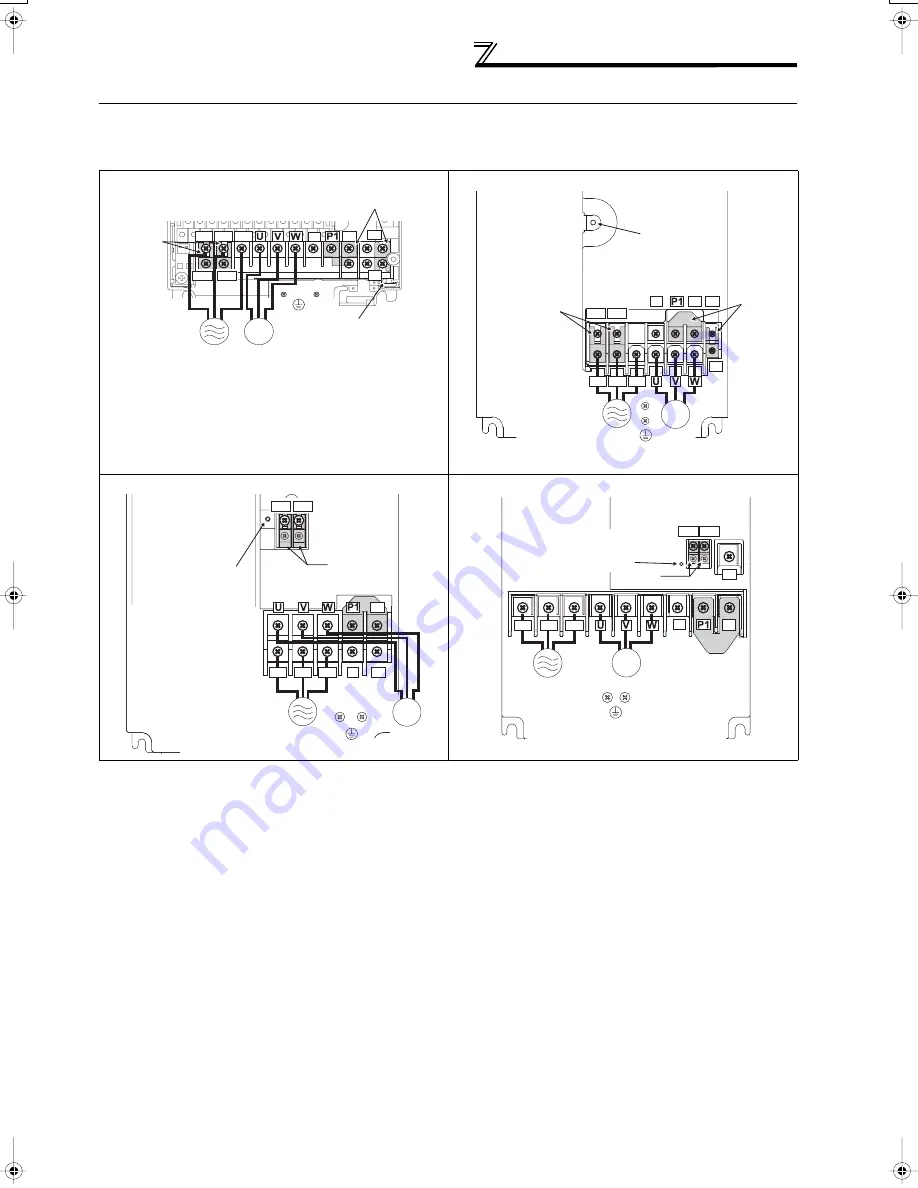
6
WIRING
3.3 Main circuit terminal
(1) Terminal layout and wiring
600V class
FR-A760-00017 to 00061-NA
FR-A760-00120-NA
FR-A760-00220-NA
FR-A760-00330-NA
R/L1 S/L2 T/L3
N/-
P/+
PR
PX
R1/L11 S1/L21
IM
Charge lamp
Jumper
Screw size (M4)
Screw size
(M4)
Jumper
Motor
Power
supply
R/L1 S/L2 T/L3
N/-
P/+ PR
PX
R1/L11 S1/L21
IM
Screw size
(M4)
Screw size
(M4)
Jumper
Jumper
Charge lamp
Motor
Power supply
R1/L11 S1/L21
R/L1 S/L2 T/L3
N/-
P/+
PR
Charge lamp
Jumper
Jumper
Screw size
(M4)
Screw size (M5)
Screw size (M5)
Power supply
IM
Motor
R/L1 S/L2 T/L3
N/-
P/+
PR
R1/L11 S1/L21
IM
Screw size (M4)
Screw size (M6)
Screw size (M6)
Jumper
Jumper
Charge lamp
Power supply
Motor
A760_installation_guideline_NA.book 6 ページ 2007年1月10日 水曜日 午前8時49分
Summary of Contents for FR-A760-00017-NA
Page 27: ...25 MEMO ...