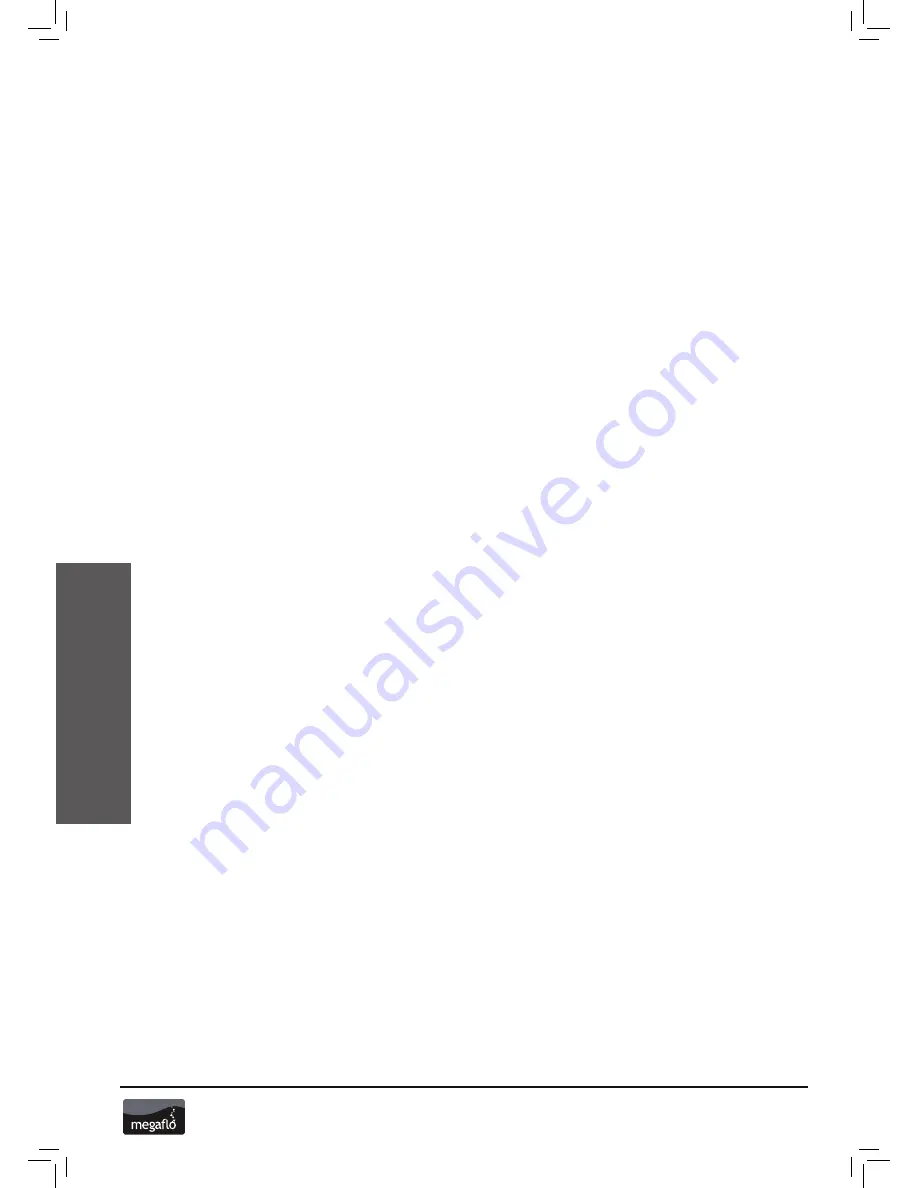
Unvented Hot Water Cylinder
24
MAINTENANCE AND
SER
VICING (3)
Commissioning
Filling and flushing the Megaflo Commercial
Ensure that all fittings and immersion heaters are correctly fitted and tightened.
i)
Open a hot tap furthest from the Megaflo
Commercial
.
ii)
Open the mains stop cock to fill the unit. When water issues from the tap, allow to run for a few
minutes to thoroughly flush through any residue, dirt or swarf, then close tap.
iii)
Open successive hot taps to purge any air from the system.
iv)
Check all connections for leaks and rectify as necessary.
v)
The Strainer housed within the Pressure Reducing Valve should be cleaned to remove any
debris that may have been flushed through the main supply pipe.
Check the operation of the Safety Valves
i)
Slowly, manually open for a few seconds, the Temperature and Pressure Relief Valve (T&P
Valve) situated on the Megaflo
Commercial
unit. Check water discharged runs freely away
through the tundish and discharge pipe work. Close valve, ensure water flow stops and valve
reseats correctly.
ii)
Repeat for the Pressure Relief Valve.
NOTE:
The water discharged may be very hot.
Auxillary
Switch on the electrical supply to the immersion heater(s) and allow the unit to heat up. Check that
the thermostat operates correctly. A storage temperature of approx. 60ºC is recommended, install
and set up immersions as per immersion heater fitting instructions (36006161) . Check that no wa-
ter is discharged from either the Expansion Valve or Temperature and Pressure Relief Valve during the
heating cycle. The thermal cut-out is factory set to 80°C max for direct heating
Primary Side
Fill the indirect (primary) circuit following the boiler manufacturer’s commissioning instructions. To
ensure the primary heating coil in the Megaflo
Commercial
indirect is filled the 2-port motorised
valve (supplied) should be manually opened by moving the lever on the motor housing to the MAN
OPEN position. When the primary circuit is full return the lever to the AUTO position. Vent any
trapped air by opening the air bleed.
If necessary the cylinder water temperature can be adjusted
by turning the knob located on front of the thermostat housing, see fig 12, page21. The minimum
thermostat setting is 30°C. The maximum thermostat setting is 70°C, it is recommended that the
water temperature setting is between 60°C and 65°C for optimum working conditions. The thermo-
static controls contain a thermal cut-out which is set 82°
Benchmark
tm
Log Book
On completion of the installation and commissioning procedures detailed in this Product Guide
the Benchmark
TM
“Installation, Commissioning and Service Record Log” should be completed and
signed off by the competent installer or commissioning engineer in the relevant sections. The various
system features, location of system controls, user instructions and what to do in the event of a sys-
tem failure should be explained to the customer. The customer should then countersign the Bench-
mark
TM
commissioning checklist to accept completion. The Service Record should be filled in when
any subsequent service or maintenance operation is carried out on the Megaflo
Commercial
unit.
See pages 33 and 34 for Benchmark
TM
logbook and service record
Summary of Contents for Commercial 1000
Page 33: ...Unvented Hot Water Cylinder 33 MAINTENANCE AND SERVICING 3...
Page 34: ...Unvented Hot Water Cylinder 34 MAINTENANCE AND SERVICING 3...
Page 35: ...Unvented Hot Water Cylinder 35 USER GUIDE 4 NOTES...
Page 39: ...Unvented Hot Water Cylinder 39 USER GUIDE 4...
Page 40: ...Unvented Hot Water Cylinder 40 2011 7032408_issue_01...