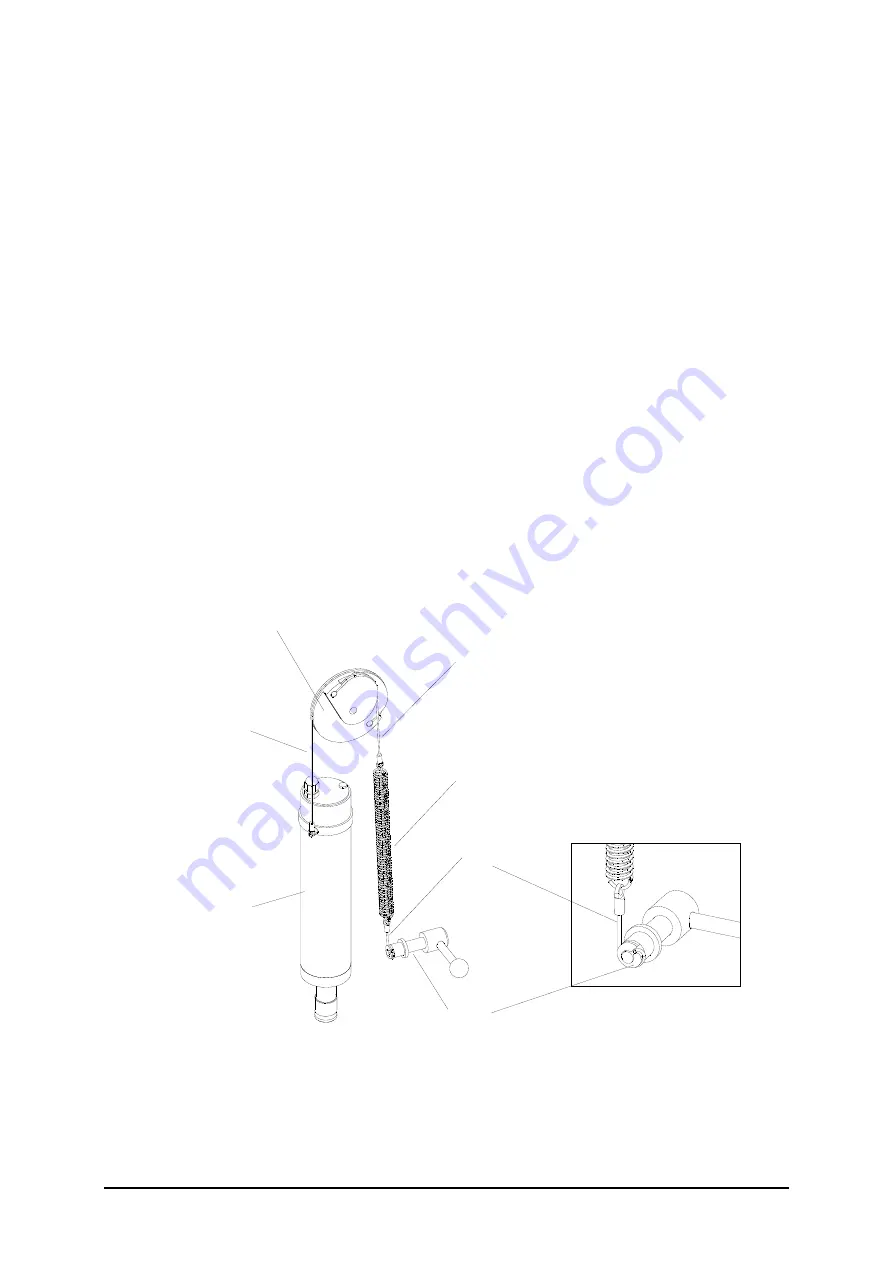
Operating Instructions Thread tapping units/ Accessoriesr 01/09, Software 4.9
©
01.1994-2016 microtap GmbH
59
• Cable 2 (retaining spring (C) -> eccentric pulley (B)
- Engage the looped end of the cable (2) with the retaining spring (2)
-
Insert the cable (2) end with the nipple and fix it in the excentre pulley (B)
• Cable 1 ( adjusting lever (D) -> retaining spring (C)
- Insert the cable (1) end with the nipple into the radial hole of the adjusting
lever (D).
- Engage the looped end of the cable (1) with the retaining spring (C)
• Cable 3 (eccentric pulley (B) and motor bracket (A)
- Insert the cable (3) end with the nipple and fix it in the excentre pulley (B)
- insert the new cable (3) end with the nipple into the hole located at the larger
diameter of the eccentric pulley (B) and secure it in place by tightening the
grub screw.
- Insert the cable end with the nipple and fix it in the eccentric pulley.
6. Remove the supporting wooden block and test the floating action of the work
head.
7. Close machine (see chapter “closing machine”)
3
B
2
1
D
A
C