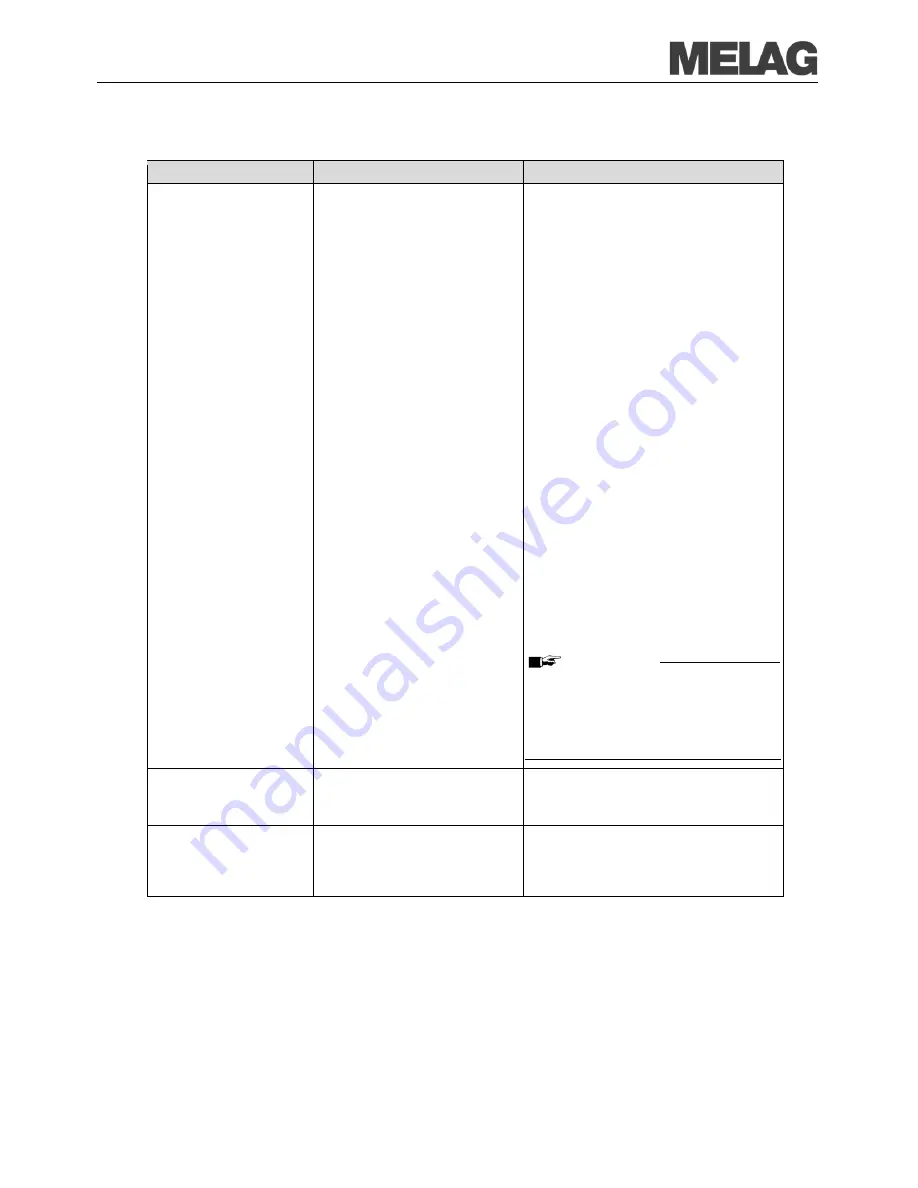
Chapter 9 – Malfunctions
51
Warning message
Possible cause
What you can do
Feed water quality bad/
Exchange cartridge/module
Conductivity of the feed water too
high
≥
40µS
Still possible to start by repeatedly
pressing the K
EY
(S):
Feed water supply from the feed water
container
Empty the feed water container, clean, rinse
with fresh feed water and fill fresh feed
water of the respective quality into the
container.
Feed water supply from water treatment
unit
Mixed-bed resin pellets consumed
MELAdem
40:
Exchange the mixed-bed resin pellets (see
operating manual for the water treatment
unit MELAd
em
40).
Mixed-bed resin pellets in the after
ion exchanger (3
rd
cartridge)
consumed
MELAdem
47
:
Exchange the mixed-bed resin pellets (see
operating manual for the water treatment
unit MELA
dem
47) and examine the water
treatment unit.
On repeated occurrence, have maintenance
carried out by MELAG customer service or
service of the specialist dealer. Possibly the
pre- and activated carbon filter must also be
exchanged.
Mixed-bed resin pellets in reverse
osmosis unit consumed
For different water treatment units:
Change the module/resin cartridge
according to the manufacturer’s instructions.
On repeated occurrence, carry out
maintenance.
PLEASE NOTE
Initiate program start after completion of the
above-mentioned work. On the first start
after maintenance of the water treatment
unit, this warning text can appear once
again since the inlet hose/measuring cell are
still not completely flushed with fresh water.
Feed water quality
insufficient/ No start
possible
Conductivity of the feed water too
high Conductivity
≥
65 µS
Start no longer possible:
See warning message: Feed water quality
insufficient/Exchange cartridge/module
Please wait
Preheating chamber
Message is displayed during
program start phase. The steam
sterilizer has not reached the
starting temperature yet.
The steam sterilizer starts automatically
after reaching the starting temperature.