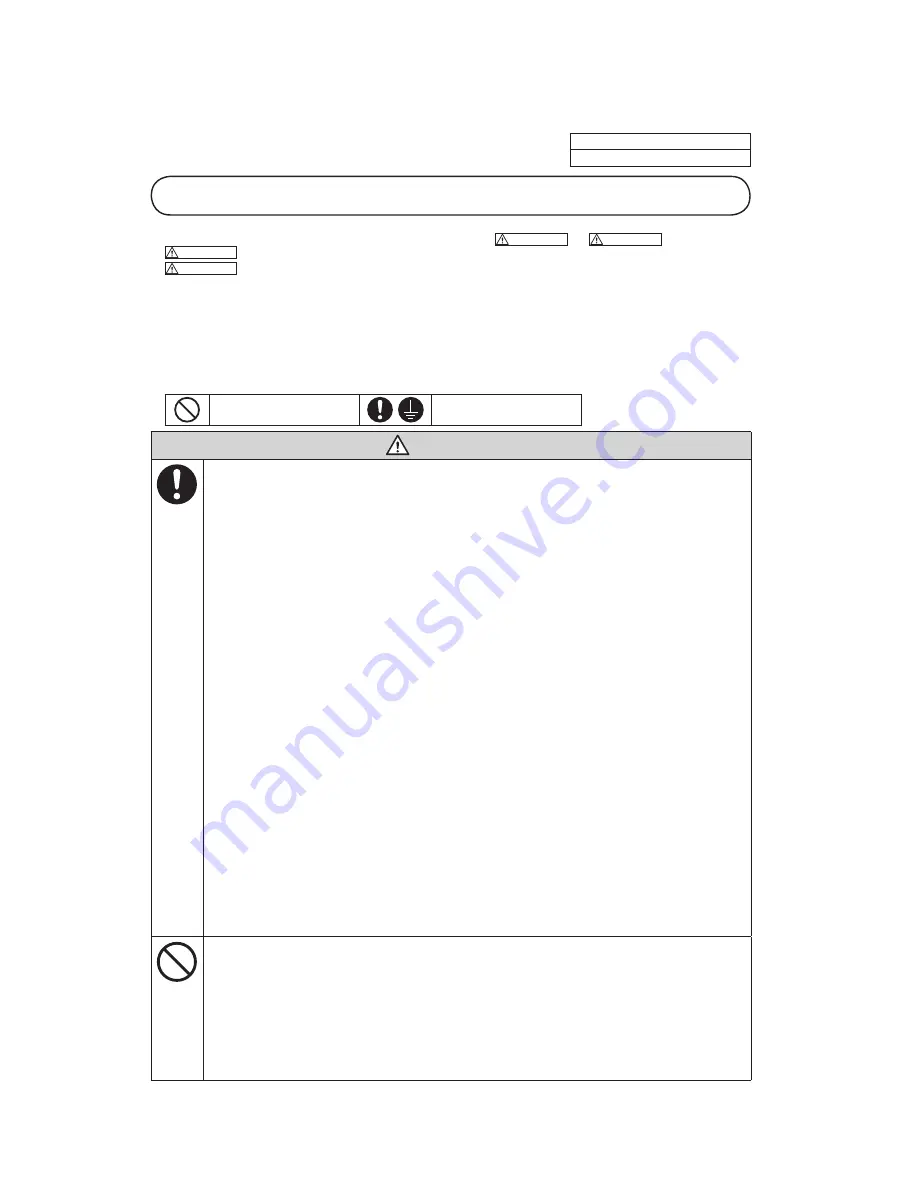
-
-
'14•SRK-T-164
6. APPLICATION DATA
– 28 –
Safety precautions
WALL TYPE AIR CONDITIONER
R410A REFRIGERANT USED
Read the “Safety precautions” carefully first of all and strictly follow it during the installation work in order to protect yourself.
v
The precautionary items mentioned below are distinguished into two levels,
v
WARNING
and
CAUTION
.
