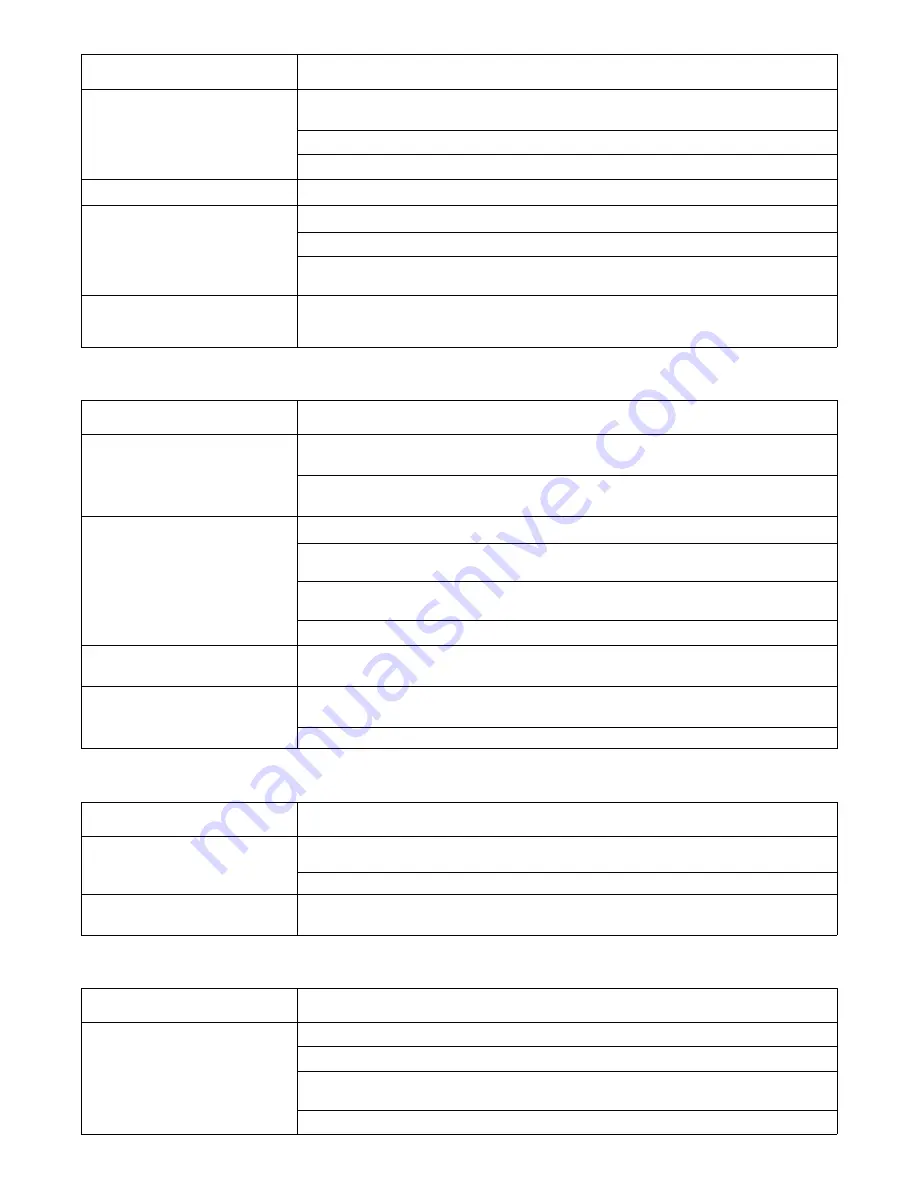
Complete Parts List available at www.MillerWelds.com
OM-262 752 Page 54
Trouble
Remedy
Constant speed wire feeder does not
work.
Reset supplementary protector CB9 (see Section 8-8).
Check and secure connections to Remote 14 receptacle (see Section 5-15).
Repair or replace wire feeder.
Low CV weld output.
Increase Voltage/Amperage Adjust Control setting.
Min or max CV weld output only.
Check position of Voltage/Amperage Adjust control and Process/Contactor switch.
Repair or replace remote control device.
Have Factory Authorized Service Agent check Amperage/Voltage Adjust Control and field current
regulator board.
With VRD switch S5 On, machine does
not return to low open−circuit voltage at
the end of weld.
Have Factory Authorized Service Agent check and replace Main Control boards PC1 and PC21.
B. Standard Generator Power
Trouble
Remedy
No generator power output at AC recept-
acles; weld output okay.
Reset receptacle supplementary protectors. Reset GFCI receptacle.
Check fuse F1, and replace if open (see Section 8-8). Have Factory Authorized Service Agent check inte-
grated rectifiers SR1 and SR2, resistor R3, and capacitor C6.
No generator power or weld output.
Disconnect equipment from generator power receptacles during start-up.
Check fuses F1 and F2, and replace if open (see Section 8-8). Have Factory Authorized Service Agent
check integrated rectifiers SR1 and SR2, capacitor C6, and the rotor.
Reset supplementary protector CB4. Have Factory Authorized Service Agent check integrated rectifier
SR1 .
Have Factory Authorized Service Agent check brushes and slip rings, and field excitation circuit.
High output at generator power AC re-
ceptacles.
Have Factory Authorized Service Agent adjust generator power field current resistor R3.
Low output at generator power AC re-
ceptacles.
Check fuse F1, and replace if open (see Section 8-8). Have Factory Authorized Service Agent check inte-
grated rectifier SR2, resistor R3, and capacitor C6.
Have Factory Authorized Service Agent check brushes and slip rings.
C. Three-Phase Generator Power
Trouble
Remedy
No or low output at three-phase gener-
ator/receptacle RC5.
Reset supplementary protector CB1 (see Section 7-1).
Have Factory Authorized Service Agent check brushes and slip rings.
Erratic output at three-phase generator/
receptacle RC5.
Have Factory Authorized Service Agent check brushes and slip rings.
D. Engine
Trouble
Remedy
Engine will not crank.
Supplementary protector CB2 open. Reset CB2.
Check battery connections and tighten if necessary. Check battery, and replace if necessary.
Circuit breaker CB10 may be open. CB10 automatically resets when fault is corrected (see Section 8-8).
Have Factory Authorized Service Agent check engine wiring harness and components.
Check engine wiring harness plug connections.