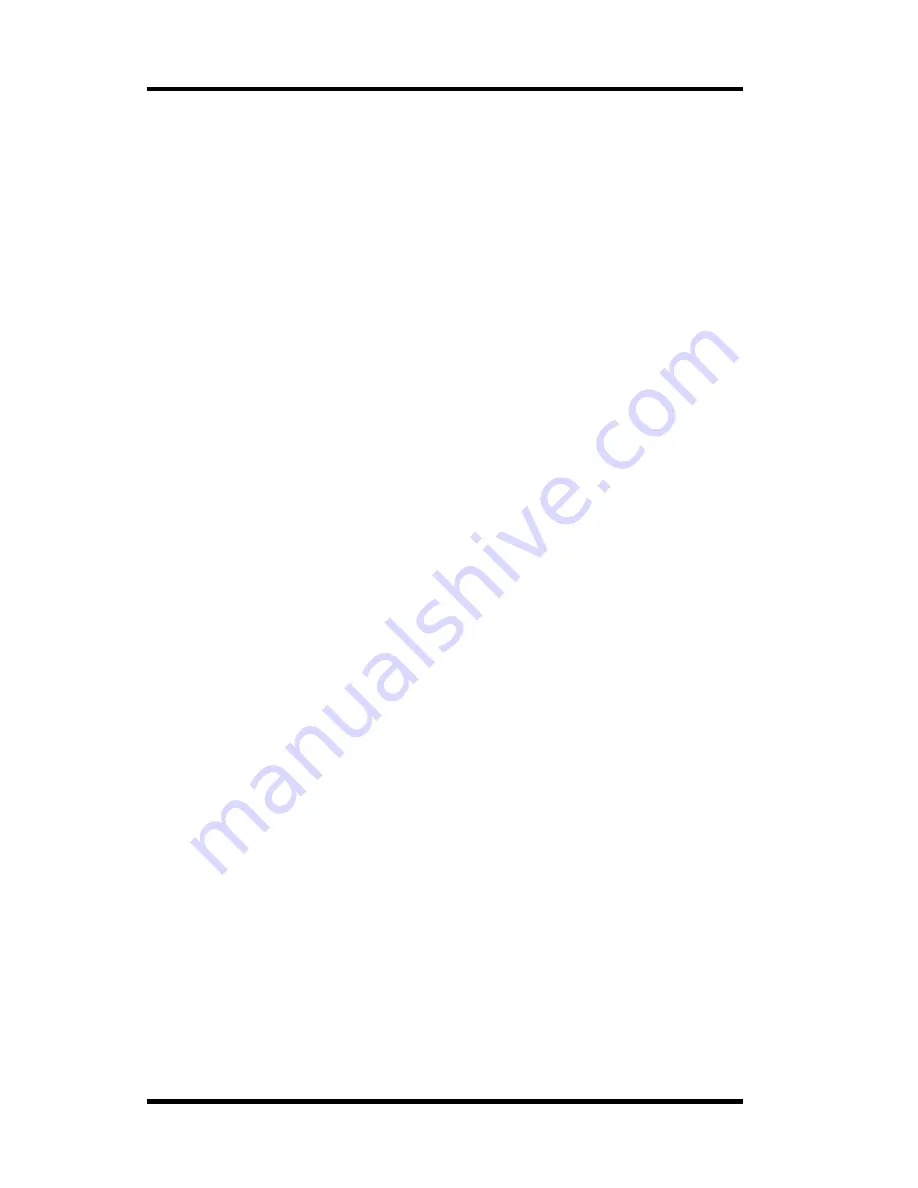
MGL Avionics Stratomaster Ultra “L” Owner’s manual
Page 58
elasticity of the materials used and therefore has a direct influence on the reading. The
quality of the vacuum has a direct bearing on errors and the maximum altitude the instrument
can indicate with a reasonable error.
The Stratomaster Ultra is based on a silicon pressure sensor. In principle, these sensors are
subject to many of the problems that affect ordinary mechanical instruments and many digital
altimeters have poor accuracy and resolution.
What is different in the Stratomaster Ultra?
The Stratomaster Ultra employs the most accurate absolute pressure sensor available. This
sensor is not cheap or simple. It starts with a tiny cavity in a silicon chip. This cavity is about
¼ mm
3
in size and contains a near perfect vacuum. It is sealed with a very thin membrane
that is only a few thousand atoms thick. The air pressure on the one side of this membrane
bends the membrane towards the vacuum cavity. This introduces tiny changes in the
electrical properties of the membrane. These changes are measured. Temperature effects
on the membrane are taken into account by measuring the temperature on the membrane
and compensating for known effects. During manufacture of this sensor, the membrane is
exposed to a focused electron beam that, atom by atom removes material from the
membrane until the sensor reads exactly the correct value. The Stratomaster Ultra then
converts this reading into digital form. But the results are not taken for granted. The
Stratomaster Ultra attempts to measure the signal to levels below those created by thermal
noise. This electrical noise is caused by the vibration of atoms. The Stratomaster Ultra knows
the characteristics of this unwanted signal and eliminates errors caused by this signal. In
addition, the Stratomaster Ultra measures the temperature surrounding the sensor and
compensates for any remaining temperature induced error. This compensation is different
from sensor to sensor as it depends on tiny, remaining manufacturing tolerances of the
sensors. But your instrument knows the behavior of its sensor and can correct for errors.
Once the pressure of the surrounding air has been accurately determined, how does one
calculate the altitude? Is atmospheric pressure not supposed to change with the local
weather as well?
Well, there you have it: All this accuracy and then a storm comes in and all is lost.
Back in the beginning of flight, (sometime after the Wright Brothers did the silly thing of
inventing powered flight), it was thought that it would be a good idea to have some indication
as to how high one was flying. Early, primitive altimeters where based on principles much like
we use today but were very crude and what was more disturbing, they depended on each
manufacturers interpretation as to how pressure changes with altitude.
We all know that pressure gets less as we increase our altitude. But by how much? The
American National Standards Institute and other standards bodies came up with the idea of
simply dictating how the atmosphere behaves. So ANSI created the “standard atmosphere”
which was valid on a “standard day”. The “standard day” was decreed to be a day at mean
sea level with a temperature of 15 degrees Celsius (59 degrees Fahrenheit). Further to this it
was decided that the temperature would decrease at a certain rate as we increased our
altitude. All of this and a portion of maths would now determine how our altimeter should
work. Of course, suitable “fudge factors” were used to make the maths agree with what could
be implemented using a bunch of mechanical gears.