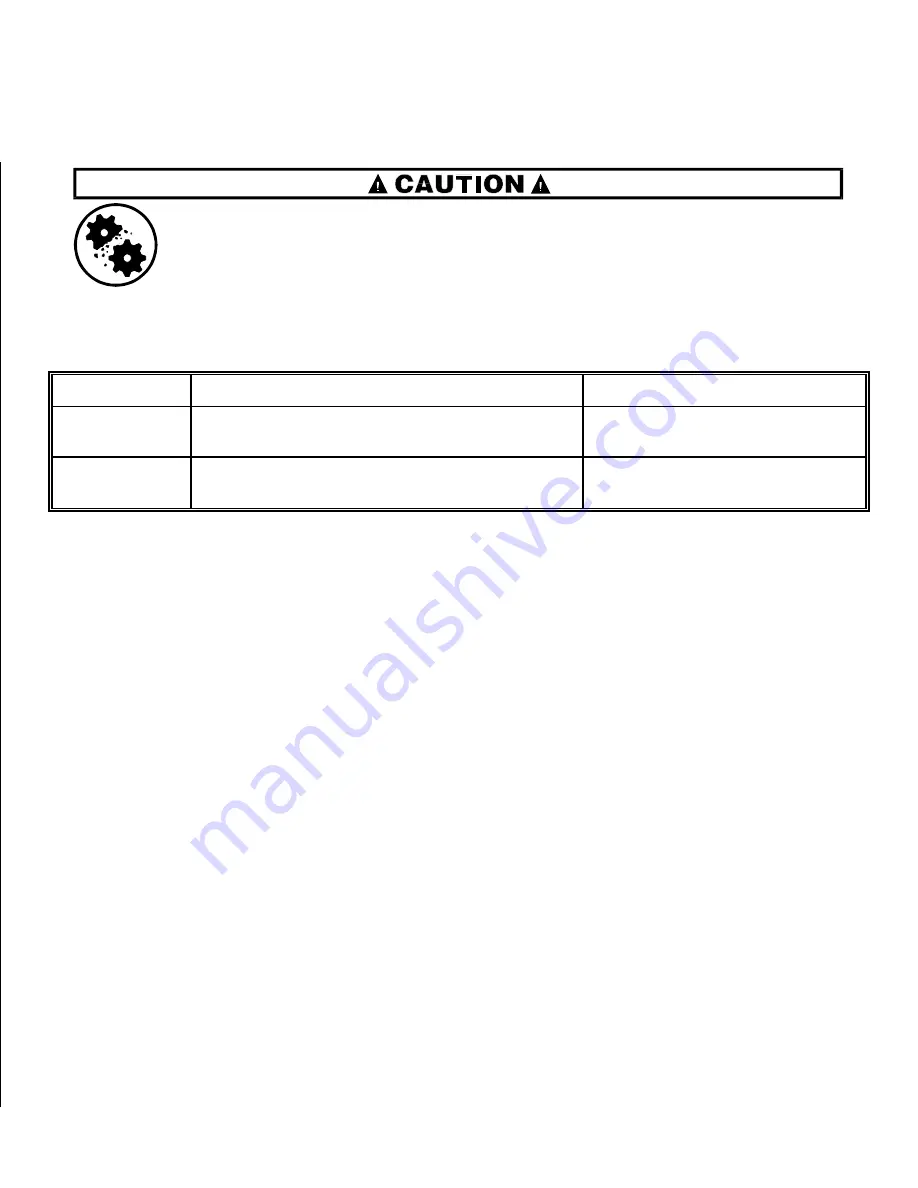
MSSM0712AE/2001084V (1 of 4)
È
30022H7J AND 30022H8J PREVENTIVE MAINTENANCE
As required by the warranty, to ensure safe operation, and to achieve optimum performance and service life
from Milnor
®
washer-extractors, the schedules, instructions, and precautions herein must be strictly followed.
Ï
Preventive Maintenance Schedule
Component
Procedure
See FIGURE
Frequency
Door interlock
Test functioning for safe operation.
BMP990012
daily
Water seal grease point
Slowly grease, 2 strokes (0.125 fluid
ounces - 3.54 grams) at one location.
FIGURE 1
monthly
Water inlet strainers
Clean as required
FIGURE 4
every four months
Foundation bolts
Check bolt tightness and wear.
Adjust or replace if necessary.
Dimensional
drawing
every four months
Drive train
Check belt tension and wear. Check
pulleys and other drive components
for wear. Replace if necessary.
FIGURE 5
every four months
Main bearing housing
Change lubricant.
FIGURES 2 and 3 every four months
Ê
Main Bearing Housing Preventive Maintenance
ELECTROCUTION HAZARD—High voltage is present inside electric boxes,
motors, and many other components. Power switches on machine disable only
control circuit power in certain boxes. You can be killed or seriously injured on
contact with high voltage.
☞
Lock OFF and tag out power at the wall disconnect before servicing.
ENTANGLE AND CRUSH HAZARD—Belts and pulleys can entangle and crush
body parts.
☞
Lock OFF and tag out power at the wall disconnect before servicing, except
where specifically instructed otherwise in this section.
☞
Permit only qualified maintenance personnel to perform these procedures.
MALFUNCTION HAZARD—Oil spilled on components may cause machine malfunction.
☞
Refill bearing housing carefully.
MACHINE DAMAGE HAZARD—Mixing incompatible lubricants will result in
severe machine damage.
☞
DO NOT mix different base lubricants.
☞
Before using a non-specified lubricant, consult the lubricant manufacturer
to determine compatibility.
Ï
Lubrication Specifications
Component
Lubricant/Type
Amount of Lubricant
Main bearing
housing
High quality SAE 50 (ISO 220)
heavy duty motor oil, non-detergent if available
22 fluid ounces (651 milliliters)
Water seal
grease
Shell Alvania EP (or equivalent)
Preventive Maintenance Schedule
Ê
Bearing Lubrication Procedures
See the appropriate main bearing drawing (if provided) during this procedure (see Table of Contents).
1. Remove the rear belt cover.
2. Remove the drain plug (FIGURE 3) on the bottom of the main bearing housing and allow the bearing housing
to drain completely. Inspect the leak-off, drained oil, and magnetic drain plug for water and/or metal parti-
cles. Water and/or metal particles can indicate worn or damaged seals and bearings. Install the drain plug.
3. Locate the oil fill plug (FIGURE 2) on the bearing housing. Clean the surrounding area and remove the
oil fill plug.
4. Refill the bearing housing. After refilling the bearing housing, reinstall the oil fill plug and clean any excess
lubricant from the machine.
Ê
Water Seal Lubrication
Ë
Grease Gun Precautions
1. Do not use a pneumatic grease gun. Pump grease slowly, taking 10-12 seconds to complete each stroke.
A grease gun can build up extremely high pressure which will force water seals out of position and cause
them to leak, even though the seal is equipped with spring loaded relief plug.
2. Apply quantity of grease called for in the schedule. Over-lubrication can be as damaging as under-lubrica-
tion. Where quantities are stated in strokes, one stroke of the grease gun is assumed to provide .0624 fluid
Summary of Contents for 30022H8J
Page 2: ......
Page 4: ......
Page 6: ......
Page 25: ...Section 1 Service and Maintenance ...
Page 52: ......
Page 53: ...Section 2 Drive Assemblies ...
Page 61: ...Section 3 Shell Door and Assemblies ...
Page 69: ...Section 4 Water and Steam Piping and Assemblies ...
Page 79: ...Section 5 Chemical Supply Devices ...
Page 82: ......