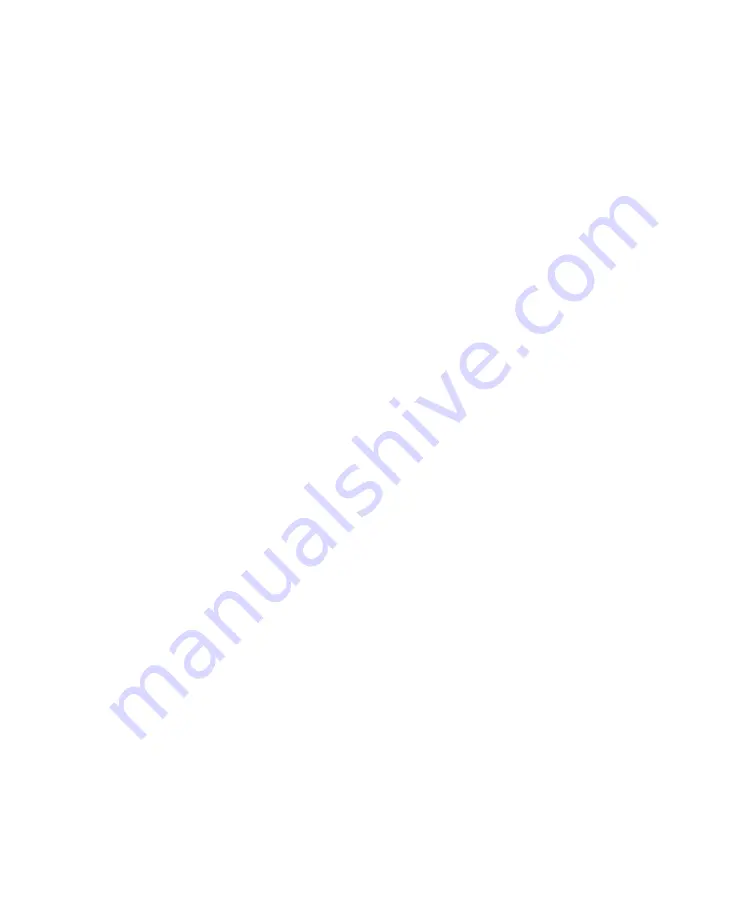
17
Chapter 6: Test the Installation
It is imperative that alarm points are tested and that alarm notifications are received
so they can be acknowledged by the customer or end-user once the unit is put into
production. This includes phone numbers, text messages, email addresses, fax
numbers, and pager numbers.
Additionally, it is recommended that the customer or end-user test all alarm points every
six months to ensure all electrical components and alarm parameters are still functioning
as desired and that alarms are being received and acknowledged by recipients. Refer to
the Spring Cleaning/Fall Fix-up document for testing procedures.
Complete the following tests prior to leaving the job site:
1. Confirm AC power. Use a voltmeter across the AC terminal to verify ~12–14 VAC is
present.
2. Test the battery. Remove the AC fuse and confirm the RTU stays online. Replace the
AC fuse.
3. Test the radio connection. Check the radio status on the LCD screen. It should read
“connected.” If not, call Technical Support at (877) 993-1911 option 2.
4. Inspect the status on the LCD. Analog, digitals, etc.
5. Test the digital alarm inputs. Put each digital input into an alarm state. From
the touch screen press digital and confirm inputs respond as expected. Mission
Technical Support is available to confirm that data is being properly transmitted and
received on your web portal. A smartphone can be used otherwise.
6. Test the pump runtime inputs. Turn on pump 1. Mission D1 should respond on the
touch screen. If not, check the wiring and/or end-of-line resistors. Repeat step for
pump 2 and 3, if used.
7. Test the high level alarm. Open the wet well. Pull the high-level float up and put it into
alarm condition by tipping it. Ensure that the digital input four respond. If not, check
the wiring and the high level float itself.