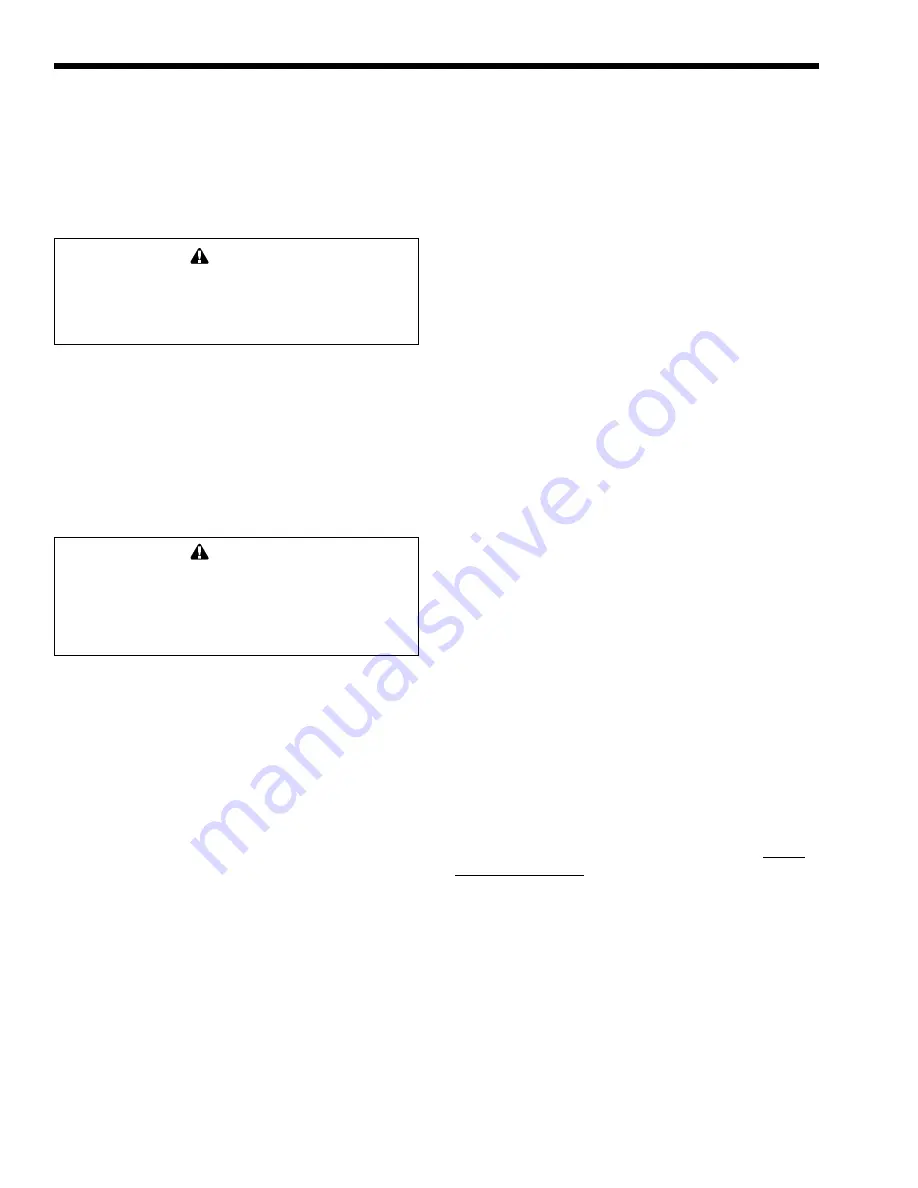
LAARS HEATING SYSTEMS
Page 8
NOTE: Do not use sheet metal screws at the
snap lock joints of Type B gas vents.
Do not weld or bolt the vent pipe to the boiler
drafthood or the vent damper if one is installed. The
weight of the stack must not rest on the boiler. The
drafthood and boiler top must be easily removable for
normal boiler service and inspection.
WARNING
Avoid ending boiler vents near air conditioning or air
supply fans. The fans can pick up exhaust flue
products from the boiler and return them inside the
building, creating a possible health hazard.
Avoid horizontal runs of the vent pipe, and 90
degree elbows, reductions and restrictions. Horizontal
runs should have at least a ¼ inch (6 mm) rise per foot
in the direction of flow. Support a vent connector for
the design and weight of the material used to maintain
clearances and prevent physical damage and
separation of joints.
Always use double-wall or insulated vent pipe
(Type B or equivalent).
WARNING
In cold weather, uninsulated outside vents can chill
the rising flue products, blocking the natural draft
action of the venting system. This can create a
health hazard by spilling flue products into the boiler
room.
Avoid oversize vent piping or extremely long
runs of the pipe which may cause too much cooling
and condensation of flue gasses.
2E-2. Replacement of Existing Boiler
At the time of the removal of an existing boiler,
the following steps shall be followed with each
appliance remaining connected to the common venting
system. During the testing of each unit, the other
appliances remaining connected to the common
venting system should not be operated.
1.
Seal any unused openings in the common
venting system.
2.
Visually inspect the venting system for proper
size and horizontal pitch. Determine that there is
no blockage or restriction, leakage, corrosion, or
other deficiencies which could cause an unsafe
condition.
3.
As far as possible, close all building doors and
windows. Also close all doors between the space
in which the appliances remaining connected to
the common venting system are located and the
other spaces of the building. Turn on any clothes
dryer and any appliance not connected to the
common venting system. Turn on any exhaust
fans, including range hoods and bathroom
exhausts, so they will operate at maximum
speed. Do not operate a summer exhaust fan.
Close all fireplace dampers.
4.
Place in operation the appliance being inspected.
Follow the lighting instructions for the unit.
Adjust the thermostat so the appliance will
operate continuously.
5.
After 5 minutes of main burner operation, test for
spillage at the draft hood relief opening. Use the
flame of a match or candle, or smoke from a
cigarette, cigar, or pipe.
6.
The tests should show that each appliance
connected to the common venting system vents
properly. Return all doors, windows, exhaust
fans, fireplace dampers and any other gas-burning
appliances to their previous condition of use.
7.
Any improper operation of the common venting
system should be corrected. The installation
should conform with the National Fuel Gas
Code, ANSI Z223.1. When resizing any portion
of the common venting system, the system
should be sized to approach the minimum
practical size. Refer to the tables in Appendix G
in the National Fuel Gas Code, ANSI Z223.1. (In
Canada, at the time the boiler is removed from
the common venting system, the common
venting system should be resized. The
installation should conform to CAN/CGA
B149.1 or .2.)
2F. Water Flow System
2F-1. Reversible Water Connections
NOTE: This procedure is not recommended for
the PH pump-mounted models.
Laars ships the HH boiler with the water
connections on the right side. The HH boiler can be
installed with the water connections on either side. It
could be necessary, or helpful, to switch the
connections to the left side to improve access for
installation service. Perform this modification before
installing the boiler using the following procedures:
1.
Remove the front door.
2.
If there is a vent cap or drafthood installed, it
must be removed before removing the grate top
assembly. On indoor installations (models 175-
250), the drafthood switch must be disconnected
at the vent damper receptacle on the left side of
the boiler.
3.
If the unit is in the low-profile outdoor
configuration, remove the hex-head screws (see
Figure 16) and lift the top assembly straight up.
4.
Remove the screws that fastens the flue collector
hold-down clamps and remove the clamps (see
Figure 17).