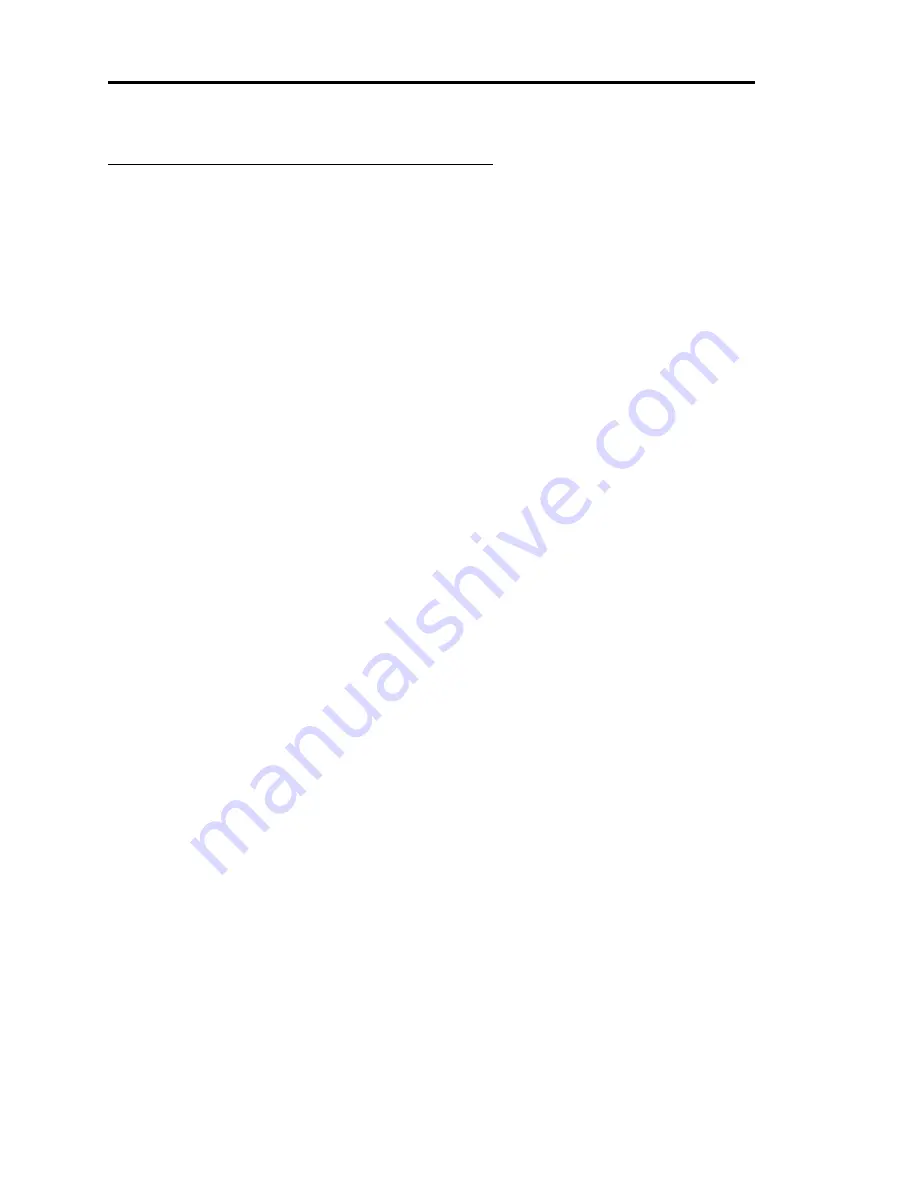
How To Respond To a Checksum Error
Chapter Six: Remote Operation
80
How To Respond To a Checksum Error
A checksum error message indicates the controller has detected a calibration problem. The
controller send a checksum error message in the following circumstances:
•
at system power up
•
in response to the R52 checksum command (1 = error)
If the controller detects a checksum error, perform a full calibration to correct the problem.
To perform a full calibration:
1. Zero the analog set point.
Perform the steps described in How To Zero the Analog Set Point, page 77.
2. Learn the analog set point full scale.
Perform the steps described in How To Learn Analog Set Point Full Scale, page 77.
3. Calibrate the span of the A/D converter.
Perform the steps described in How To Calibrate Span of the A/D Converter, page 79.
If the checksum error persists after you perform a full calibration, the error indicates a hardware
failure of the EEPROM. Contact any MKS Service Center, listed on the inside back cover of this
manual, for assistance.
Summary of Contents for 651C
Page 12: ...List of Figures x...
Page 14: ...List of Tables xii...
Page 34: ...Customer Support Chapter One General Information 20 This page intentionally left blank...
Page 110: ...Digital Logic Control Chapter Six Remote Operation 96 This page intentionally left blank...
Page 170: ...Safety Information Page 6 of 8 This page intentionally left blank...