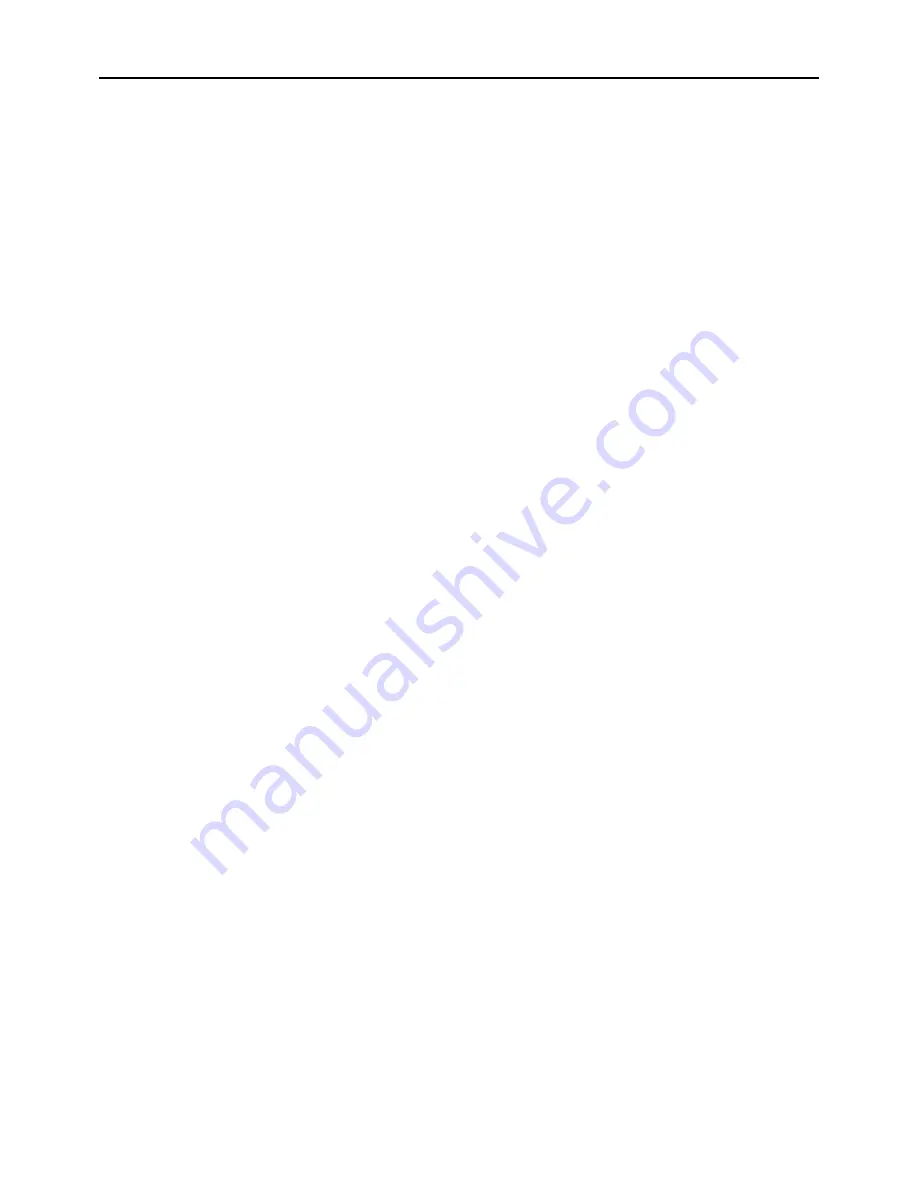
[
I
Read Before Servicing ]
- 11 -
HWE09070
GB
7. Notes
To evacuate air from the entire system
Applying a vacuum through the check joints at the refrigerant service valve on the high and low pressure sides (BV1
and 2) is not enough to attain the desired vacuum pressure.
Be sure to apply a vacuum through the check joints at the refrigerant service valve on the high and low pressure
sides (BV1 and 2) and also through the check joints on the high and low pressure sides (CJ1 and 2).
To evacuate air only from the outdoor units
Apply a vacuum through the check joints on the high and low pressure sides (CJ1, and 2).
To evacuate air from the indoor units and extension pipes
Apply a vacuum through the check joints at the refrigerant service valve on the high and low pressure sides (BV1
and 2).
Summary of Contents for CMB-PW202V-J
Page 1: ...Service Handbook AIR CONDITIONERS MODEL CMB PW202V J ...
Page 9: ...HWE09070 GB ...
Page 11: ... 2 ...
Page 25: ... 16 ...
Page 28: ... II Restrictions 19 HWE09070 GB ...
Page 31: ... 22 II Restrictions GB HWE09070 ...
Page 37: ... 28 ...
Page 40: ... III WCB Components 31 HWE09070 GB 3 WCB Circuit Board SW1 SW2 SW5 SW6 SW4 ...
Page 41: ... 32 III WCB Components GB HWE09070 ...
Page 42: ... 33 HWE09070 GB IV Electrical Wiring Diagram 1 Electrical Wiring Diagram of the WCB 35 ...
Page 43: ... 34 ...
Page 45: ... 36 IV Electrical Wiring Diagram GB HWE09070 ...
Page 47: ... 38 ...
Page 51: ... 42 ...
Page 61: ... 52 VI Control GB HWE09070 ...
Page 63: ... 54 ...
Page 73: ... 64 ...
Page 109: ... 100 ...