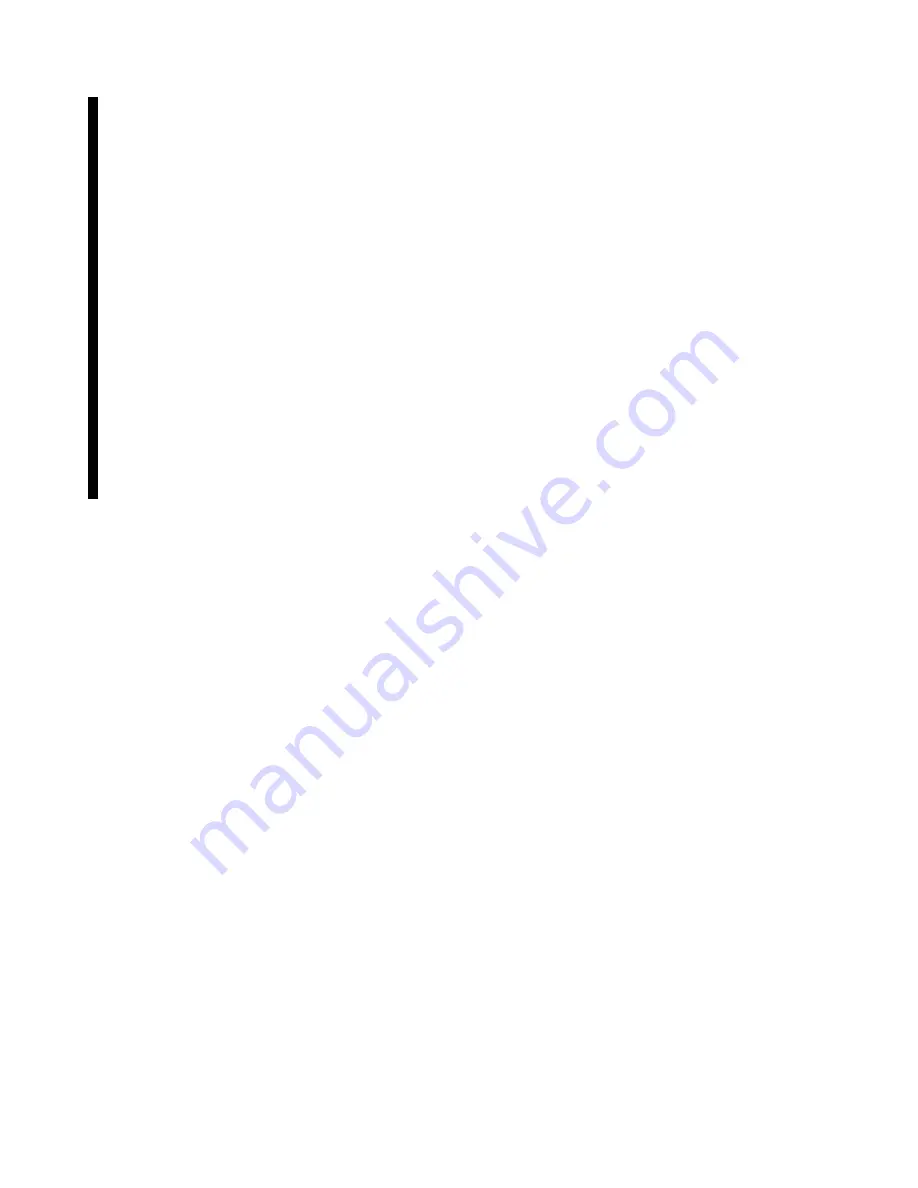
CSP−HMI−2
MD Helicopters, Inc
.
MAINTENANCE MANUAL
67−10−00
Page 603
Revision 28
(b). Back off jam nut sufficiently enough
to inspect insert.
(c). Inspect insert for proper installation,
flush to a maximum of 0.010 inch
(0.254 mm) below the surface of the
rod.
(d). Check that insert is tight inside of
rod.
1). If insert is loose or protrudes above
surface of rod, rod assembly is
unserviceable and must be repla-
ced.
2). If insert is tight and swaged flush
to 0.010 inch (0.254 mm) below the
surface of the rod, rod is servi-
ceable.
(e). Reconnect rod to control system and
tighten jam nut.
(8). Check rigging of re−connected control
system.
2. Controls Support Bracket and Bellcrank
Inspection
(1). Inspect bearings in bellcranks for
binding.
(2). Perform fluorescent dye penetrant
inspection on any suspected part.
NOTE:
Parts identified with double asterisk
(**) (Ref. Figure 403) may be either magne-
sium or aluminum alloy. (For corrosion con-
trol and identification of magnesium and
aluminum alloys, Ref. Sec. 20−40−00.)
3. Pilot’s Collective Pitch Stick Inspection
(1). Inspect bearings for binding or play.
(2). Inspect all gears for cracks, and
chipped or broken teeth.
(3). Inspect stick tube and gas producer
control tube for corrosion, deformation
and loose rivets.
NOTE:
Pitch stick housing and cap may be ei-
ther magnesium or alloy casting. (For corro-
sion control and identification of magne-
sium or aluminum alloys, Ref. Sec.
20−40−00.)
4. Copilot’s Collective Pitch Stick Inspection
(1). Inspect bearings for binding or play.
(2). Inspect all gears for cracks, and
chipped or broken teeth.
(3). Inspect stick tube and gas producer
control tube for corrosion, deformation
and loose rivets.
5. Collective Stick Friction Mechanism
Operational Check
(1). Remove guard from collective stick.
(2). Check that teeth of friction drive gear,
idler gear, and driven gear are not
stripped or otherwise damaged.
(3). Rotate friction drive gear grip counter-
clockwise to maximum friction stop;
gear train must rotate freely. Check
position of shaft assembly pin. Pin
should be at highest point of cam.
(4). If pin is not at approximate peak of cam
or has overridden peak, friction mecha-
nism must be readjusted. If pin is in
correct position, continue with step (5).
below.
(5). Rotate drive gear grip clockwise to
minimum friction position and release
grip; gear train must rotate freely. Pin
should be at approximate low point of
cam.
(6). With pin on low point of cam, hand
rotate spring release housing. If there is
drag on retainer, there is friction on
guide and collective friction must be
readjusted. If retainer rotates freely,
without obvious play, low point friction
setting is correct.