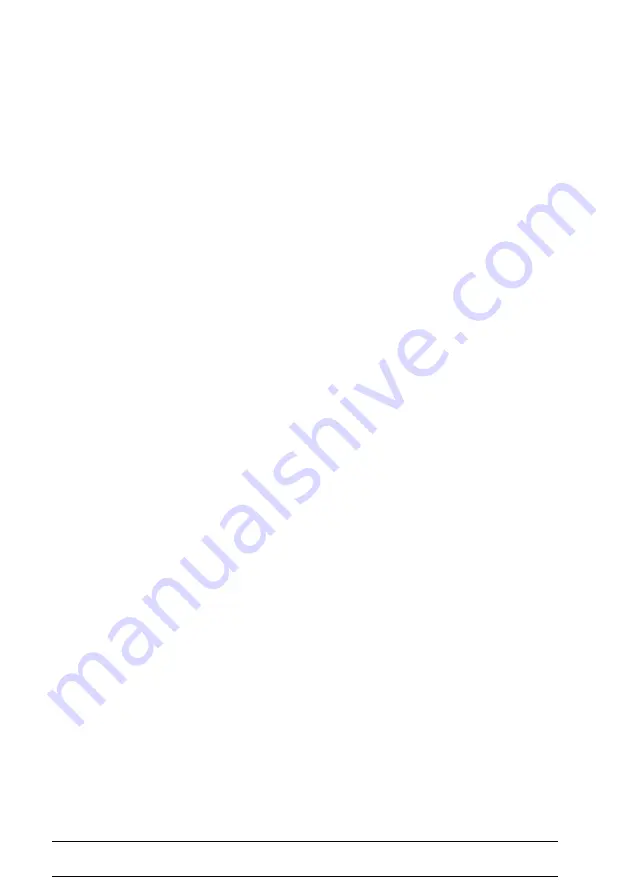
PAS Trolley Manual
LP101017 Rev 1.02
Page ii
4.7. Inlet System...........................................................................................22
4.8. Operation via flexible connection .........................................................22
4.9. Operation with remote mounted analyser..............................................23
4.10. Operation with atmospheric inlet ........................................................24
Section 5.
Troubleshooting
............................27
Section 6.
Troubleshooting
............................31
6.1. General ..................................................................................................31
6.2. Primary Pump........................................................................................31
6.3. Turbo Pump...........................................................................................31
6.4. Cold Cathode Gauge .............................................................................31
6.5. RGA Head.............................................................................................32
6.6. Service/Repair .......................................................................................32
Appendix 1.
Related documents
..................35
Appendix 2.
Returns form
..................................37
Summary of Contents for Spectra 138A
Page 10: ...PAS Trolley Manual LP101017 Rev 1 02 Page ii This page is deliberately left blank ...
Page 17: ...PAS Trolley Manual LP101017 Rev 1 02 Page 9 This page is deliberately left blank ...
Page 19: ...PAS Trolley Manual LP101017 Rev 1 02 Page 11 ...
Page 20: ...PAS Trolley Manual LP101017 Rev 1 02 Page 12 This page is deliberately left blank ...
Page 21: ...PAS Trolley Manual LP101017 Rev 1 02 Page 13 ...
Page 22: ......
Page 25: ...PAS Trolley Manual LP101017 Rev 1 02 Page 17 ...
Page 26: ......
Page 34: ......
Page 38: ......
Page 41: ...PAS Trolley Manual LP101017 Rev 1 02 Page 33 ...
Page 42: ......
Page 44: ...PAS Trolley Manual LP101017 Rev 1 02 Page 36 This page is deliberately left blank ...