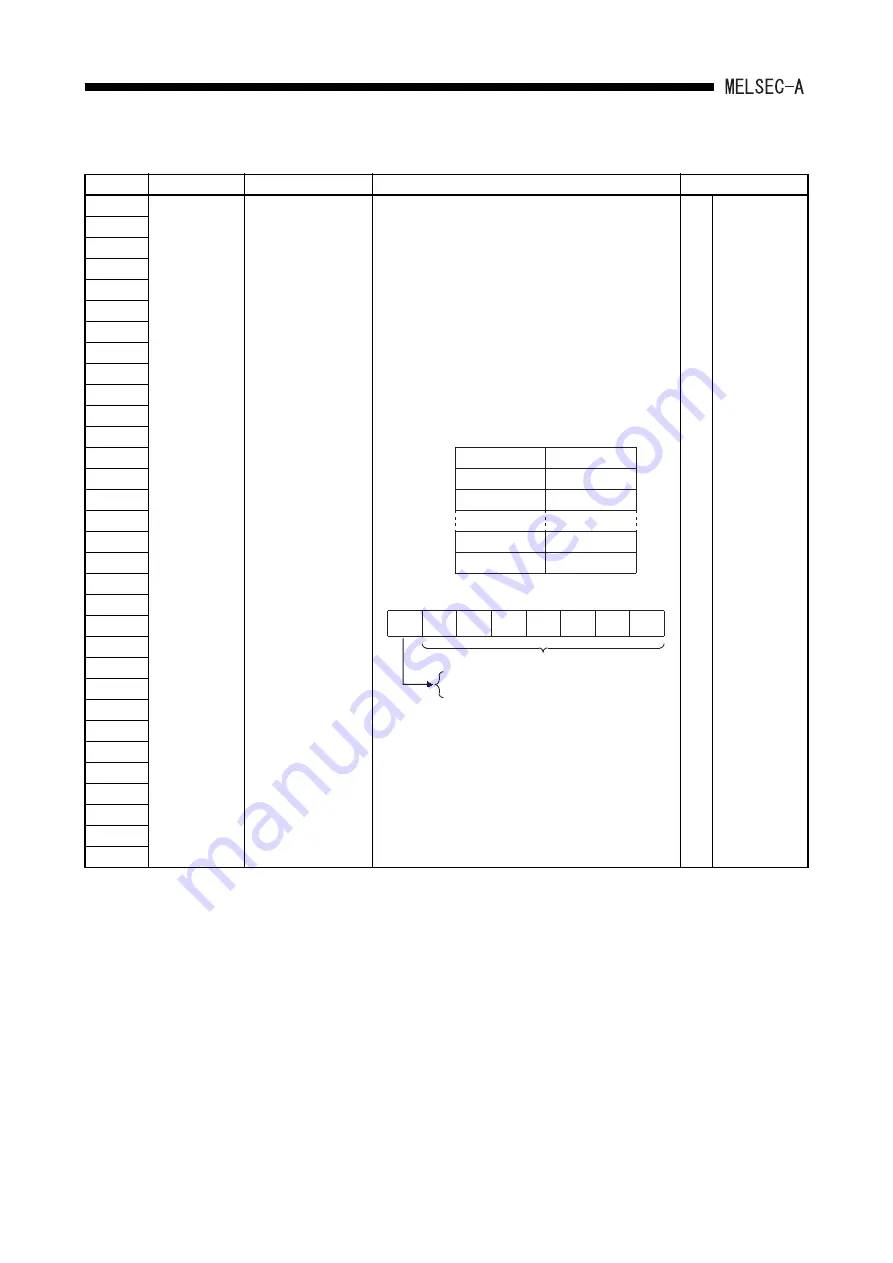
APP -
41
APPENDICES
Table App2.2 Special Register List (Continue)
Number
Name
Description
Details
Applicable CPU
D9141
Number of
times of retry
execution
Number of retries
• Stores the number of retries executed to I/O modules
or remote terminal modules which caused
communication error.
(Retry processing is executed the number of times set
at D9174.)
• Data becomes 0 when communication is restored to
normal.
• Station number setting of I/O modules and remote
terminal modules is as shown below.
• Retry counter uses 8 bits for one station.
* "n" is determined by station number of I/O module or
remote terminal module.
Odd number stations: b0 to b7 (n = 0)
Even number stations: b8 to b15 (n = 8)
—
Usable with
A2C and A52G.
D9142
D9143
D9144
D9145
D9146
D9147
D9148
D9149
D9150
D9151
D9152
D9153
D9154
D9155
D9156
D9157
D9158
D9159
D9160
D9161
D9162
D9163
D9164
D9165
D9166
D9167
D9168
D9169
D9170
D9171
D9172
b15 to b8
b7 to b0
D9141
Station 2
Station 4
Station 6
Station 62
Station 64
Station 1
Station 3
Station 5
Station 61
Station 63
D9142
D9171
D9172
D9143
b(n+7)
0/1
Number of retries
b(n+6)
b(n+5)
b(n+4)
b(n+3) b(n+2)
b(n+1)
b(n+0)
0: Normal
1: Station error
Summary of Contents for A2USCPU(S1)
Page 1: ......
Page 2: ......
Page 18: ...A 16 Memo...
Page 254: ...App 59 APPENDIX Appendix5 2 A1S61PN A1S62PN and A1S63P power supply modules Unit mm inch...
Page 271: ......
Page 272: ......