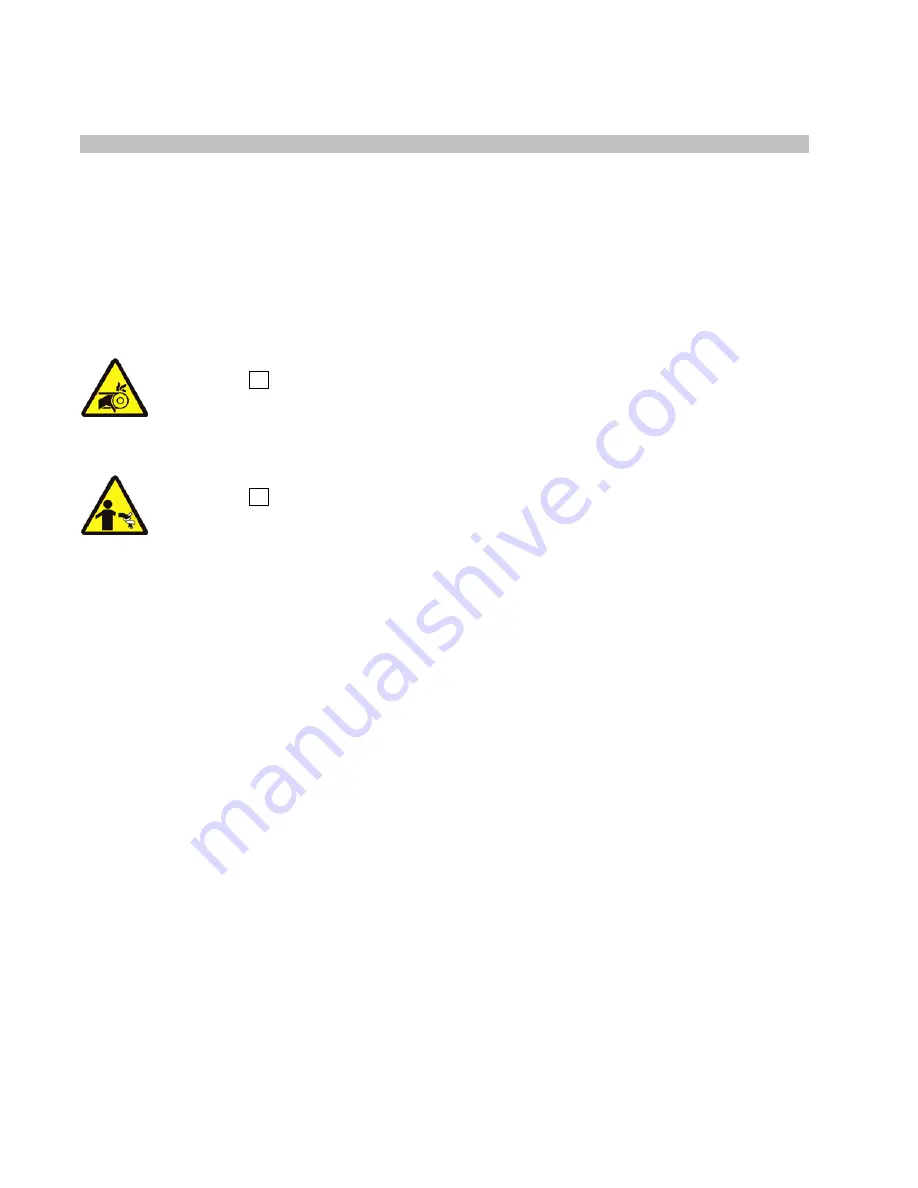
PELLERIN MILNOR CORPORATION
BIRH3M02 (Published) Book specs- Dates: 20080731 / 20080731 / 20080731 Lang: ENG01 Applic: RH3
Servicing the Door to Open it with Power Off or with a
Malfunctioning Door Lock
Note 1:
This document supersedes document MSSM0288AE and applies to all washer-extractors with
four-spoke door handles, including 30022Hxx, MCRxxxxx models. The photographs in this document
show the older style bare metal door handles but the instructions apply, as well, to newer machines with
black, coated handles.
The door is designed to lock as soon as the machine starts a wash cycle. If electrical power to the
machine is interrupted during the washing cycle, or if the door interlock mechanism fails to
unlock, the door can be opened by
qualified, service personnel
by removing the door handle and
a few related components. These components must be properly reinstalled for safe operation.
WARNING 1 : Entangle and crush hazards
—Contact with moving components normally
isolated by doors, guards, covers and panels can entangle and crush body parts. These
components move automatically.
• Service the machine only if qualified and authorized.
• Lockout/tagout power at the wall disconnect before proceeding.
WARNING 2 : Amputation hazard
—If the door interlock mechanism does not function
properly, an operator may be able to open the door and reach into the machine during operation.
Goods in the rotating cylinder can wrap around a person's arm and twist it off.
• Verify proper door lock function during machine operation, before returning the machine
to normal service.
1.
Disassembly
1.1.
Removing the Handle and Opening the Door
—The handle is held in place on the
shaft with a thrust washer and retaining clip in front of the handle and a flange bearing and
retaining clip behind the handle. The amount of turning force the handle can exert on the shaft is
adjustable with the four set screws, springs and steel balls—one within each spoke of the handle.
The steel balls seat into depressions in the shaft. When properly adjusted, the set screws will
apply sufficient spring tension so that the handle will reliably operate the latch, but the handle
will ratchet if turned counterclockwise or if too much turning force is applied.
Remove the handle from the shaft as follows:
1. Gently pry the black plastic cap from the center of the handle with a small screwdriver.
2. Attempt to ratchet the handle by turning it counterclockwise by hand. If this is not possible,
the springs have too much tension applied. Back off on the four set screws just enough for the
handle to ratchet. Typically this happens when the set screws are flush with the surface of the
handle spoke as is the case in
Figure 1
.
3. Repeat the following sub-steps four times to remove all set screws, springs, and steel balls:
a.
Remove the set screw from the topmost handle spoke.
b. Hold a finger over the hole, then, while keeping your finger on the hole, ratchet the
handle counterclockwise until the hole is pointing down.
c.
Hold one hand or a cup under the handle to catch the contents, then remove your finger,
allowing the spring and ball to fall out, as in
Figure 2
. Shake the handle if necessary, to
work the components free.
Summary of Contents for 30022H8J
Page 2: ......
Page 4: ......
Page 6: ......
Page 25: ...Section 1 Service and Maintenance ...
Page 52: ......
Page 53: ...Section 2 Drive Assemblies ...
Page 61: ...Section 3 Shell Door and Assemblies ...
Page 69: ...Section 4 Water and Steam Piping and Assemblies ...
Page 79: ...Section 5 Chemical Supply Devices ...
Page 82: ......