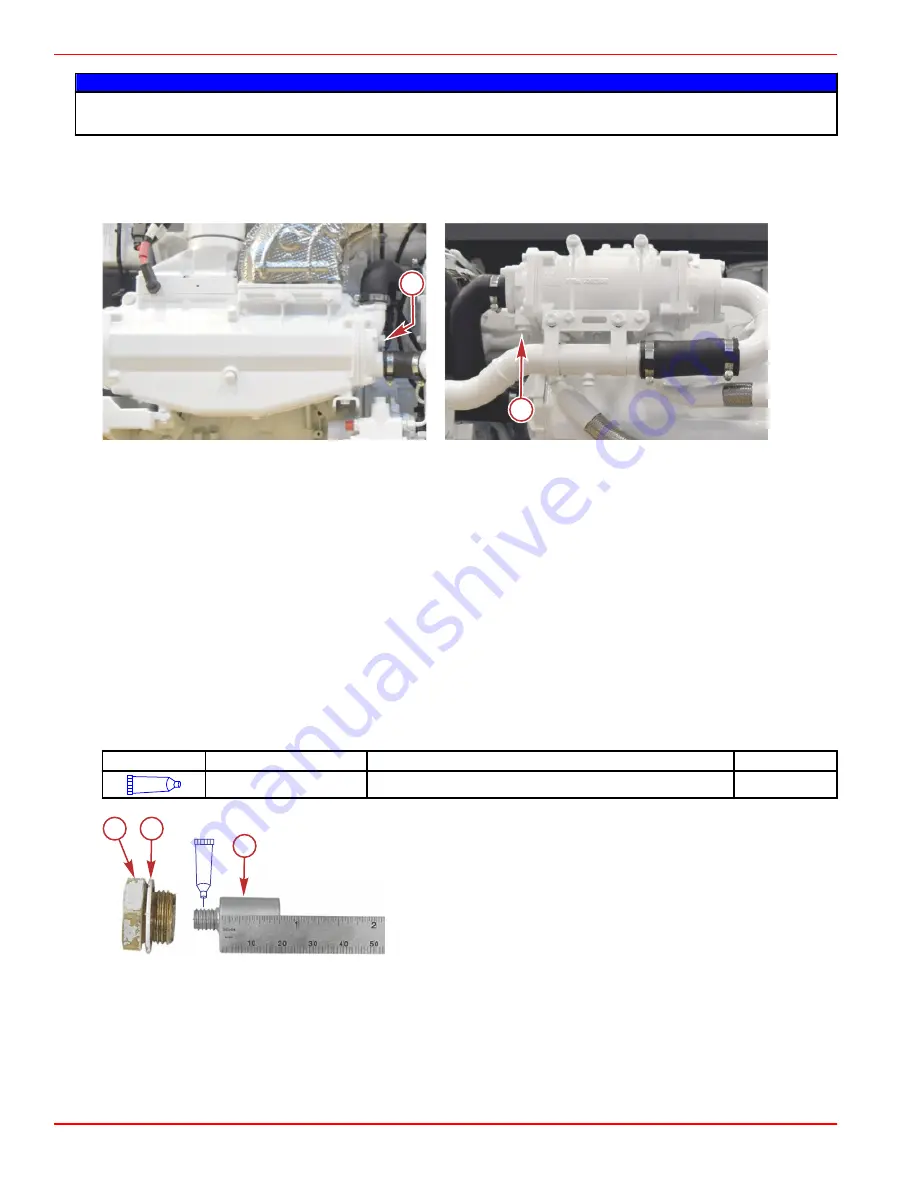
NOTICE
Failure to close the seawater inlet or seacock when removing or replacing the anode plugs can lead to water damage. Close
the seacock or remove and plug the seawater inlet hose to prevent water from entering the anode plug holes.
2. Close the seacock.
3. Remove the two anodes; one from the seawater/air heat exchanger on the port side of the engine, and one from the oil/
seawater heat exchanger on the starboard side of the engine.
NOTE: Removing the anodes will allow water to drain into the boat. Use a suitable container to catch the water.
a -
Seawater/air heat exchanger anode
b -
Oil/seawater heat exchanger anode
Cleaning and Inspection
The inspection and replacement interval will vary depending on the condition of the seawater and the mode of engine
operation.
NOTE: Use sandpaper, a fiber brush, or a cleaning pad to remove the deposits from the surface of each anode before trying to
determine the amount of erosion. Do not use a mild steel brush, which might leave deposits that could accelerate corrosion.
1. Remove the deposits from each anode.
2. Inspect and measure the anodes. Replace the anode if the length is less than 9.5 mm (0.38 in.) or if the nominal diameter
of 14.3 mm (0.56 in.) has been significantly eroded.
a. If replacement is required, remove the zinc anode from the anode hex plug by turning counterclockwise.
b. Apply Loctite 242 Threadlocker to the threads of the new zinc anode and screw it into the anode hex plug until fully
seated.
Tube Ref No.
Description
Where Used
Part No.
66
Loctite 242 Threadlocker
Zinc anode threads
92-809821
New anode shown
a -
Anode plug
b -
Sealing washer
c -
Zinc anode
Anode Installation
1. Inspect each anode sealing washer for damage. Replace as necessary.
2. Install a sealing washer onto each anode and install an anode assembly into the seawater/air heat exchanger, and into the
oil/seawater heat exchanger. Tighten the anodes to the specified torque.
65062
a
b
66048
a
b
c
Section 5 - Maintenance
Page 68
90-8M0117076
eng
FEBRUARY 2018
Summary of Contents for MerCruiser Series
Page 6: ...Page iv 90 8M0117076 eng FEBRUARY 2018...
Page 32: ...Section 2 Getting to Know Your Power Package Notes Page 26 90 8M0117076 eng FEBRUARY 2018...
Page 50: ...Section 4 Specifications Notes Page 44 90 8M0117076 eng FEBRUARY 2018...
Page 80: ...Section 5 Maintenance Notes Page 74 90 8M0117076 eng FEBRUARY 2018...
Page 86: ...Section 6 Storage Notes Page 80 90 8M0117076 eng FEBRUARY 2018...
Page 90: ...Section 7 Troubleshooting Notes Page 84 90 8M0117076 eng FEBRUARY 2018...
Page 98: ...Section 9 Checklists Notes Page 92 90 8M0117076 eng FEBRUARY 2018...