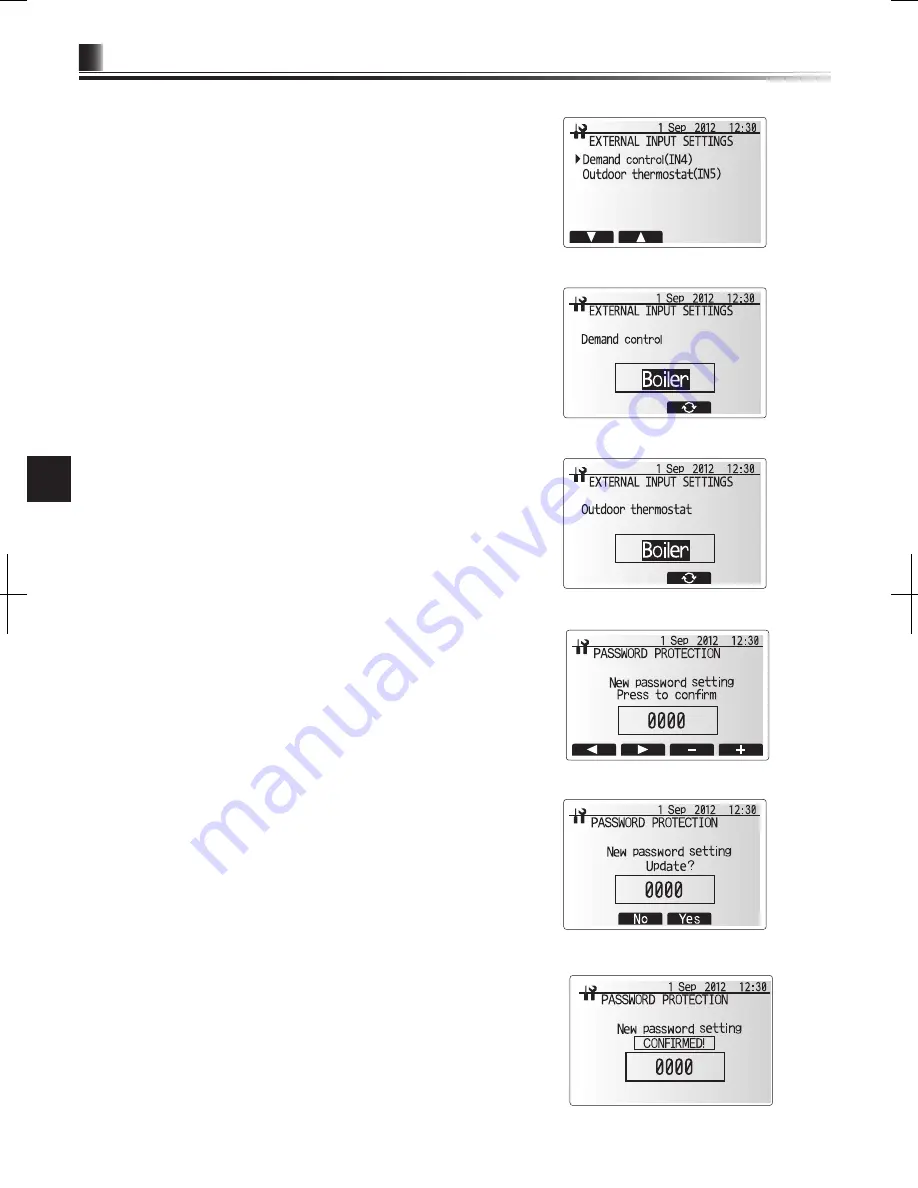
5
System Set Up
5
GB
External input settings menu screen
Demand control screen
Outdoor thermostat setting screen
External input settings
From the service menu use F and F2 buttons to highlight External input settings
then press CONFIRM.
<Demand control (IN4)>
From the External input settings menu highlight Demand control (IN4).
Press CONFIRM.
The Demand control screen is displayed.
.
2.
3.
Press F3 button to select Heat source OFF or Boiler.
Press CONFIRM.
Note: The selection of “OFF”, whilst a signal is being sent to IN4, forcefully
stops all the heat source operations and the selection of “Boiler” stops
operations of heat pump and electric heater and performs boiler op-
eration.
4.
5.
<Outdoor thermostat (IN5)>
From the External input settings menu highlight Outdoor thermostat (IN5).
Press CONFIRM.
The Outdoor thermostat screen is displayed.
Press F3 button to select Heater or Boiler.
Press CONFIRM.
Note: The selection of “Heater”, whilst a signal is being sent to IN5, performs
electric-heater-only operation and the selection of “Boiler” performs
boiler operation.
.
2.
3.
4.
5.
Password protection
Password protection is available to prevent unauthorised access to the service
menu by untrained persons.
From the service menu use F and F2 buttons to scroll through list until
Pass-
word protection
is highlighted.
Press CONFIRM.
When password input screen is displayed use buttons F and F2 to move left
and right between the four digits, F3 to lower the selected digit by , and F4 to
increase the selected digit by .
When you have input your password press CONFIRM.
.
2.
3.
4.
The password verify screen is displayed.
To verify your new password press button F3.
Your password is now set and the completion screen is displayed.
5.
6.
7.
<Resetting the password>
If you forget the password you entered, or have to service a unit somebody else
installed, you can reset the password to the factory default of
0000
.
From the main settings menu scroll down the functions until Service Menu is
highlighted.
Press CONFIRM.
You will be prompted to enter a password.
Hold down buttons F3 and F4 together for 3 secs
You will be asked if you wish to continue and reset the password to default set-
ting.
To reset press button F3.
The password is now reset to
0000
.
.
2.
3.
4.
5.
6.
7.
Password input screen
Password verify screen
Completion screen