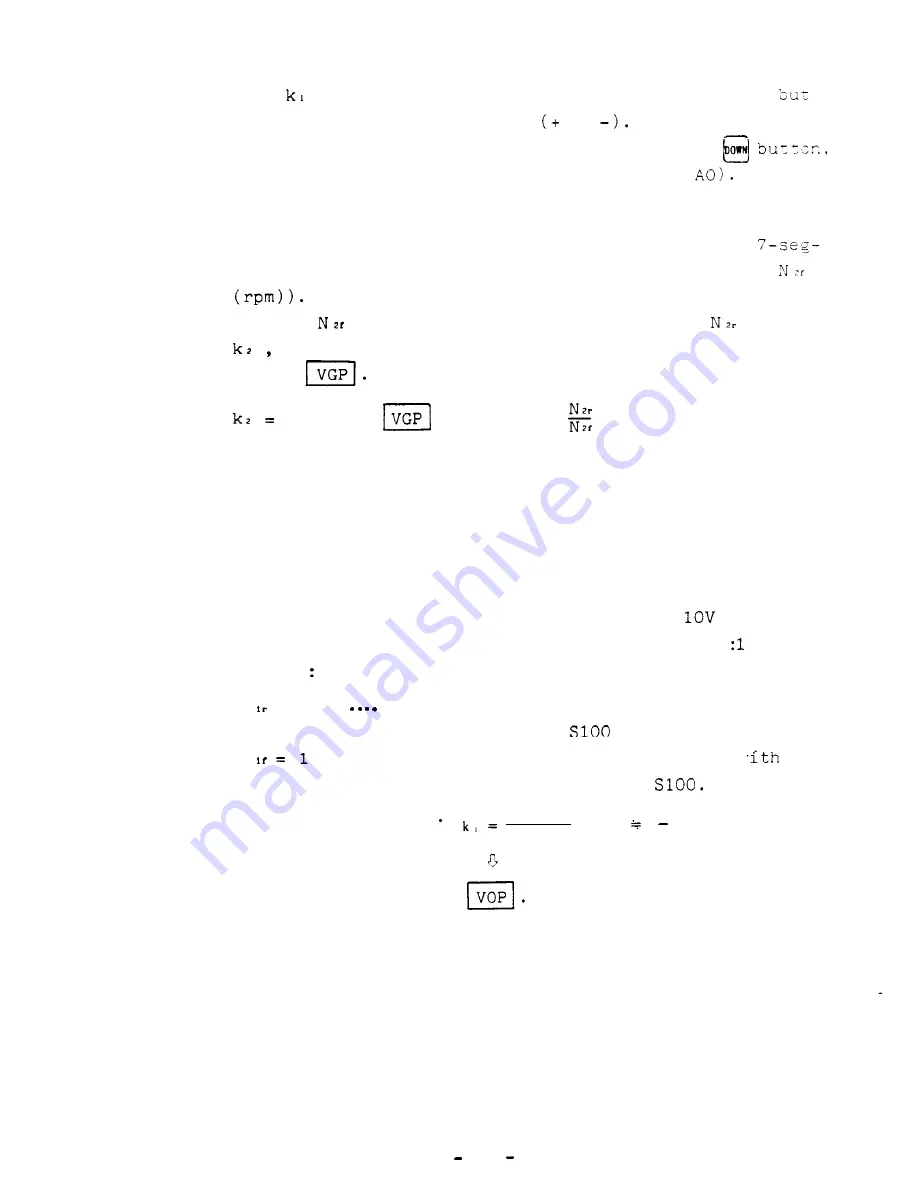
Note:
is either negative value or positive value,
not displayed with sign
or
When value can be incremented by pressing
the value is negative (for ROM version
(2) Set speed reference signal to the forward run maximum
speed and record the motor speed displayed by the
ment LED readout of controller (record the speed as
If this
is not equal to the desired speed
, set
determined from the following formula, for parameter
No.
OD
(Current
setting) x
(3) When the adjustment has been completed for forward run,
speed in reverse run should have been adjusted automati-
cally.
It is,
however,
recommended to verify that
specified reference speeds are always equal to true motor
speeds.
Ex.:
Let the rated motor speed be 8000rpm with
speed re-
ference signal,
and the reduction ratio be 2
(motor
speed
spindle speed)
. . . . . .
N = 200
Motor speed should be 200rpm with spindle
N
speed command of
188 . . . .
Reading of 7-segment LED readout w
spindle speed command of
188-200
. .
X
2048
3
8000
Set -3 for parameter
33