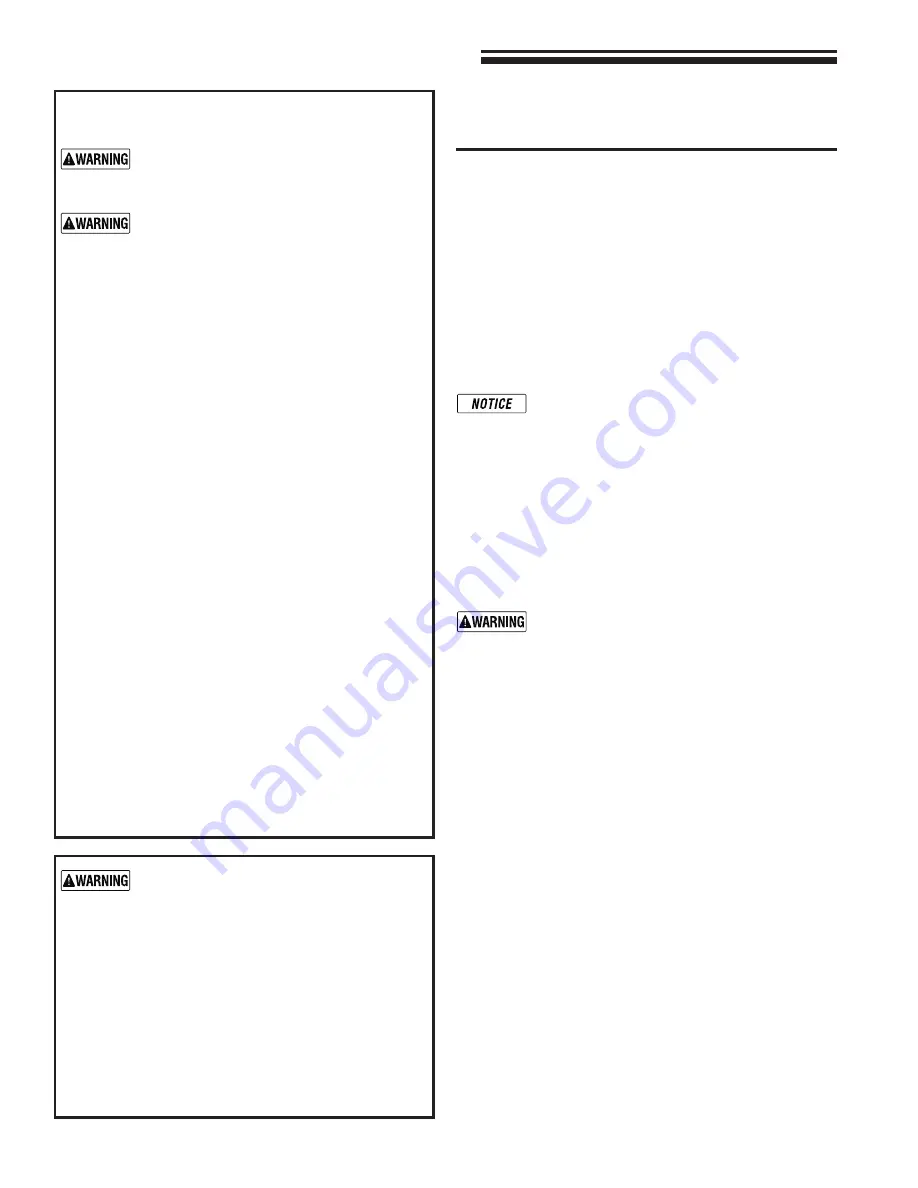
GSA
Gas-Fired Steam Boilers –
Boiler Manual
2
Part Number 550-110-738/1012
This manual must only be used by a
qualified
heating installer/service technician. Read
these instructions completely before beginning the
installation. Failure to follow these instructions can
cause severe personal injury, death or substantial
property damage.
Improper installation, adjustment, alteration, service or
maintenance can cause property damage, personal injury,
exposure to hazardous materials, or loss of life. Refer to the
User’s Information Manual provided with this boiler. Installation
and service must be performed by a qualified installer, service
agency or the gas supplier who must read and follow the
supplied instructions before installing, servicing or removing this
boiler. This boiler contains materials that have been identified
as carcinogenic, or possibly carcinogenic, to humans.
Failure to adhere to the guidelines below
can result in severe personal injury, death or
substantial property damage.
The boiler contains ceramic fiber and fiberglass
materials. Use care when handling these
materials per instructions on page 25 of this
manual. Failure to comply could result in severe
personal injury.
When servicing boiler —
1. To avoid electric shock, disconnect electrical supply before
performing maintenance.
2. To avoid severe burns, allow boiler to cool before performing
maintenance.
Boiler operation —
3. Do not block flow of combustion or ventilation air to boiler.
4. Should overheating occur, turn off or disconnect electrical
supply to boiler and shut off the gas supply at a location
external to the appliance, if possible.
5. Do not use this boiler if any part has been under water.
Immediately call a qualified service technician to inspect the
boiler and to replace any part of the control system and any
gas control that has been under water.
Boiler water —
6. DO NOT use petroleum-based cleaning or sealing
compounds in boiler system. Water seal deterioration will
occur, causing leakage between boiler sections, circulator
flanges, diaphragm tanks or other system components. This
can result in substantial property damage.
7. DO NOT use “ homemade cures ” or “ boiler patent
medicines”. Serious damage to boiler, personnel and/or
property may result.
8. Continual fresh makeup water will reduce boiler life. Mineral
buildup in sections reduces heat transfer, overheats cast
iron, and causes section failure. Addition of oxygen and
other gases can cause internal corrosion. Leaks in boiler or
piping must be repaired at once to prevent makeup water.
9. Do not add cold water to hot boiler. Thermal shock can cause
sections to crack.
1 Prepare boiler location
Codes & Checklist
Installations must follow these codes:
• Local, state, provincial, and national codes, laws, regulations
and ordinances.
• National Fuel Gas Code, ANSI Z223.1–latest edition.
• Standard for Controls and Safety Devices for Automatically
Fired Boilers, ANSI/ASME CSD‑1, when required.
• National Electrical Code.
• For Canada only: B149.1 or B149.2 Installation Code, CSA
C22.1 Canadian Electrical Code Part 1 and any local codes.
Certification
The GSA boiler gas manifold and controls met safe
Lighting and other performance criteria when boiler
underwent tests specified in ANSI Z21.13–latest
edition.
Before locating the boiler:
o
Check for nearby connection to:
• Venting connections
• Gas supply piping
• Electrical power
o
Check area around boiler. Remove any combustible materials,
gasoline and other flammable liquids.
Failure to keep boiler area clear and free of com-
bustible materials, gasoline and other flammable
liquids and vapors can result in severe personal
injury, death or substantial property damage.
o
Boiler must be installed so that gas control system components
are protected from dripping or spraying water or rain during
operation or service.
o
If new boiler will replace existing boiler, check for and correct
system problems, such as:
• System leaks causing oxygen corrosion or section cracks
from hard water deposits.
Read this first!