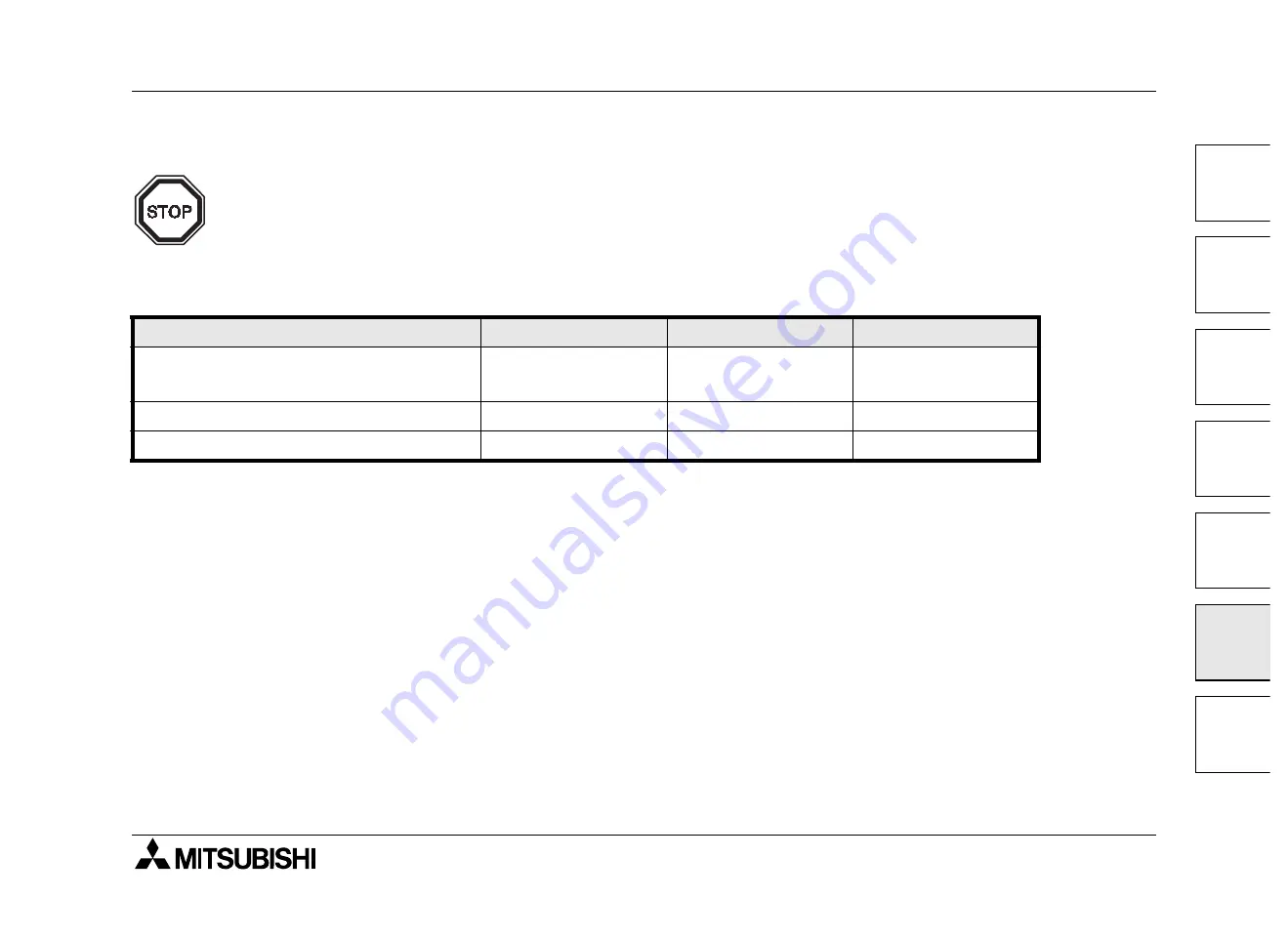
FX1S Series Programmable Controllers
Outputs 6
6-3
1
2
3
4
5
6
7
6.2.1
Reliability Tests
The test results in Table 6.2 were gathered from a 1 sec ON/OFF test cycle. Please note that
the over current induced by in-rush greatly reduces the relay contact’s service life. The rated
life for an inductive AC load such as a contactor or solenoid valve is 500,000 operations at
20VA.
Table 6.2: Relay Life Cycle Data
Description
20VA
35VA
80VA
Load capacity
0.2A/100VAC
0.1A/200VAC
0.35A/100V AC
0.17A/240V AC
0.8A/100V AC
0.4A/240V AC
Life of contact (cycles)
3,000,000
1,000,000
200,000
Example load (Mitsubishi contactor)
S-K10 ~ S-K95
S-K100 ~ S-K150
S-K180,S-K400