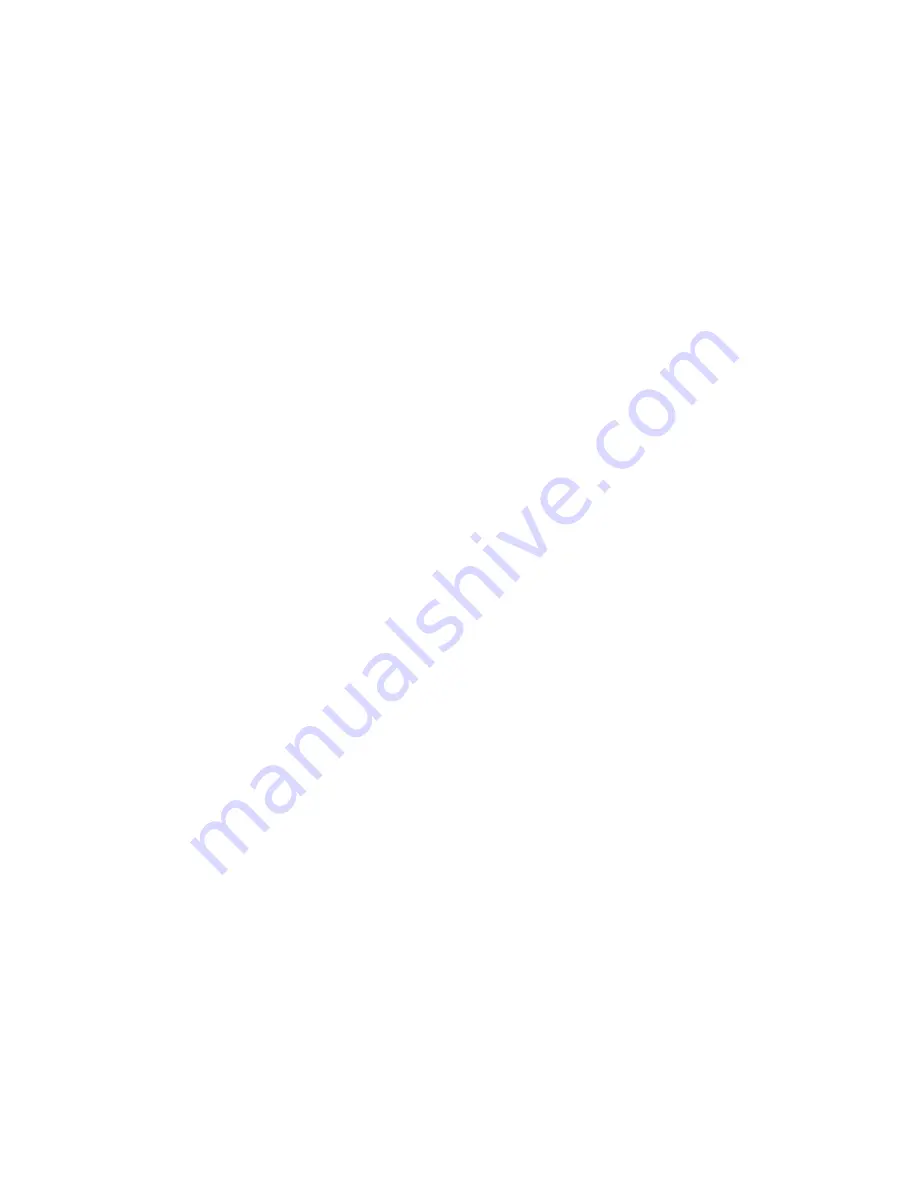
micro
Tec
9
2. Basic Safety Instructions
2.1 Heed the Notes and Instructions Given in this Operating
Manual!
A prime prerequisite for safe handling and malfunction-free operation of this instrument
is the awareness and recognition of basic safety instructions and regulations.
This operating manual contains the most important instructions for operating the
instrument in a safe manner.
This operating manual, especially the instructions on safety, are to be heeded by all
personnel who operate the instrument.
In addition, compliance with the regulations and specifications on accident prevention
applicable for the site of installation and use is to be maintained.
2.2 Obligation on the Part of the Operator
The operator is obliged to only allow personnel to operate the instrument, who
•
are familiar with basic regulations on safety at work and accident prevention,
and are trained in the use and operation of the instrument.
•
have read the chapter on safety and the warning notes and instructions given in
this operating manual.
•
have been taught to have due regard to aspect of safety during the execution of
their work.
2.3 Obligations on the Part of the Operating Staff
All personnel who are delegated with the task of operating this instrument are obliged
before starting work
•
to heed the basic regulations on safety at work and accident prevention.
•
to read and to comprehend the chapter on safety and the warning notes and
instructions given in this operating manual.
Summary of Contents for CUT4060E
Page 36: ...microTec 36 Notice...