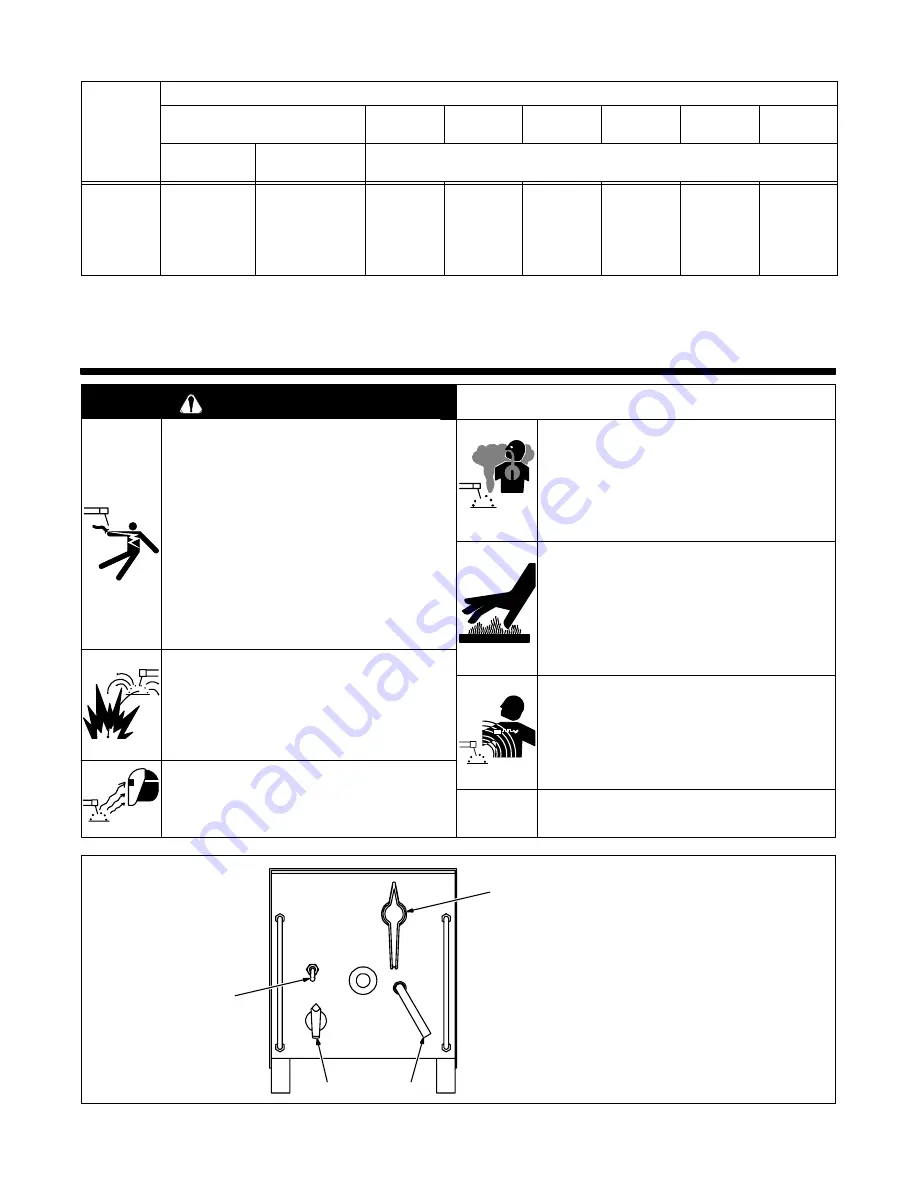
OM-805 Page 5
Table 3-1. Weld Cable Size*
Total Cable (Copper) Length In Weld Circuit Not Exceeding
100 ft (30 m) Or Less
150 ft
(45 m)
200 ft
(60 m)
250 ft
(70 m)
300 ft
(90 m)
350 ft
(105 m)
400 ft
(120 m)
Welding
Amperes
10 To 60%
Duty Cycle
60 Thru 100%
Duty Cycle
10 Thru 100% Duty Cycle
100
4
4
4
3
2
1
1/0
1/0
150
3
3
2
1
1/0
2/0
3/0
3/0
200
3
2
1
1/0
2/0
3/0
4/0
4/0
250
2
1
1/0
2/0
3/0
4/0
2-2/0
2-2/0
300
1
1/0
2/0
3/0
4/0
2-2/0
2-3/0
2-3/0
*Weld cable size (AWG) is based on either a 4 volts or less drop or a current density of at least 300 circular mils per ampere.
S-0007-D
SECTION 4 – OPERATION
WARNING
ELECTRIC SHOCK can kill; TWO TIMES
NORMAL OPEN-CIRCUIT VOLTS exists
between electrode holders of opposite
polarity.
•
Always wear dry insulating gloves.
•
Insulate yourself from work and ground.
•
Do not touch live electrical parts.
•
Keep all panels and covers securely in place.
•
Do not touch electrode holders of opposite polarity
at the same time.
•
Separate electrode holders of opposite polarity to
prevent contact.
•
See ANSI Z49.1 and OSHA TITLE 29, CHAPTER
XVII, PART 1910, Subpart Q.
WELDING can cause fire or explosion.
•
Do not weld near flammable material.
•
Watch for fire; keep extinguisher nearby.
•
Do not locate unit over combustible surfaces.
•
Do not weld on closed containers.
•
Allow work and equipment to cool before handling.
ARC RAYS can burn eyes and skin;
NOISE can damage hearing.
•
Wear welding helmet with correct shade of filter.
•
Wear correct eye, ear, and body protection.
FUMES AND GASES can be hazardous
to your health.
•
Keep your head out of the fumes.
•
Ventilate area, or use breathing device.
•
Read Material Safety Data Sheets (MSDSs) and
manufacturer’s instructions for material used.
HOT SURFACES AND EQUIPMENT can
cause burns.
•
Allow equipment to cool before inspecting or servic-
ing.
•
Wear correct hand and body protection.
•
Do not place anything on or near this unit during op-
eration.
MAGNETIC FIELDS FROM HIGH CUR-
RENTS can affect pacemaker operation.
•
Pacemaker wearers keep away.
•
Wearers should consult their doctor before going
near arc welding, gouging, or spot welding opera-
tions.
See Safety Precautions at beginning of manual for ba-
sic welding safety information.
swarn6.1* 10/91
ST-800 263
1
Coarse Amperage Control
2
Polarity Switch
This switch is included on PRC
units.
3
Fine Amperage Control
4
2-1/2 Ampere Switch
This switch is included on units with
Polarity switch. Switch is optional
for all other models.
1
2
3
4
Figure 4-1. Controls (PRC Model Shown)
Summary of Contents for MOG-200C
Page 6: ......
Page 17: ...OM 805 Page 11 NOTES...
Page 21: ...OM 805 Page 15 Notes...
Page 22: ...OM 805 Page 16 Notes...