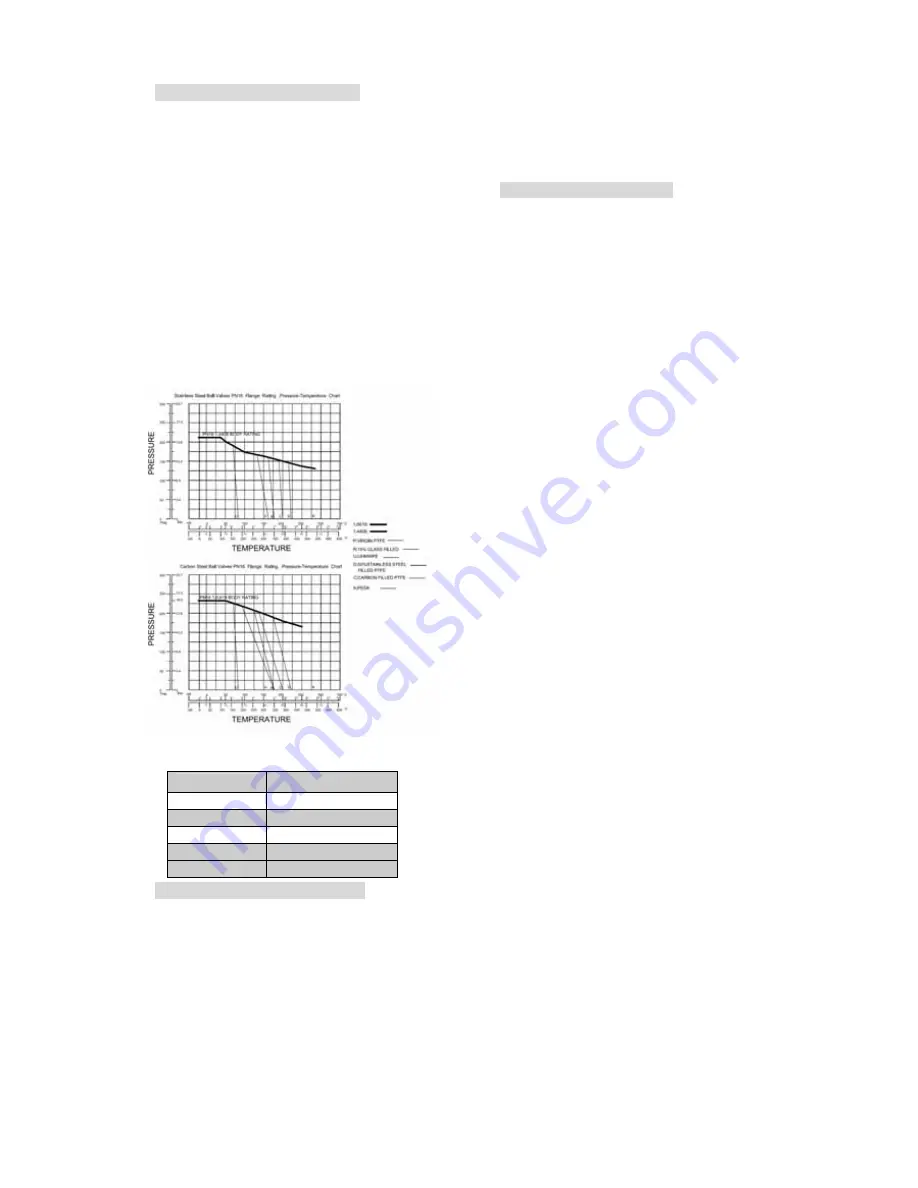
4
3. Pressure-Temperature Ratings
The pressure-temperature rating of GLOBE
Valves are determined, not only by valve shell
materials, but also by sealing materials used for
Gasket, and stem packing. Sealing materials
may be high molecule, elasticity and hardness,
however, the choice is limited by the
characteristics of the service fluid, temperature,
pressure, velocity of fluid, frequency of valves
operation and sizes of valves etc, Followings
are the general rating chart for non-shock fluid
service for Globe Valves distinguished by
nominal pressure and sealing materials.
Temp.
(°C)
PN16 Bar
-20 to 0
14.7
0 to 50
14.3
50 to 100
12.0
100 to 150
11.2
150 to 200
10.3
4. Delivery Condition and Storage
Valves stay in the open condition during the
transportation, such that the seating material
is not in compression. Valves are drained of
any test liquid. The body ends are covered to
prevent the introduction of foreign materials
and moisture.
Valves must store in an indoor warehouse to
avoid dusts and other foreign object. The
elastomeric seating shall be protected from
ultra violet light. Do not exposed in an open
space without body end cover. Do not take
off the packing under an unnecessary
situation.
5. Installation and Operation
5.1 Cleaning
Even the valves was transported under a clean
environment, operator must Globe is there any
foreign body or dusts inside the bore. If yes,
clean it before installation. Operator clean the
valves by water, compression air, or steam
(automation valve shall be cleaned only with
water or steam, the compression air is not
allowed.)
5.2 Thread cutting
Care should be taken not to thread-cut the
pipes excessively. Care should be taken not to
over-tighten the pipe connected to the valve. If
the pipe is inadvertently screwed deep into the
thread chamber of the valve, it may deform the
body disc. Prior to pipe connection, remove all
foreign material deposits, such as mud, rust, oil
and swarf, from the thread-cut portion of the
pipe. Prior to pipe connection, remove sand,
mud, molten spatter deposits and any other
foreign materials from the interior of the pipes
to be connected to the valve
5.3 Valve Installation
a. Remove any swarf from the thread-cut
portion of the pipe, then wrap with Teflon tap, or
apply a thin coat of an appropriate liquid
sealant (pipe compound), to that portion. The
liquid sealant should be selected with due
consideration to the kind and temperature of
the fluid, and must be applied on the thread of
the pipe.
b. When a screwed-end valve will be
connected to the pipe, be sure to hold the pipe
in the pipe vice and screw the valve onto it. In
this case, always apply the wrench to the
connected end of the valve Connecting to
pipeline
c.Select the correct specification of bolts to
fasten the flange with pipeline. Following table
Summary of Contents for GLOBE Series
Page 5: ...3 f Dimensions Parts List ...