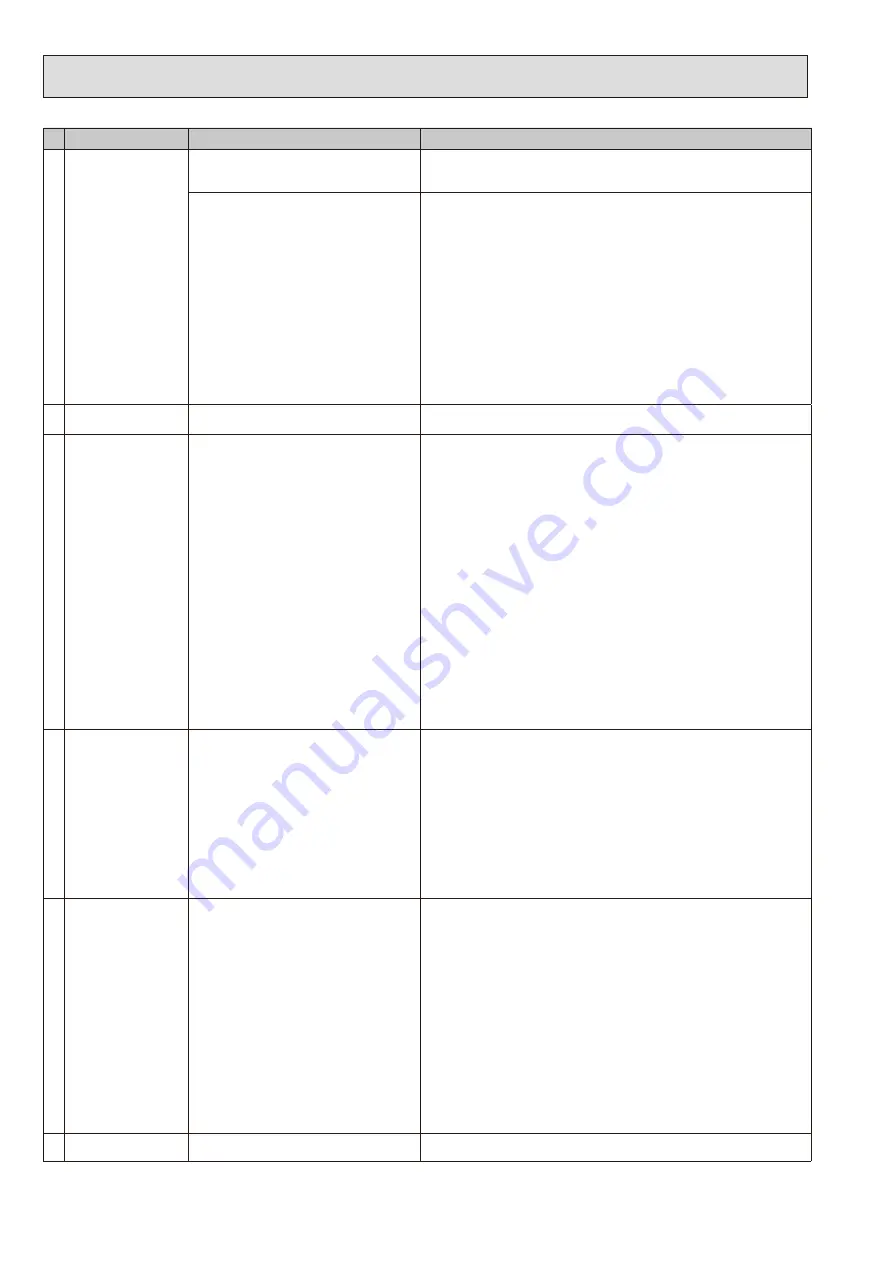
No.
Fault symptom
Possible cause
Explanation - Solution
5
LED on FTC3 is blink-
ing.
When LED1 on FTC3 is also blinking.
Check FTC3/outdoor unit connecting wire for connection failure.
Connection failure of FTC3/outdoor unit
connecting wire
When LED1 on FTC3 is lit.
1.
Miswiring of main controller wires
Multiple indoor units have been wired to 1
outdoor unit.
1.
Check the connection of main controller wires.
Only 1 indoor unit should be wired to 1 outdoor unit.
Supplementary indoor units should each be wired to a separate outdoor unit.
.
Miss-setting of refrigerant address for
outdoor unit
(Outdoor unit refrigerant address should be
set to "0")
.
Recheck the refrigerant address setting on the outdoor unit.
Set the refrigerant address to “0”.
(Set refrigerant address using SW1(3~6) on outdoor controller
circuit board.)
3.
Short-circuit of main controller wires
3, 4.
4. Defective main controller
Remove main controller wires and check LED2 on FTC3.
• If LED2 is blinking check the main controller wires are not short circuiting.
• If LED2 is lit, connect main controller wires again and:
- if LED2 is blinking, main controller is defective;
- if LED is lit, connection failure of main controller terminal block etc. has
returned to normal.
