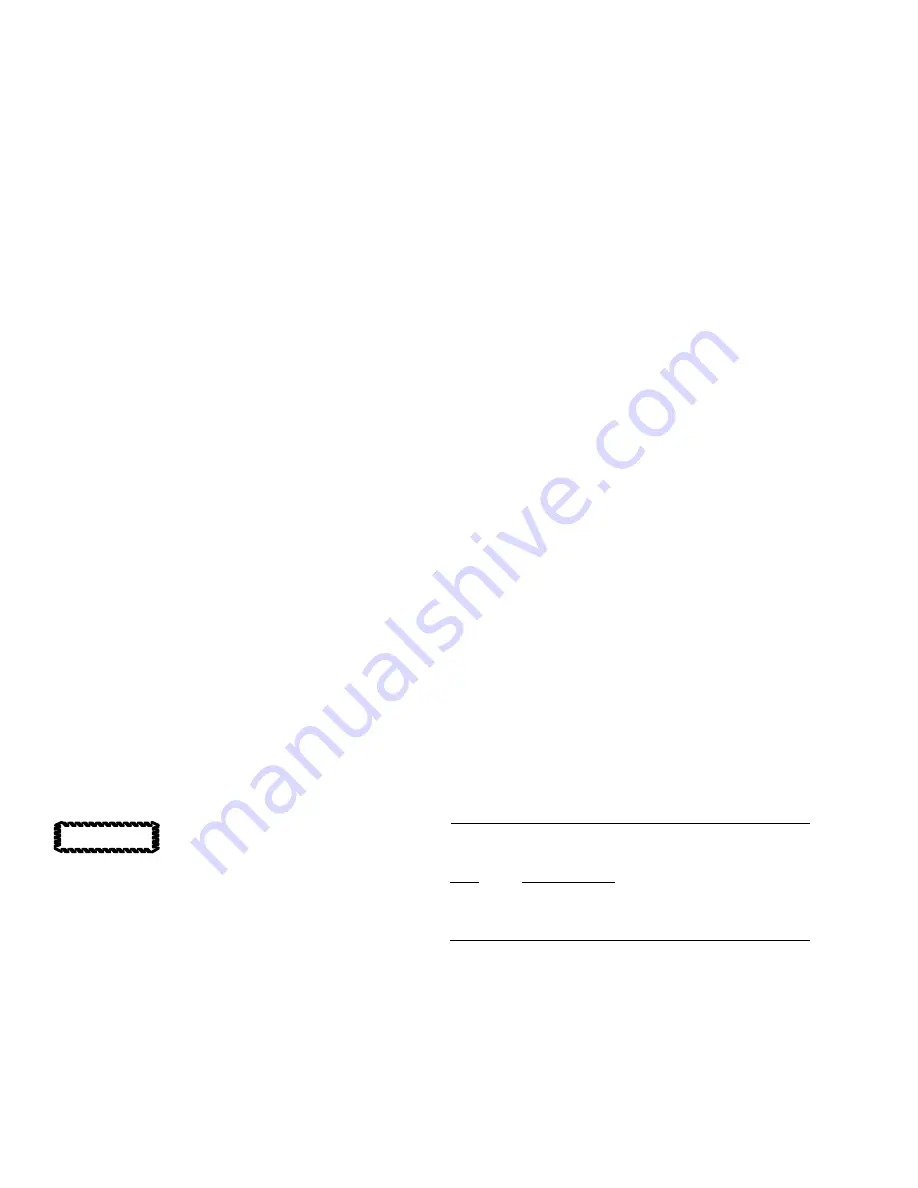
CSP−HMI−2
MD Helicopters, Inc
.
MAINTENANCE MANUAL
Page 208
Revision 39
53−40−30
NOTE:
Refer to MD Helicopters Inc. Represen-
tative for structural repairs, cracks, etc.
9. Stationary Thruster Cone Replacement
A. Stationary Thruster Cone Removal
(1). Remove rotating thruster cone (Ref.
Rotating Thruster Cone Removal).
(2). Remove eight off wing screws from pan
cover, remove cotter pin, nut and
washer from sector input shaft and
remove pan cover. Remove washer and
bushing from sector bellcrank input
shaft.
(3). Remove bolt, washer and bushing from
thruster input sector bellcrank clevis
(Ref. View J).
(4). Remove thruster cone fairings.
(5). Support stationary thruster cone and
remove eight bolts and washers, with
cable assembly attached to cone,
carefully lift cone off tailboom so that
the control rod passes through the
thruster cone cutout.
B. Stationary Thruster Cone Installation
(1). Support stationary thruster cone to
tailboom so that the control rod passes
through the cutout of the stationary
cone, and that the mating surfaces are
flush to the tailboom. Slide counter-
sunk/chamber washers on external
wrenching bolts with countersunk side
facing bolt head.
If washers are installed back-
wards, structural failure may
result due to insufficient surface clamp−up
in load bearing areas that can cause spread-
ing or cracking, resulting in loss of clamp−
up torque.
(2). With the stationary thruster cone
support in place, install eight bolts and
washers. Torque bolts
30 − 40 inch−
pounds (3.39 − 4.52 Nm) plus drag
torque.
(3). Connect control rod to input sector
bellcrank clevis and install bushing,
washer and bolt, torque bolt per
standard aircraft torque values and
safety wire.
(4). Install thruster cone fairings.
(5). Install rotating thruster (Ref. Rotating
Thruster Cone Installation).
10. Stationary Thruster Cone Inspection
(1). Inspect for cracks and delamination of
composites structure for the following:
Internal ducts, air foil supports, pan
cover and pan (hat section).
(2). Inspect rollers and bearings for condi-
tion and freedom of rotation. Inspect for
cleanliness.
(3). Inspect sector bellcrank, cable assem-
blies, pulleys and support brackets for
condition, inspect of cleanliness.
(4). Inspect upper input shaft for damage
and wear. Check for play in mounting
pins. If mounting pins are found to
have play, replace with new pins and
collars.
(5). Inspect thruster aft support shaft for
damage and wear. Check for play in
mounting hardware. If top bolt is found
to be loose, retorque to
10 − 15 inch−
pounds (1.13 − 1.69 Nm)
. If bottom
mounting pins are found to be loose,
replace with new pins and collars.
11. Conduit and Support Strap Rebonding
(Ref. Figure 203) The following procedure is for
rebonding of the conduit supports.
Consumable Materials
(Ref. Section 91
−
00
−
00)
Item
Nomenclature
Isopropyl alcohol
Adhesive
(1). Lightly abrade faying surfaces with
Scotchbrite until surface gloss of the
laminate is gone.
(2). Solvent−wipe parts using a clean
lint−free cloth dampened with isopropyl
alcohol (CM217).
CAUTION