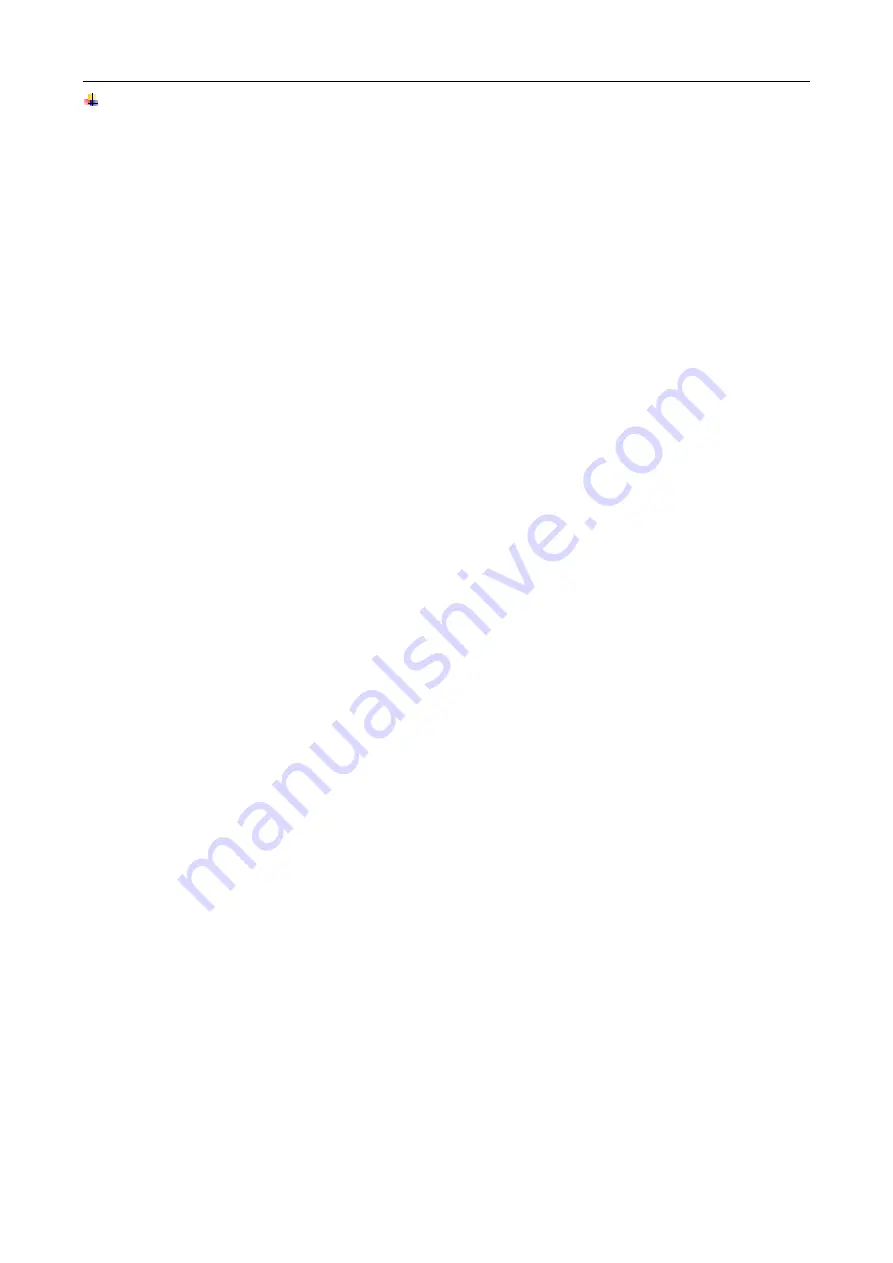
Flooded type water cooled screw chiller (PCB Control)
100
Refrigerant Circuit
Leak testing
Units are factory-charged with refrigerant R-22 (Refer to the Physical Data tables supplied in the IOM
manual book). Leak test must be done under sufficient pressure. This can be done by charging enough
refrigerant into the system to build the pressure up to approximately 70 kPa and adding sufficient dry
nitrogen to bring the pressure up to a maximum of 850 kPa. Leak test with an electronic leak detector.
Water flow through the vessels must be maintained anytime refrigerant is added or removed from the
system. If any leaks are found in welded or brazed joints, or it is necessary to replace a gasket, relieve
the test pressure in the system before proceeding. Brazing is required for copper joints. After leaks are
repaired, system must be evacuated and dehydrated.
Evacuation
After it has been determined that there are no refrigerant leaks, the system must be evacuated using a
vacuum pump with a capacity that will reduce the vacuum to at least 130Pa (=1mmHg). A mercury
manometer, or an electronic or other type of micron gauge, must be connected at the farthest point from
the vacuum pump. For readings below 130Pa, an electronic or other micron gauge must be used. The
triple evacuation method is recommended and is particularly helpful if the vacuum pump is unable to
obtain the desired 130Pa of vacuum. The system is first evacuated to approximately 660Pa (=5mmHg).
Dry nitrogen is then added to the system to bring the pressure up to zero.
Then the system is once again evacuated to approximately 230Pa(=2mmHg). This is repeated three
times. The first pull down will remove about 90% of the non-condensable, the second about 90% of that
remaining from the first pull down and, after the third, only 0.2% non-condensable will remain.
Checks on refrigerant charge
To verify if the unit is operating with the correct refrigerant charge, perform the following checks.
1. Run the unit at maximum operating load.
2. Check the leaving chilled water temperature to be between 6~8°C.
3. Check the entering cooling water temperature to be between 25 and 32°C.
4. Under the above mentioned conditions verify the following items.
a) The sub-cooling to be between 4 and 6°C
b) The difference between leaving water temperature and evaporating temperature to be in 4~6°C
range.
c) The difference between condensing temperature and condenser leaving water temperature to be in
0.2~3°C range.
e) The evaporator refrigerant level slightly laps last tubes row by checking the sight glass installed on
each evaporator for a visual inspection.
f) The condenser refrigerant level to be included between the condensing and the sub-cooling sections
by checking the sight glass installed on each condenser for a visual inspection.
5. Verify the sight glass on the liquid piping to be fully charged. If one of the above parameters exceeds
the limits, unit may require an additional refrigerant charge.
Note: Refrigerant removing and drain operation must be performed by qualified personnel using correct
material. Inappropriate maintenance could lead to refrigerant or pressure loss. Do not discharge the
refrigerant or the lubricant oil into the environment. Always use a proper recovery system.