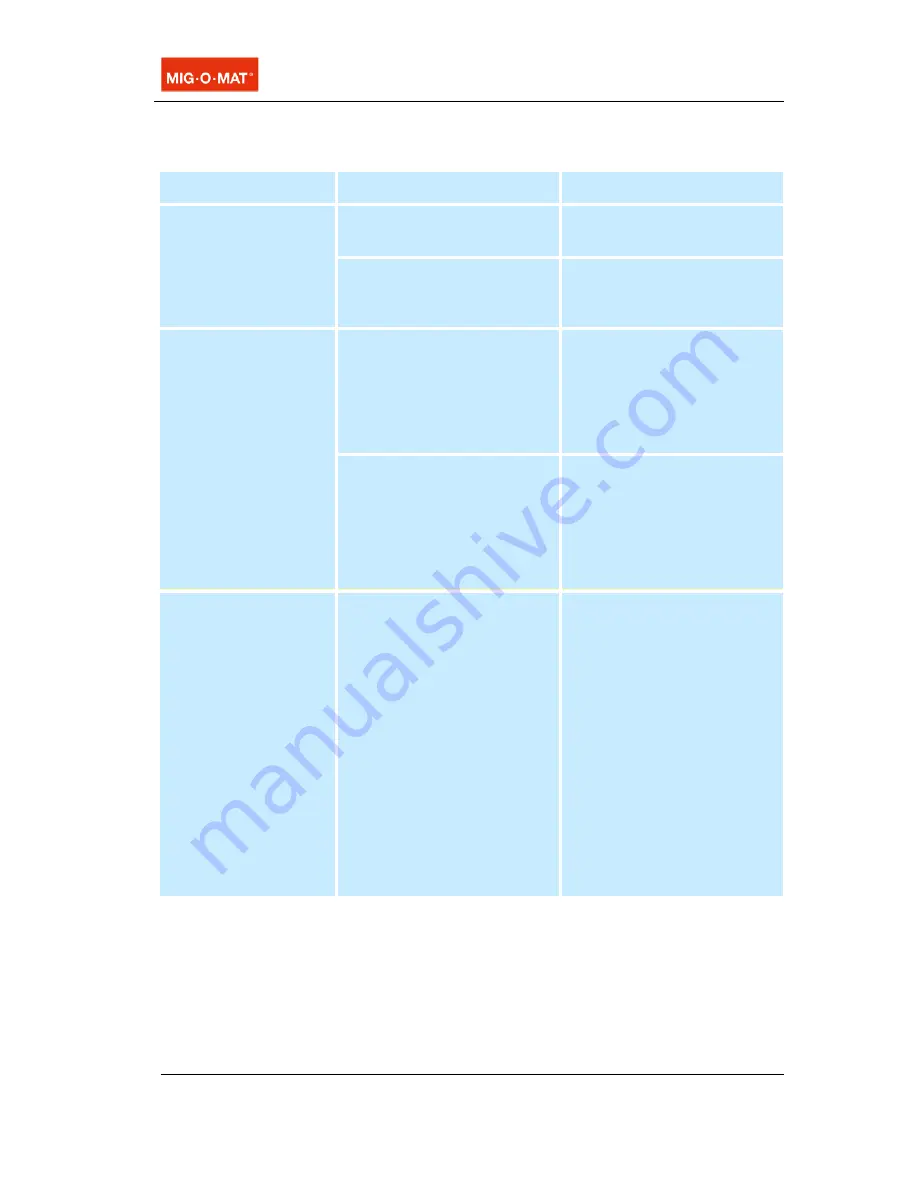
40
BA_Lötstar_EN_Vers.07.2016
© MIG·O·MAT GmbH
8.4
Trouble shooting
Malfunction / Fault
Possible cause
Remedy
The unit does not produce
any gas,
the display shows no
malfunction.
The unit is not connected to the
mains.
Plug the mains cable into a
suitable socket.
The unit has not been switched
on at the mains switch.
Switch on the unit at the mains
switch on the back – the display
shows the designation of the unit.
The unit does not produce
any gas.
The gas pressure is set at
approx. 150 mbar, the
valve at the burner hand
piece is closed.
The actual gas pressure
value does not correspond
with the set value!
The unit is leaky -(closing cap at
the reactor (
illustration 4.6.E.
)
and/or the gas route between gas
outlet (
illustration 5.2.B.
) and
hand piece are leaky).
Switch off the unit at the mains
switch, retighten the screw
connections, replace washers if
necessary, check the glasses for
leaks – check if the O rings are
mounted correctly.
The hose system inside the unit is
leaky.
Switch off the unit, pull the mains
plug, open the unit, check if the
hose connections sit tightly,
retighten loose connections
(if necessary contact the
Technical Support).
The unit does not produce
any gas although the
actual pressure
corresponds with the set
pressure value.
The gas route in one or more
components is choked:
•
burner nozzle and/or
•
filter cartridge (
illustration
8.1.3.B.
) and/or
•
sintered cone in vaporizer
glass
(illustration 8.1.3.F.
)
and/or
•
backfire protection (
illustration
4.6.B.
) and/or
•
handle of burner hand piece
Exchange the choked
components.