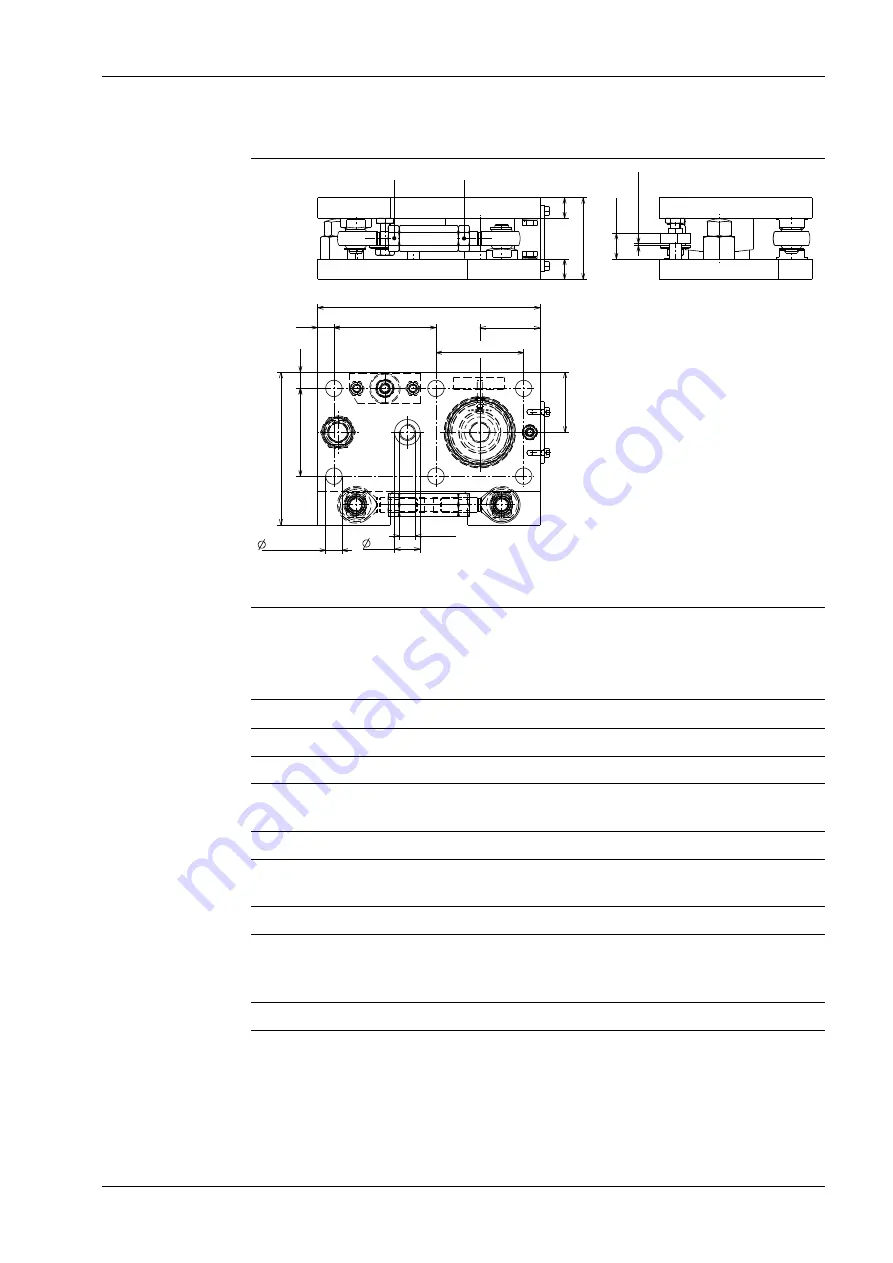
PR 6012/42
8
0
2
0
2
0
2
1.5..
..
5
2
5
(
)
15
0
21 8
1
6
1 6
5
9
5 9
1 6 (12x )
8 6
10 0
8
6
M1 6
2 5
**
*
* Right-handed thread, ** Left-handed thread
all dimensions in mm
4.3
Technical data
Maxi FLEX mounting kits PR 6012/02N and PR 6012/02S
PR 6012/02N
PR 6012/02S
Maximum capacity of load cell
500 kg…10 t
500 kg…10 t
Permissible lifting force
max. 10 kN
max. 10 kN
Permissible vertical load without
load cell
max. 5 t
max. 5 t
Permissible jack-up load
max. 5 t
max. 5 t
Permissible horizontal displace-
ment
max. ±4 mm
max. ±4 mm
Permissible temperature range
-40 °C…+100 °C
-40 °C…+100 °C
Material
Steel S235 with galv. zinc
coating, passivated and
sealed, RoHS-compliant
Stainless steel 1.4301 ac-
cording to DIN EN
10088-3 (AISI 304)
Weight net/gross
6.38 kg/6.77 kg
6.38 kg/6.77 kg
4 Specifications
Maxi FLEX and Maxi FLEXLOCK mounting kits PR 6012/02, ../32, ../42
Minebea Intec
EN-17