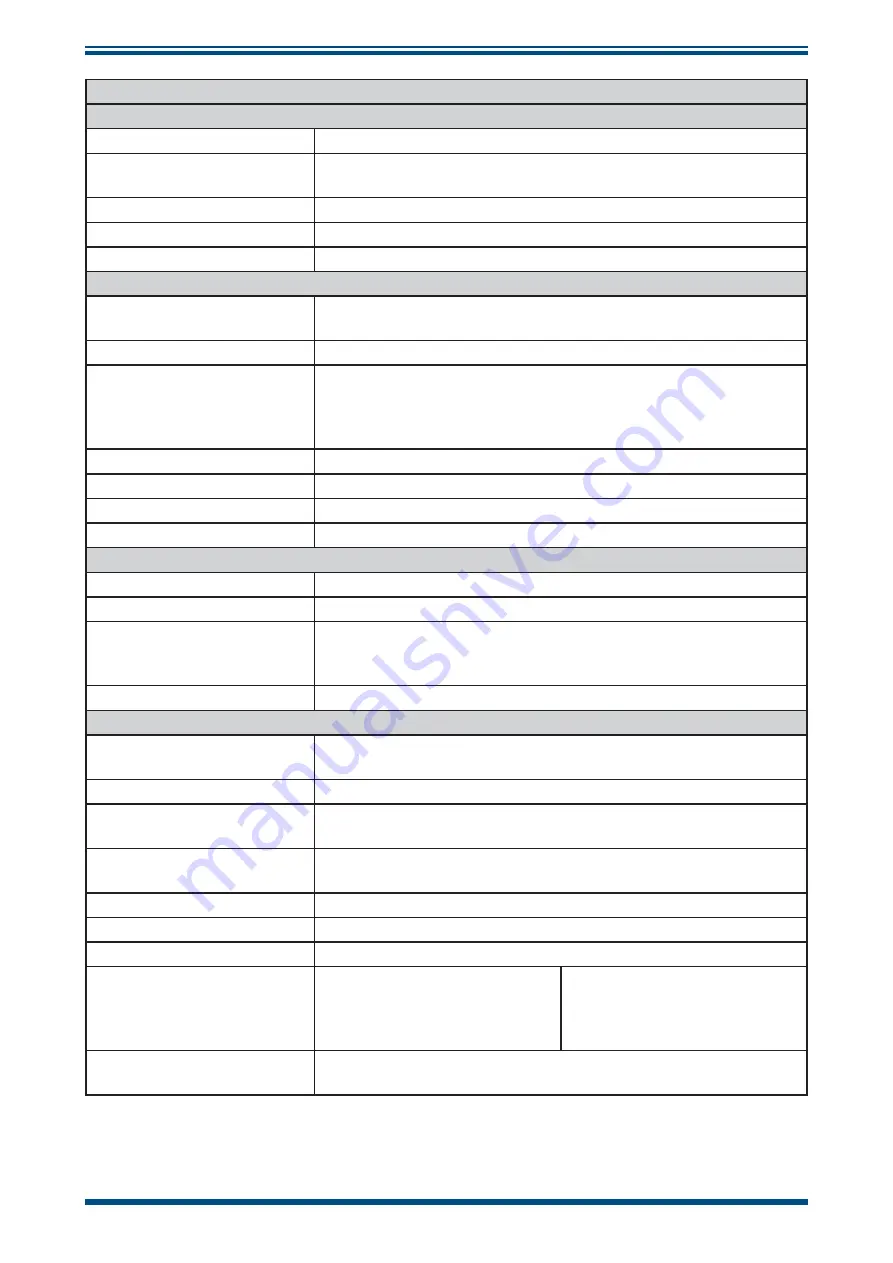
Cermet II User’s Manual
28
97049 Issue 25.3, October 2016
APPENDIX A
Transmitter
Performance Speci
fi
cations
Measurement Range
-100 to +20°Cdp (-148 to +68°Fdp) dew point
Accuracy
±1°C dew point (+20 to -60°C) (+68 to -76°F)
±2°C dew point (-60 to -110°C) (-76 to -166°F)
Response Time
5 mins to T95 (dry to wet)
Repeatability
0.5°Cdp (0.9°Fdp)
Calibration
13 point calibration with traceable 7 point calibration certi
fi
cate
Electrical Speci
fi
cations
Output Signal
4-wire connection, digital signal
User-con
fi
gurable over range
Output
Dew point
Output Scaled Range
Dew point: -100 to +20°C
Moisture content in gas: 0 to 9999 ppm
V
, 0 to 1000 lbs/MMSCF
and g/m
3
Non-standard available upon request
Supply Voltage
12 to 28 V DC
Load Resistance
Max 250
Ω
@ 12 V (500
Ω
@ 24 V)
Current Consumption
20 mA max
CE Conformity
2004/108/EC
Operating Speci
fi
cations
Operating Temperature
-40 to +60°C (-40 to +140°F)
Operating Pressure
45 MPa (450 barg ) max
Flow Rate
Mounted in standard sampling block: 1 to 5 Nl/min (2.1 to 10.6
scfh)
Direct insertion: 0 to 10 m/sec (0 to 32.8 fps)
Temperature Coef
fi
cient
Temperature compensated across operating temperature range
Mechanical Speci
fi
cations
Ingress Protection
IP66 in accordance with standard BS EN60529:1992
NEMA 4 in protection accordance with standard NEMA 250-2003
Housing Material
316 stainless steel
Filter (sensor protection)
Standard
: HDPE Guard < 10
μ
m
Optional
: 316 stainless steel sintered guard < 80
μ
m
Process Connection &
Material
5/8” - 18 UNF 316 stainless steel
Weight
150g (5.3oz)
Interchangeability
Fully interchangeable transmitter
Electrical Connection
Hirschmann GDS series (DIN 4350-C)
Diagnostic Conditions
(factory programmed)
Condition
Sensor fault
Under-range dew point
Over-range dew point
Output
23 mA
4 mA
20 mA
Digital Diagnostic
Communications
Communications RS485, 2-wire Modbus RTU