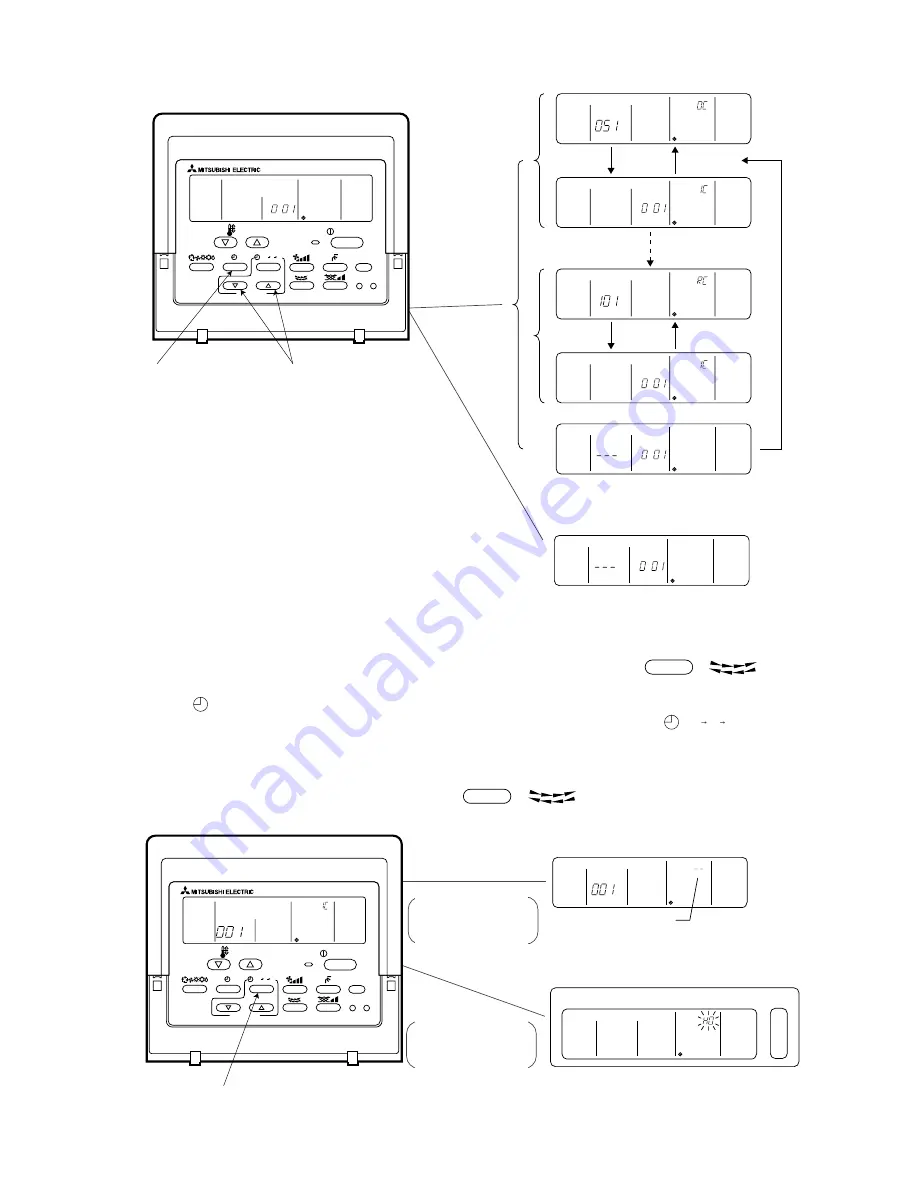
3)
Method of deletion
•Deletion of group registration information of indoor unit ......................................
¢
[Operation procedure]
1
With the remote controller under stopping or at the display of “HO”, continuously press the
FILTER
+
switch (
A
+
B
) at the same time for 2 seconds to change to the registration mode.
.
2
Press the
switch (
E
) to display the indoor unit address registered. (As same as
™
)
3
In order to delete the registered indoor unit being displayed on the remote controller, press the
CLOCK
ON OFF
(
F
) switch
two times continuously. At completion of the deletion, the attribute display section will be shown as “– – ”.
(See figure below.)
Note: Completing the deletion of all indoor units registered on the remote controller returns to “HO” display.
4
After completing the registration, continuously press the
FILTER
+
switch (
A
+
B
) at the same time for 2
seconds to change to the original ordinary mode (with the remote controller under stopping).
ERROR CODE
OA UNIT ADDRESS NO
˚C
INDOOR UNIT
ADDRESS NO
ERROR CODE
OA UNIT ADDRESS NO
˚C
INDOOR UNIT
ADDRESS NO
ERROR CODE
OA UNIT ADDRESS NO
˚C
1
Set the address
2
Press the switch for
confirmation (
E
)
• Registered
• No registration
❇
Same display will appear when
the unit of “007” is not existing.
1
Press the switch for confir mation (
F
)
twice continuously .
• Deletion completed
• Deletion completed
In case group re-
gistration with other
indoor unit is existing
In case no group
registration with other
indoor unit is existing
1
1
1
+
2
“– –” indicates the
deletion completed.
˚C
˚C
(Alternative
display)
˚C
˚C
(Alternative
display)
INDOOR UNIT
ADDRESS NO
ERROR CODE
OA UNIT ADDRESS NO
˚C
2
ON/OFF
TEMP
FILTER
CHECK TEST
ON OFF
CLOCK
PAR-F27MEA
TIMER SET
ON/OFF
TEMP
FILTER
CHECK TEST
ON OFF
CLOCK
PAR-F27MEA
TIMER SET
- 52 -
Summary of Contents for CITY MULTI CMB-P1016V-F
Page 18: ... 17 RELAY 10 board RELAY 4 board ...
Page 72: ... 71 ...