6
No water at hot tap.
1. Cold main off
1.
Check and open stop cock.
.
Strainer (field supply) blocked.
.
Isolate water supply and clean strainer.
7
Cold water at tap.
1.
All hot water used.
1.
Ensure DHW mode is operating and wait for tank to re-heat.
. Prohibit, schedule timer or holiday mode
selected.
.
Check settings and change as appropriate.
3.
Heat pump not working.
3.
Check heat pump – consult outdoor unit service manual.
4.
Booster heater cut out has triggered.
4.
Check booster heater thermostat and press reset button if safe.
Reset button is covered with white rubber cap see component parts diagram
section 10-6. for position.
5.
Booster heater breaker (ECB1) has tripped.
5.
Check the cause of the trip and reset if safe.
6. The booster heater thermal cut-out has
operated and can not be reset using the
manual reset button.
6.
Check the resistance of the thermal cut out, if open then the connection is
broken and the booster heater will have to be replaced.
Please contact your Mitsubishi Electric dealer.
7.
Immersion heater cut out has triggered.
7.
Check immersion heater thermostat and press reset button,
located on immersion heater boss, if safe. If the heater has been operated
with no water inside it may have failed, so please replace it with a new one.
8.
Immersion heater breaker (ECB2) has tripped.
8.
Check the cause of the trip and reset if safe.
9.
3-way valve fault
9.
Check plumbing/wiring to 3-way valve.
(i) Operate 3-way valve manually using the main remote controller. (Refer to
<Manual operation> in 9.2).
(ii) Replace 3-way valve coil.
(iii) Replace 3-way valve. (Refer to Procedure 6 in “11. DISASSEMBLY
PROCEDURE.”
8
It takes long for water
to heat.
1.
Heat pump not working.
1.
Check heat pump – consult outdoor unit service manual.
.
Booster heater cut out has triggered.
.
Check booster heater thermostat and press reset button if safe.
Reset button is covered with white rubber cap see component parts diagram
section 10-6. for position.
3.
Booster heater breaker (ECB1) has tripped.
3.
Check the cause of the trip and reset if safe.
4. The booster heater thermal cut-out has
operated and can not be reset using the
manual reset button.
4.
Check the resistance of the thermal cut out, if open then the connection is
broken and the booster heater will have to be replaced.
Please contact your Mitsubishi Electric dealer.
5.
Immersion heater cut out has triggered.
5.
Check immersion heater thermostat and press reset button,
located on immersion heater boss, if safe. If the heater has been operated
with no water inside it may have failed, so please replace it with a new one.
6.
Immersion heater breaker (ECB2) has tripped.
6.
Check the cause of the trip and reset if safe.
9
Water in tank is not
used, but the water
temperature of the tank
decreases.
The water temperature decreases to a certain
degree as the tank heat radiates when DHW
or Heating operation is not running. If the
temperature decreases excessively and
reheating occurs frequently, check for the
following.
1.
Water leakage through the pipes that
connect to the tank
1.
Take the following measures.
• Retighten the nuts holding the pipes onto the tank.
• Replace seal materials.
• Replace the pipes.
.
Peeling off of insulation
.
Reattach insulation.
3.
3-way valve fault
3.
Check plumbing/wiring to 3-way valve.
(i) Operate 3-way valve manually using the main remote controller. (Refer to
<Manual operation> in 9.2).
(ii) Replace 3-way valve coil.
(iii) Replace 3-way valve. (Refer to Procedure 6 in “11. DISASSEMBLY
PROCEDURE.”
10
Hot or warm water from
cold tap.
If tap runs cold after a minute or so the pipe is
picking up heat from heating pipe work.
Insulate/re-route pipe work.
50
Summary of Contents for EHPT20X-VM2HA
Page 11: ... See Chapter 6 10 11 6 WIRING DIAGRAM 6 1 EHST20C VM6HA ...
Page 12: ... See Chapter 6 10 12 6 2 EHST20C YM9HA ...
Page 13: ... See Chapter 6 10 13 6 3 EHST20C VM6A EHST20C VM6SA ...
Page 14: ... See Chapter 6 10 14 6 4 EHST20C YM9A ...
Page 15: ... See Chapter 6 10 15 6 5 EHPT20X VM2HA ...
Page 16: ... See Chapter 6 10 16 6 6 EHPT20X VM6HA ...
Page 17: ... See Chapter 6 10 17 6 7 EHPT20X YM9HA ...
Page 18: ... See Chapter 6 10 18 6 8 EHPT20X VM6A ...
Page 19: ... See Chapter 6 10 19 6 9 EHPT20X YM9A ...
Page 25: ...25 WATER SYSTEM DIAGRAM 8 EHST20C M HA M A EHST20C VM6SA ...
Page 26: ...26 EHPT20X VM2HA EHPT20X M HA M A ...
Page 75: ...75 ...