WARNING
: Wrong installation would cause serious consequences such as injuries or death.
CAUTION
: Wrong installation might cause serious consequences depending on circumstances.
Both mentions the important items to protect your health and safety so strictly follow them by any means.
Be sure to confirm no anomaly on the equipment by commissioning after completed installation and explain the operating methods as
v
well as the maintenance methods of this equipment to the user according to the user’s manual.
Keep the installation manual together with user’s manual at a place where any user can read at any time. Moreover if necessary, ask
v
to hand them to a new user.
For installing qualified personnel, take precautions in respect to themselves by using suitable protective clothing, groves, etc., and then
v
perform the installation works.
Please pay attention not to fall down the tools, etc. when installing the unit at the high position.
v
If unusual noise can be heard during operation, consult the dealer.
v
The meanings of “Marks” used here are shown as follows:
v
Never do it under any
circumstances.
Always do it according to the
instruction.
WARNING
Installation must be carried out by the qualified installer.
v
If you install the system by yourself, it may cause serious trouble
such as water leaks, electric shocks, fire and personal injury, as a
result of a system malfunction. Do not carry out the installation and
maintenance work except the by qualified installer.
Install the system in full accordance with the installation
v
manual.
Incorrect installation may cause bursts, personal injury, water leaks,
electric shocks and fire.
Be sure to use only for household and residence.
v
If this appliance is installed in inferior environment such as machine
shop and etc., it can cause malfunction.
Use the original accessories and the specified components for
v
installation.
If parts other than those prescribed by us are used, it may cause
water leaks, electric shocks, fire and personal injury.
Install the unit in a location with good support.
v
Unsuitable installation locations can cause the unit to fall and cause
material damage and personal injury.
Ensure the unit is stable when installed, so that it can withstand
v
earthquakes and strong winds.
Unsuitable installation locations can cause the unit to fall and cause
material damage and personal injury.
Ventilate the working area well in the event of refrigerant
v
leakage during installation.
If the density of refrigerant exceeds the limit, please consult the
dealer and install the ventilation system, otherwise lack of oxygen
can occur, which can cause serious accident.
When installing in small rooms, take prevention measures not
v
to exceed the density limit of refrigerant in the event of leakage,
referred by the formula (accordance with ISO5149).
If the density of refrigerant exceeds the limit, please consult the
dealer and install the ventilation system, otherwise lack of oxygen
can occur, which can cause serious accident.
After completed installation, check that no refrigerant leaks
v
from the system.
If refrigerant leaks into the room and comes into contact with an
oven or other hot surface, poisonous gas is produced.
Use the prescribed pipes, flare nuts and tools for R410A.
v
Using existing parts (for R22 or R407C) can cause the unit failure
and serious accidents due to burst of the refrigerant circuit.
Tighten the flare nut by torque wrench with specified method.
v
If the flare nut were tightened with excess torque, this may cause
burst and refrigerant leakage after a long period.
Do not open the operation valves for liquid line and gas line
v
until completed refrigerant piping work, air tightness test and
evacuation.
If the compressor is operated in state of opening operation valves
before completed connection of refrigerant piping work, air can be
sucked into refrigerant circuit, which can cause burst or personal
injury due to anomalously high pressure in the refrigerant.
The electrical installation must be carried out by the qualified
v
electrician in accordance with “the norm for electrical work” and
“national wiring regulation”, and the system must be connected
to the dedicated circuit.
Power supply with insufficient capacity and incorrect function done
by improper work can cause electric shocks and fire.
Be sure to shut off the power before starting electrical work.
v
Failure to shut off the power can cause electric shocks, unit failure or
incorrect function of equipment.
Be sure to use the cables conformed to safety standard and
v
cable ampacity for power distribution work.
Unconformable cables can cause electric leak, anomalous heat
production or fire.
