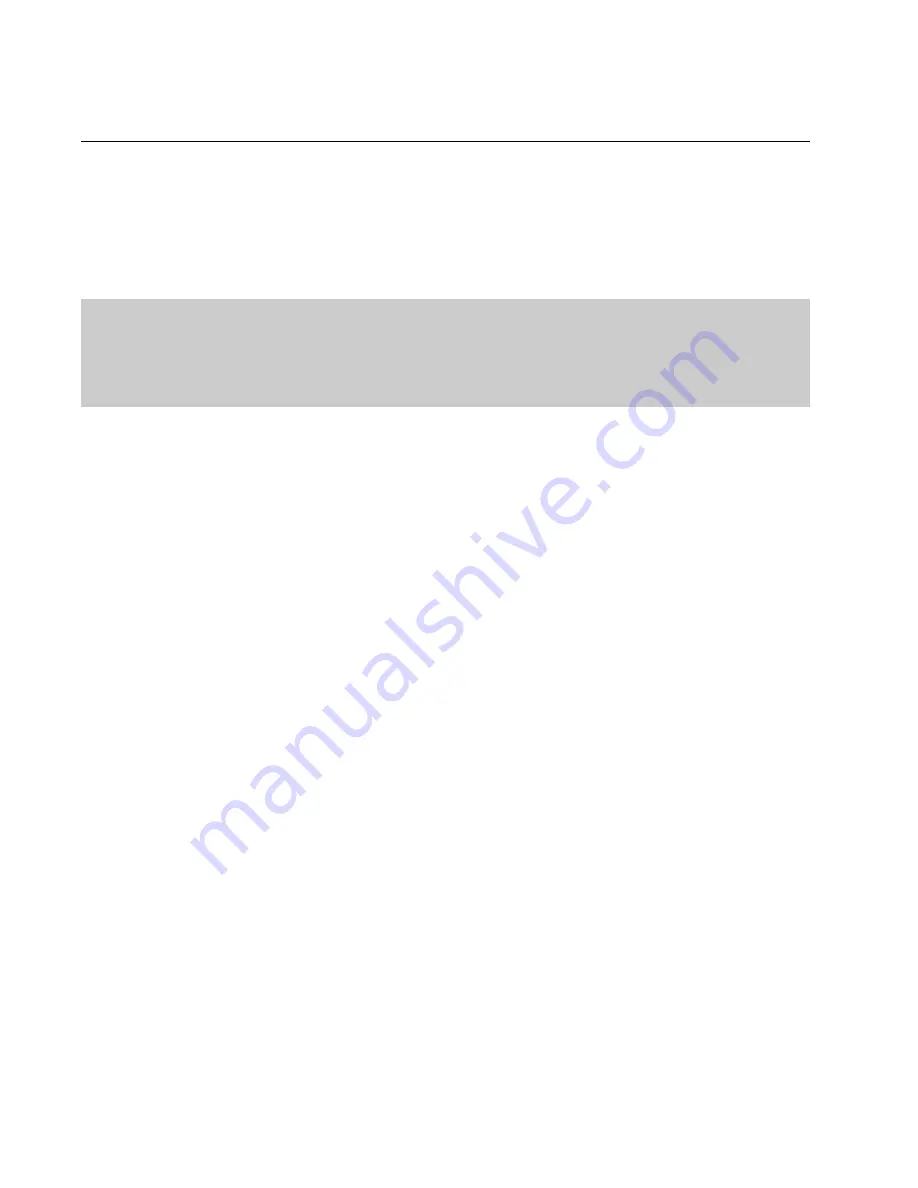
36
Visit our website at http://modeltech.globalhobby.com or for Customer Service at http://globalservices.globalhobby.com
SECTION 25: FLYING THE MAGIC EXTRA 300L
The Magic Extra 300L ARF is designed for those pilots who are experienced at flying sport models. It is not a trainer. If you
do not feel comfortable about test-flying the airplane, don't hesitate to ask someone more experienced for help.
When set up for test-flying, the Magic Extra 300L is much like flying any other sport aerobatic airplane. It's a nimble flyer
that has a low wing loading. This makes it predictable during slow flight and landing. Because it uses very large control
surfaces you need to remember not to over-control. For general sport flying, we recommend you use the "Test-Flying"
control throws - and even then, you will not need to move the sticks very far.
WARNING
Because of the extremely large control surfaces and high power-to-weight ratio, control surface flutter is a possibility.
To prevent any chance of control surface flutter, always reduce engine power during down-leg maneuvers. Never fly the
airplane at full throttle in a downward attitude. Doing so can over-speed the airplane and cause control surface flutter,
which can quickly lead to airframe damage and/or a crash.
TAKE-OFF
Because the Magic Extra 300L is light and has a lot of power, it sometimes seems like it wants to take off by itself. Do be
aware that it's still important to let the airplane get up to flying speed before lifting off the ground. Lifting the airplane off the
ground too fast will cause the airplane to stall and crash. You should allow the airplane to roll out until the tail is completely
off the ground and flying, and then gently pull the airplane off the ground and into a shallow climb.
Because of the torque of the engine, the airplane will have a natural tendency to pull to the left when it is accelerating down
the runway. You will need to compensate for this by applying and holding right rudder during the takeoff roll. Once the
airplane lifts off the ground, you can release the right rudder. Because of the wide landing gear stance and long tail
moment you will find the ground handling of the Magic Extra 300L very smooth and predictable.
IN THE AIR
In the air the Magic Extra 300L is as smooth and docile or as wild and aerobatic as you want it to be. With the control
throws set to the "Test-Flying" settings, the airplane is smooth throughout the entire flight envelope, even while moving the
control sticks to the corners. Most flyers interested in sport-flying will probably want to keep the control throws set to the
"Test-Flying" settings for most maneuvers.
Setting the control throws to the "Aerobatic Flying" settings opens up a whole new dimension to the airplane. With these
settings the airplane becomes extremely responsive in all attitudes, even at very low rates of speed. Thanks to the
extremely large control surfaces, 3D style manuevers can be performed without hesitation. We suggest that if you use the
"Aerobatic Flying" settings, you make these your "high rates" and make the "Test-Flying" settings your "low rates." This
way, for take-off, general flying and landing you can use low rates, and for 3D flying you can flip to high rates.
LANDING
Just because the Magic Extra 300L is so aerobatic doesn't mean it's difficult to land. We've designed the airplane so it will
slow down to a practical crawl without tip stalling. Because of this design, landings are quite slow and predictable. There
is no tendency to tip stall, but we do recommend that you land with a small amount of power. It's not good practice to just
chop the power and dive the airplane to the runway.
On your initial upwind leg, reduce power and allow the airplane to begin slowing down. Follow your normal landing
procedure, allowing the airplane to gradually lose altitude and speed. When turning onto final approach the airplane
should have a slightly nose-down attitude and you should be carrying a small amount of power to control your descent.
Just before touch-down, reduce power to idle and let the airplane settle onto the main gear. If you flair too much or try for
a three point landing, the airplane will have a tendency to balloon up and possibly stall if it's too slow. As always, when
landing be careful not to over-control. Over-controlling leads to excessive oscillations which don't make for good landings.