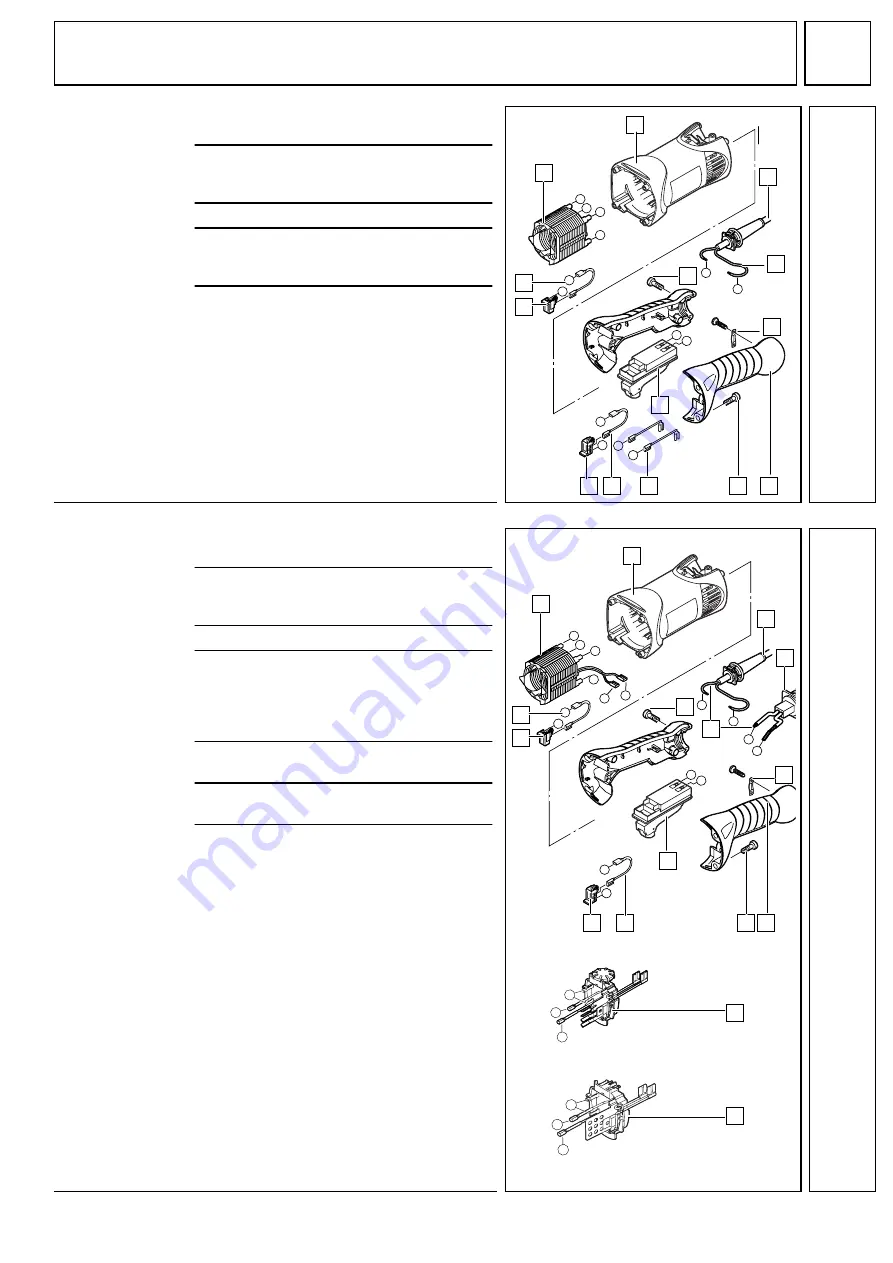
5
PAGE
4939 5228 01
Machines
without
electronics:
Removing
the field
1
Remove seven screws (5) and (A) from
the handle (B) and detach the handle.
2
Branch off the field wires (e, d, f, g) and re-
move the brush holders (4) and the con-
necting cables (3) and (8) from both sides.
3
Unscrew the strain relief (7).
4
Remove the switch (9) and branch off the
mains feed lines (6) (a, b).
Remove the mains connection cable (C).
5
Remove the field (1) from the motor hous-
ing (2).
☞
If necessary, hit the motor housing (2)
lightly with a plastic hammer for sup-
port.
Machines with
electronics:
Removing
the field
Removing
the electronic
component
1
Remove seven screws (5) and (A) from
the handle (B) and detach the handle.
2
Branch off the field wires (e, d, f, g, k) and
remove the connecting cables (3) and the
brush holders (4) from both sides.
3
Unscrew the strain relief (7).
4
Branch off the switch (8) and remove it.
Branch off the mains feed lines (6) (a, b).
Remove the mains connection cable (9).
Machines with QUIK-LOK:
Remove the
insert (E).
5
Machines with speed electronics:
Remove the electronic element (C).
6
Machines with constant electronics:
Remove the electronic element (D).
7
Remove the field (1) from the motor hous-
ing (2).
☞
If necessary, hit the motor housing (2)
lightly with a plastic hammer for sup-
port.
e
d
a
b
i
a
b
h
f
g
g
f
d
e
1
2
3
8
3
4
6
5
A
7
9
4
B
C
12
k
f
d
d
f
k
b
a
e
d
a
b
i
a
b
h
f
g
e
g
k
k
b
a
1
2
3
3
4
6
5
A
7
8
4
B
C
D
E
9
12