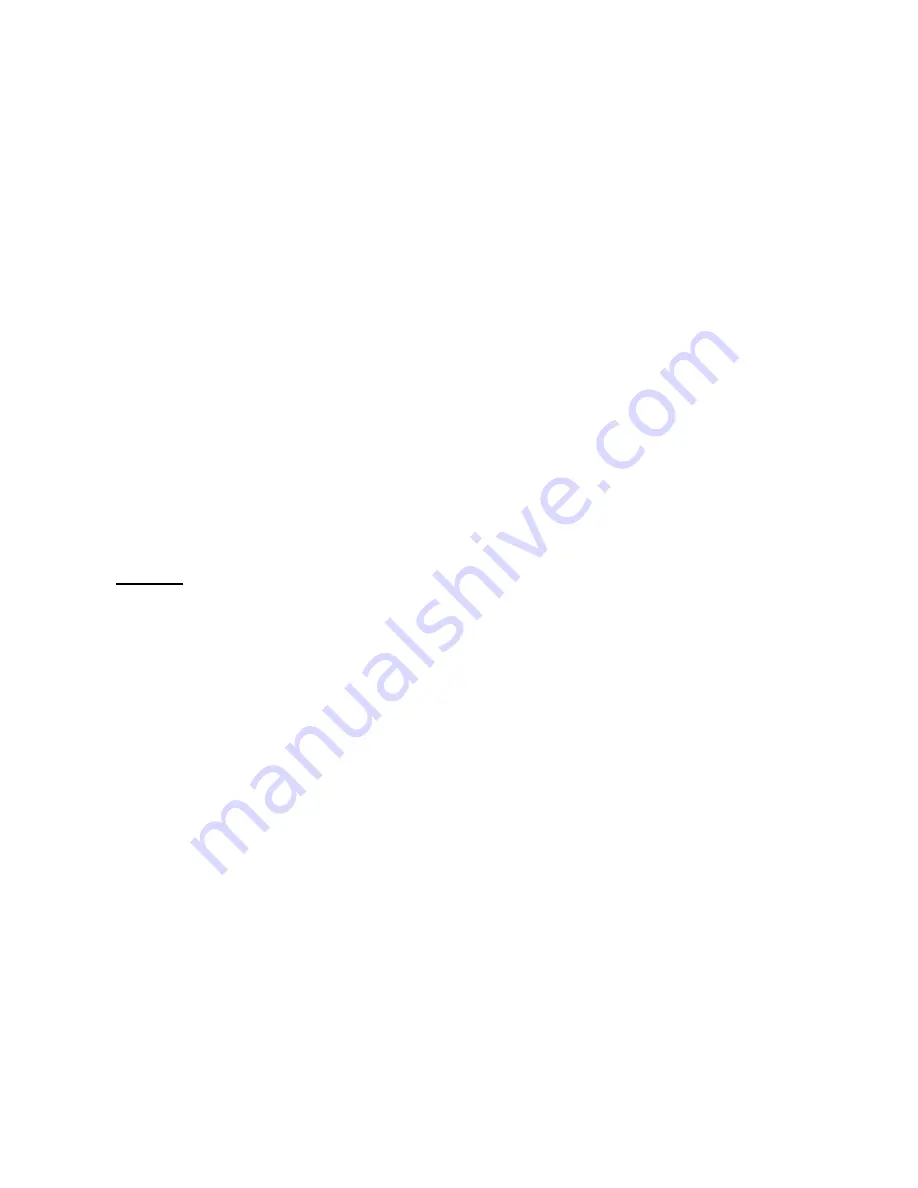
3
unit is so equipped.)
There is risk of physical injury, electric shock, or product failure.
When the product is soaked (flooded or submerged), contact an Authorized service center.
There is risk of fire or electric shock.
Be caution that water could not enter the product.
There is risk of fire, electric shock, or product damage.
Ventilate the product from time to time when operating it together with a stove, etc.
There is risk of fire or electric shock.
Turn the main power off when cleaning or maintaining the product.
There is risk of electric shock.
When the product is not be used for a long time, disconnect the power supply plug or turn off the
breaker.
There is risk of product damage or failure, or unintended operation.
Take care to ensure that nobody could step on or fall onto the outdoor unit.
This could result in personal injury and product damage.
Caution
Always check for gas (refrigerant) leakage after installation or repair of product.
Low refrigerant levels may cause failure of product.
Install the drain hose to ensure that water is drained away properly.
A bad connection may cause water leakage.
Keep level even when installing the product.
To avoid vibration of water leakage
Do not install the product where the noise or hot air from the outdoor unit could damage the
neighborhoods.
It may cause a problem for your neighbors.
Use two or more people to lift and transport the product.
Avoid personal injury.
Do not install the product where it will be exposed to sea wind (salt spray) directly.
It may cause corrosion on the product. Corrosion, particularly on the condenser and evaporator fins, could
cause product malfunction or inefficient operation.
Summary of Contents for PH Series
Page 1: ...MIDEA 50Hz PORTABLE PH SERIES ...
Page 11: ...9 4 Dimension Capacity Btu h W mm H mm D mm small body 329 318 615 big body 345 355 703 H W D ...
Page 13: ...11 6 Wiring Diagram MPPHA 05CRN7 QB6 MPPH 07CRN7 QB6G1 MPPH 08CRN7 QB6 MPPH 09CRN7 QB6 ...
Page 14: ...12 MPPHA 07CRN7 QB6 MPPHB 08CRN7 QB6 N MPPHB 09CRN7 QB6 N ...
Page 20: ...18 2 Use bolts to fasten the window sliders once they are adjusted to the Proper length ...