This appliance must be connected to main power supply by
v
means of a circuit breaker or switch (fuse 21 series: 20A,
26 series: 25A) with a contact separation of at least 3mm.
When plugging this appliance, a plug conforming to the norm
v
IEC60884-1 must be used.
Use the prescribed cables for electrical connection, tighten
v
the cables securely in terminal block and relieve the cables
correctly to prevent overloading the terminal blocks.
Loose connections or cable mountings can cause anomalous heat
production or fire.
Arrange the wiring in the control box so that it cannot be
v
pushed up further into the box. Install the service panel
correctly.
Incorrect installation may result in overheating and fire.
Be sure to fix up the service panels.
v
Incorrect fixing can cause electric shocks or fire due to intrusion of
dust or water.
Be sure to switch off the power supply in the event of
v
installation, inspection or servicing.
If the power supply is not shut off, there is a risk of electric shocks,
unit failure or personal injury due to the unexpected start of fan.
Stop the compressor before removing the pipe after shutting
v
the service valve on pump down work.
If the pipe is removed when the compressor is in operation with the
service valve open, air would be mixed in the refrigeration circuit and
it could cause explosion and injuries due to abnormal high pressure
in the cooling cycle.
Only use prescribed option parts. The installation must be
v
carried out by the qualified installer.
If you install the system by yourself, it can cause serious trouble
such as water leaks, electric shocks, fire.
Be sure to wear protective goggles and gloves while at work.
v
Earth leakage breaker must be installed.
v
If the earth leakage breaker is not installed, it can cause electric
shocks.
Do not put the drainage pipe directly into drainage channels
v
where poisonous gases such as sulphide gas can occur.
Poisonous gases will flow into the room through drainage pipe and
seriously affect the user’s health and safety. This can also cause the
corrosion of the indoor unit and a resultant unit failure or refrigerant
leak.
Ensure that no air enters in the refrigerant circuit when the unit
v
is installed and removed.
If air enters in the refrigerant circuit, the pressure in the refrigerant
circuit becomes too high, which can cause burst and personal injury.
Do not bundling, winding or processing for the power cord. Or,
v
do not deforming the power plug due to tread it.
This may cause fire or heating.
Do not processing, splice the power cord, or share a socket
v
with other power plugs.
This may cause fire or electric shock due to defecting contact,
defecting insulation and over-current etc.
Do not vent R410A into the atmosphere : R410A is a fluorinated
v
greenhouse gas, covered by the Kyoto Protocol with Global
Warming Potential (GWP)=1975.
Do not run the unit with removed panels or protections.
v
Touching rotating equipments, hot surfaces or high voltage parts can
cause personal injury due to entrapment, burn or electric shocks.
Do not perform any change of protective device itself or its
v
setup condition.
The forced operation by short-circuiting protective device of pressure
switch and temperature controller or the use of non specified
component can cause fire or burst.
When install the unit, be sure to check whether the selection of installation place, power supply
specifications, usage limitation (piping length, height differences between indoor and outdoor
units, power supply voltage and etc.) and installation spaces.
RMA012A076A_En.indb 28
22-Jan-14 09:00:39
Summary of Contents for SRK19CNS-S
Page 2: ......
Page 3: ...14 SRK T 164 TECHNICAL MANUAL...
Page 12: ...10 14 SRK T 164 3 Wireless remote control Unit mm 60 17 3 150 Unit mm 60 17 3 150...
Page 40: ...38 14 SRK T 164 4 Troubleshooting procedure If the air conditioner runs NO YES 39...
Page 48: ...46 14 SRK T 164...
Page 53: ...51 14 SRK T 164 MEMO...
Page 59: ...57 14 SRK T 164 MEMO...
Page 62: ...60 14 SRK T 164 CRBE0393 14 2 5 3 6 7 8 9 11 13 4 17 12 15 15 16 15 15 10 1 18 PANEL FAN ASSY...