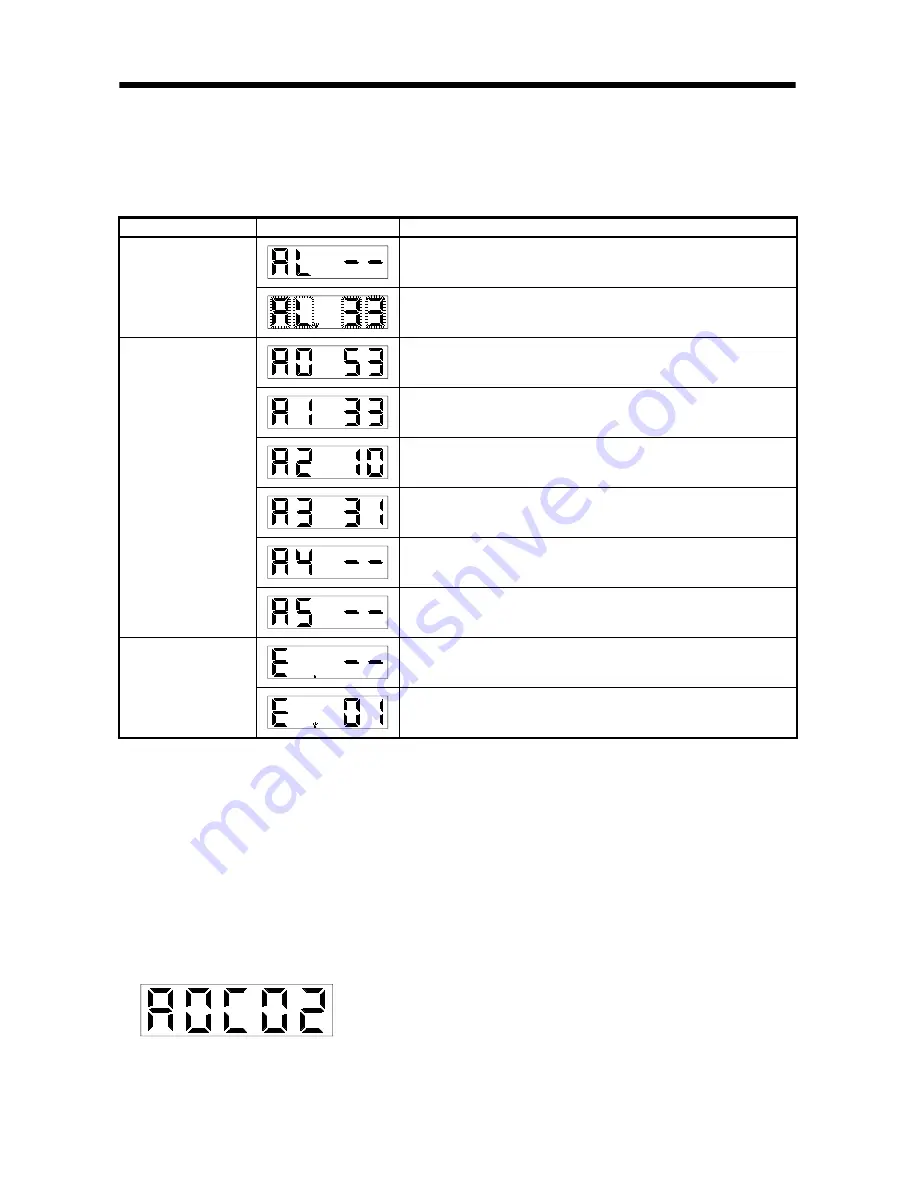
www.dadehpardazan.ir 88594014-15
4 - 7
4. OPERATION AND DISPLAY
4.2.4 Alarm mode of interface unit
The current alarm, past alarm history and parameter error are displayed. The lower 2 digits on the
display indicate the alarm number that has occurred or the parameter number in error. Display examples
are shown below.
Name
Display
Description
Indicates no occurrence of an alarm.
Current alarm
Indicates the occurrence of overvoltage (A.33).
Flickers at occurrence of the alarm.
Indicates that the last alarm is Multiple axis overload (A.53).
Indicates that the second alarm in the past is overvoltage (A.33).
Indicates that the third alarm in the past is undervoltage (A.10).
Indicates that the fourth alarm in the past is overspeed (A.31).
Indicates that there is no fifth alarm in the past.
Alarm history
Indicates that there is no sixth alarm in the past.
Indicates no occurrence of parameter error.
Parameter error No.
Indicates that the data of parameter No. 1 is faulty.
Functions at occurrence of an alarm
(1) Any mode screen displays the current alarm.
(2) Even during alarm occurrence, the other screen can be viewed by pressing the button in the operation
area. At this time, the decimal point in the fourth digit remains flickering.
(3) For any alarm, remove its cause and clear it in any of the following:
(a) Switch power OFF, then ON.
(b) Press the
"SET"
button on the current alarm screen.
(c) Turn on the alarm reset (RES) methods (for clearable alarms, refer to Section 9.1).
(4) Use IFU parameter No. 16 to clear the alarm history.
(5) Pressing
"SET"
button on the alarm history display screen for 2s or longer shows the following detailed
information display screen. Note that this is provided for maintenance by the manufacturer.
(6) Press
"UP"
or
"DOWN"
button to move to the next history.
Summary of Contents for MELSERVO-J2M series
Page 26: ...www dadehpardazan ir 88594014 15 1 10 1 FUNCTIONS AND CONFIGURATION MEMO ...
Page 36: ...www dadehpardazan ir 88594014 15 2 10 2 INSTALLATION AND START UP MEMO ...
Page 64: ...www dadehpardazan ir 88594014 15 3 28 3 SIGNALS AND WIRING MEMO ...
Page 74: ...www dadehpardazan ir 88594014 15 4 10 4 OPERATION AND DISPLAY MEMO ...
Page 112: ...www dadehpardazan ir 88594014 15 6 12 6 GENERAL GAIN ADJUSTMENT MEMO ...
Page 122: ...www dadehpardazan ir 88594014 15 7 10 7 SPECIAL ADJUSTMENT FUNCTIONS MEMO ...
Page 124: ...www dadehpardazan ir 88594014 15 8 2 8 INSPECTION MEMO ...
Page 186: ...www dadehpardazan ir 88594014 15 12 36 12 OPTIONS AND AUXILIARY EQUIPMENT MEMO ...
Page 190: ...www dadehpardazan ir 88594014 15 13 4 13 ABSOLUTE POSITION DETECTION SYSTEM MEMO ...