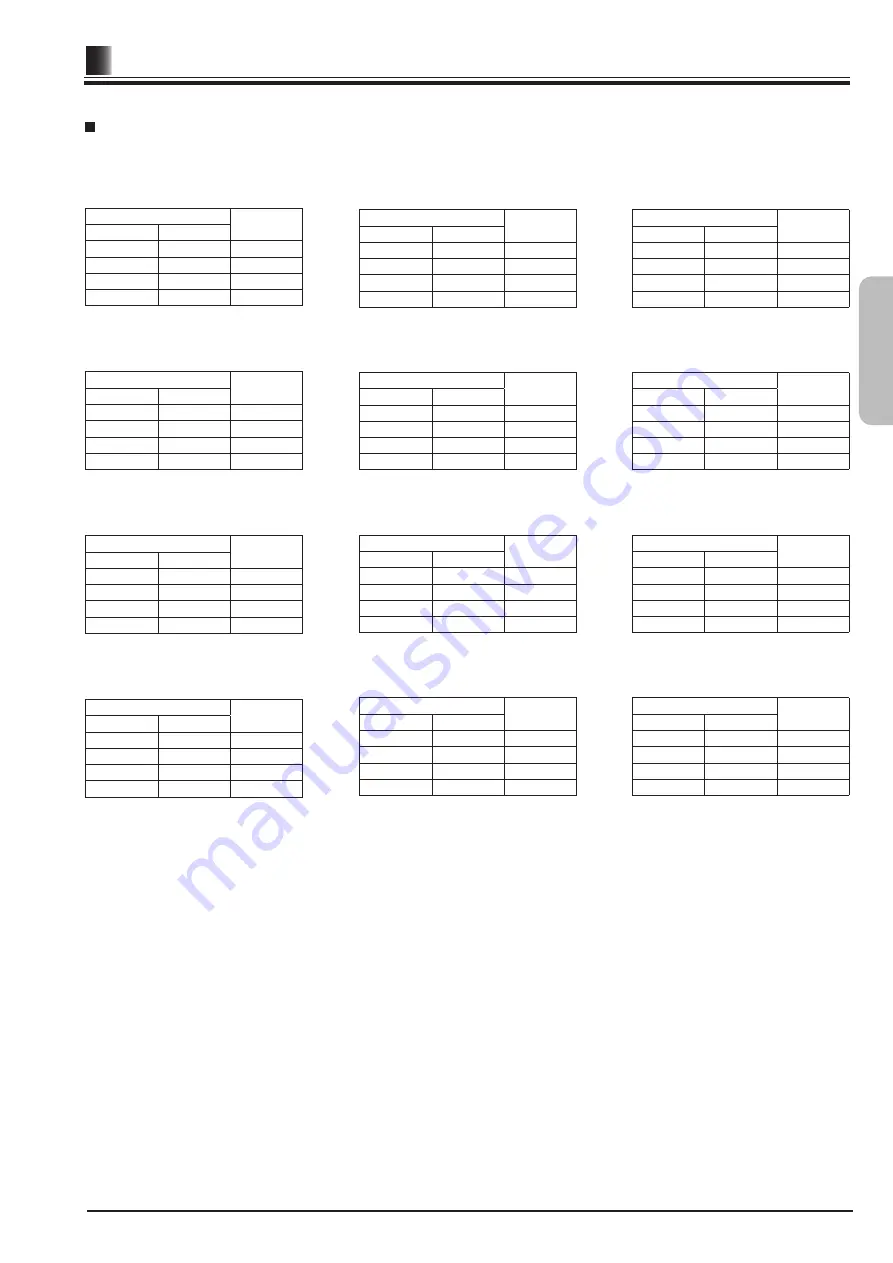
3.4 Water to Water Heat Pump (WTW)
EHWT17D-MHEDW
Flow rate
Ambient loop: 19.2 L/min Heating: 12.4 L/min
W10W35
Capacity
COP
%
kW
100%
6.5
5.7
75%
4.8
5.9
50%
3.2
5.7
25%
1.6
4.2
Ambient loop: 14.4 L/min Heating: 12.4 L/min
W15W35
Capacity
COP
%
kW
100%
7.4
6.4
75%
5.5
7.2
50%
3.7
6.6
25%
1.8
4.7
Ambient loop: 9.6 L/min Heating: 12.4 L/min
W20W35
Capacity
COP
%
kW
100%
7.5
6.8
75%
5.6
7.6
50%
3.7
7.2
25%
1.8
6.0
Ambient loop: 9.6 L/min Heating: 12.4 L/min
W25W35
Capacity
COP
%
kW
100%
8.3
8.4
75%
6.2
9.3
50%
4.1
9.2
25%
2.0
9.1
W10W45
Capacity
COP
%
kW
100%
6.3
4.3
75%
4.7
4.4
50%
3.1
4.1
25%
1.5
2.8
W15W45
Capacity
COP
%
kW
100%
7.1
4.8
75%
5.3
5.2
50%
3.5
4.5
25%
1.7
3.1
W20W45
Capacity
COP
%
kW
100%
7.3
5.2
75%
5.4
5.4
50%
3.6
4.8
25%
1.8
3.4
W25W45
Capacity
COP
%
kW
100%
8.1
5.9
75%
6.0
6.9
50%
4.0
6.3
25%
2.0
4.2
W10W55
Capacity
COP
%
kW
100%
5.9
3.0
75%
4.4
3.1
50%
2.9
2.6
25%
1.4
1.6
W15W55
Capacity
COP
%
kW
100%
6.7
3.5
75%
5.0
3.5
50%
3.3
2.9
25%
1.6
1.8
W20W55
Capacity
COP
%
kW
100%
7.0
3.8
75%
5.2
3.7
50%
3.5
3.2
25%
1.7
2.2
W25W55
Capacity
COP
%
kW
100%
7.8
4.3
75%
5.8
5.1
50%
3.9
4.6
25%
1.9
2.9
COP contains the "pump input (Based on EN 14511)"
100%: MAX Capacity
Performance data
3
B-35
Cylinder
unit/
Hydrobox/GSHP/WTW
Summary of Contents for EHWT17D-MHEDW
Page 1: ...DATA BOOK Vol 5 5 R32 ...
Page 2: ......
Page 4: ......
Page 71: ...MEMO ...
Page 128: ......
Page 131: ......